Key Takeaway
Servo control in process control refers to the regulation of a motor’s speed, position, and torque to achieve precise control over a process. This is accomplished using feedback loops that continuously monitor the output of the system and make adjustments to minimize errors. The goal of servo control is to maintain the desired process conditions, such as temperature, pressure, or flow rate, with high accuracy.
In process automation, servo control systems are critical for enhancing efficiency and consistency. They ensure that processes operate smoothly and within specified parameters, making them essential in industries like manufacturing, robotics, and automation, where precise control over machinery is crucial.
Introduction to Servo Control in Process Automation
Servo control systems are a cornerstone of modern process automation. They function by continuously adjusting a system’s output to match a desired setpoint, ensuring precision in tasks like positioning, speed regulation, and force control. For instance, in a robotic arm used in manufacturing, servo control ensures that the arm moves to the exact location needed, with the correct speed and force, every time. This level of precision is crucial in applications where even a tiny deviation can result in defective products or unsafe conditions. Understanding servo control is essential for anyone looking to enhance their process automation skills.
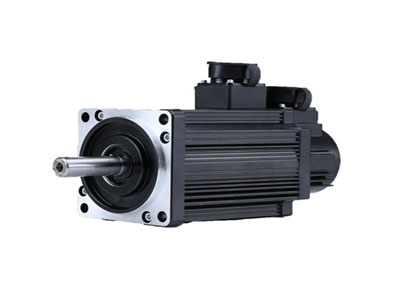
How Servo Control Systems Enhance Process Efficiency
Servo control systems are fundamental to improving process efficiency in modern industrial operations. Imagine you’re working on a production line, where consistency and speed are crucial. A servo-controlled motor can dynamically adjust its speed in real-time to match the immediate demands of the process. For instance, if there’s a slight delay or a sudden change in the load, the servo system responds almost instantaneously to correct it. This real-time adaptability is a game-changer. It significantly reduces energy consumption by ensuring that the motor only works as hard as it needs to at any given moment, avoiding unnecessary power usage.
Moreover, by minimizing mechanical stress through precise control, servo systems extend the life of machinery. Fewer breakdowns and lower maintenance costs are direct benefits, contributing to a smoother, more reliable operation. Imagine the costs saved when machines run efficiently without frequent interruptions. And it’s not just about saving money—this efficiency translates to higher throughput. With fewer errors and quicker adjustments, the production process becomes faster, leading to an increase in overall output. The precision of servo control also means that product quality is consistently high, as the system can maintain tight tolerances, reducing defects and rework. As an engineer, recognizing the value that servo systems bring to optimizing industrial operations is essential for driving both productivity and profitability in any manufacturing environment.
Key Components of a Servo Control System
Understanding the key components of a servo control system is crucial for any engineer stepping into the world of industrial automation. Let’s break it down. At the heart of the system is the controller—think of it as the brain. The controller is responsible for sending precise commands based on the desired setpoint, whether it’s positioning, speed, or torque. These commands are then executed by the motor, which acts as the muscle of the operation, doing the physical work according to the instructions it receives.
But how does the system know if the motor is performing correctly? This is where the feedback device comes into play, typically an encoder. The encoder constantly monitors the motor’s output—its position, speed, and so on—and sends this data back to the controller. This feedback loop is what makes servo systems so precise. If there’s any deviation from the desired setpoint, the controller adjusts its commands to bring the system back in line.
Finally, we have the drive, which serves as the intermediary between the controller and the motor. The drive converts the controller’s digital commands into electrical signals that the motor can understand and act upon. It’s the link that ensures the motor receives the right amount of power to execute its task precisely. Understanding how these components interact allows engineers to troubleshoot issues more effectively and design systems that are both efficient and reliable. With this knowledge, you’ll be better equipped to optimize the performance of servo control systems in any industrial application.
Practical Applications of Servo Control in Industry
Servo control systems are integral to the efficiency and precision of numerous industries, and their adaptability makes them a cornerstone of modern manufacturing processes. Take the automotive industry, for example. Here, servo systems are essential in operating assembly robots that place components with pinpoint accuracy, ensuring that every part of a vehicle is assembled correctly. These systems also play a critical role in testing equipment, where they provide the exact force or speed needed to test components under real-world conditions, guaranteeing that only high-quality parts make it into the final product.
In the food and beverage industry, precision is equally crucial. Servo control systems manage filling machines, ensuring that each bottle or package is filled with the exact amount of product. This not only maintains consistency in product quality but also reduces waste, which is vital in an industry with tight margins. Similarly, in the textile industry, servo systems are employed in weaving and knitting machines to maintain consistent tension and speed, which is essential for producing high-quality fabrics. The versatility of servo control is what makes it so valuable across these diverse applications. As an engineer, understanding how servo systems are utilized in different industries helps you appreciate their broad impact on modern manufacturing, making you more equipped to innovate and optimize processes within your field.
Challenges and Solutions in Implementing Servo Control
While the benefits of servo control systems are clear, their implementation can present several challenges, particularly for engineers new to the technology. One of the most common issues is tuning the system to achieve the desired performance without causing instability. Servo systems need to be fine-tuned so that they respond quickly to changes without overshooting the target. If not properly tuned, the system might oscillate, causing fluctuations that can disrupt the process or lead to wear and tear on the machinery. This is where hands-on experience becomes invaluable—knowing how to tweak the system parameters to achieve the right balance is a skill developed through practice and understanding.
Another challenge lies in integrating servo systems with existing machinery. Often, older machines were not designed with modern servo controls in mind, requiring custom modifications to accommodate new technology. This can be a complex process, involving retrofitting equipment and ensuring that all components work harmoniously together. However, these challenges are not insurmountable. By thoroughly understanding the system’s requirements and continuously updating your knowledge through training and real-world application, you can overcome these hurdles. The key is to approach each challenge as an opportunity to learn and innovate, ensuring that your servo control implementation not only succeeds but also sets a new standard for efficiency and reliability in your industry.
Conclusion
Servo technology is an essential tool for optimizing process control in a wide range of industries. Its ability to provide precise, real-time adjustments makes it invaluable for maintaining quality and efficiency in complex systems. By mastering servo control, engineers can significantly improve the performance of automated processes, leading to increased productivity and reduced costs. As industries continue to evolve and demand greater precision and efficiency, the role of servo control will only become more critical. Embracing this technology and its applications will be a key factor in staying competitive in the ever-advancing world of industrial automation.