Key Takeaway
Intelligent manufacturing, also known as smart manufacturing, uses advanced technologies like automation, data collection, AI, and machine learning to optimize production processes. By integrating human capabilities with machines and processes, it creates an adaptable and responsive production environment. Technologies like IoT and robotics enhance real-time decision-making, leading to better product quality and faster responses to market demands. Intelligent manufacturing improves efficiency by streamlining operations and reducing costs. It allows for predictive maintenance, minimizing downtime and extending equipment life. Adopting intelligent manufacturing
Defining Intelligent Manufacturing in the Context of Industry 4.0
Intelligent manufacturing is closely tied to the concept of Industry 4.0, which emphasizes the digitalization of manufacturing through advanced technologies. In Industry 4.0, factories are equipped with smart systems that collect, process, and act on real-time data, enabling the automation of decision-making processes. Intelligent manufacturing takes this a step further by creating interconnected production systems where machines, sensors, and software can communicate with each other to optimize processes without human intervention.
The core idea behind intelligent manufacturing is to achieve a higher level of flexibility and efficiency. For instance, production lines can automatically adjust to changes in customer demand or raw material availability. Intelligent manufacturing also incorporates predictive maintenance, where machines anticipate breakdowns before they occur, minimizing downtime and improving productivity.
For engineers, this new era of manufacturing requires a deep understanding of data-driven technologies and how to integrate them into existing systems. It’s about moving beyond traditional manufacturing methods and embracing intelligence-driven processes to create smarter, more efficient factories.
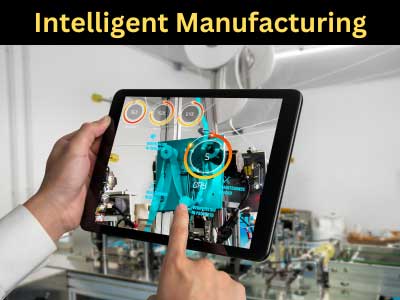
How AI and Data Analytics Transform Production Processes
The use of artificial intelligence (AI) and data analytics in intelligent manufacturing is revolutionizing production processes. AI enables machines to learn from data, make predictions, and optimize their performance without needing constant human input. In combination with data analytics, AI can analyze massive amounts of information from production lines, supply chains, and even customer feedback to find patterns and opportunities for improvement.
For example, AI systems in manufacturing can predict which machines are likely to fail based on historical data, allowing engineers to perform predictive maintenance before any disruptions occur. This reduces downtime and extends the lifespan of equipment. AI also enhances quality control by identifying defects during production in real-time and making adjustments to processes to ensure that products meet exacting standards.
Data analytics plays a critical role in process optimization. Engineers can monitor production data in real-time to detect inefficiencies, such as energy consumption spikes or bottlenecks in the workflow. By addressing these issues quickly, manufacturers can save time and resources while maintaining optimal performance.
Moreover, AI-powered systems can self-optimize, meaning that they learn from past data and automatically adjust parameters to enhance efficiency. This not only increases productivity but also ensures that manufacturers can remain competitive in a fast-evolving market. As AI and data analytics become more embedded in manufacturing, engineers must develop expertise in using these tools to drive performance and innovation.
The Role of IoT in Connecting Intelligent Manufacturing Systems
The Internet of Things (IoT) is a foundational technology for intelligent manufacturing, enabling seamless connectivity between machines, devices, and systems across the factory floor. IoT devices, such as sensors and controllers, collect data on various aspects of the manufacturing process, including temperature, pressure, machine status, and product quality. This data is then sent to a central system for analysis and action.
For example, IoT sensors can detect when a machine is operating outside its optimal range and automatically trigger adjustments or send alerts to engineers. This continuous flow of data allows for real-time monitoring and control, ensuring that production runs smoothly and efficiently.
IoT also facilitates interconnectivity, where machines can communicate with each other and share information to optimize workflows. In an intelligent manufacturing system, IoT-enabled machines can adjust their operations based on data from other machines in the line. This means that if one machine slows down due to maintenance, others can speed up to compensate, minimizing any disruption in production.
For engineers, understanding how to leverage IoT technology is key to unlocking the full potential of intelligent manufacturing. IoT enables manufacturers to create a truly connected, responsive, and flexible factory where decision-making is not just data-driven but data-enabled.
Benefits of Predictive Maintenance in Intelligent Manufacturing
Predictive maintenance is one of the standout features of intelligent manufacturing. Unlike traditional maintenance, which relies on fixed schedules or reactive repairs after a breakdown, predictive maintenance uses data to forecast when machines are likely to fail. By monitoring parameters such as temperature, vibration, or noise levels, engineers can identify signs of wear and tear early, preventing costly downtime.
In an intelligent manufacturing system, sensors continuously collect data from machinery, and AI algorithms analyze this data to predict future malfunctions. This allows engineers to perform maintenance just-in-time, replacing parts or tuning machines before issues escalate into larger problems. Predictive maintenance reduces downtime, lowers repair costs, and extends the life of equipment.
Another significant benefit is the increased efficiency in resource allocation. By predicting exactly when maintenance is needed, manufacturers can avoid over-maintenance, where machines are serviced more frequently than necessary, leading to unnecessary costs. Instead, resources are deployed only when and where they are needed most.
Engineers need to be familiar with predictive maintenance tools and techniques, as these systems will be integral to maintaining high levels of productivity in smart factories. Predictive maintenance ensures that production lines run smoothly with minimal interruptions, leading to increased profitability and operational efficiency.
Differences Between Traditional and Intelligent Manufacturing
The shift from traditional manufacturing to intelligent manufacturing is driven by technological advancements that allow for more automation, data utilization, and flexibility. Traditional manufacturing typically relies on fixed processes, manual intervention, and reactive problem-solving. In contrast, intelligent manufacturing uses data-driven systems, real-time monitoring, and autonomous machines to optimize every stage of production.
In traditional manufacturing, manual decision-making is often required to address issues such as equipment failure or quality defects. Engineers or operators must analyze data manually and make adjustments. This can be time-consuming and error-prone. In intelligent manufacturing, AI and machine learning algorithms automatically detect problems and suggest solutions without human intervention.
Another key difference is the ability of intelligent systems to adapt to changing conditions. For instance, if a supply chain disruption occurs, an intelligent system can quickly reallocate resources and adjust production schedules. Traditional systems, by contrast, may experience significant delays and require extensive manual adjustments.
Lastly, intelligent manufacturing systems are more scalable and flexible. Traditional systems may struggle to handle variations in production volume or complexity, whereas intelligent systems can easily adjust to new demands. This adaptability makes intelligent manufacturing more efficient, cost-effective, and responsive to modern market dynamics.
Conclusion
Intelligent manufacturing represents a major leap forward in how factories operate, driven by AI, IoT, and data analytics. By integrating these technologies, manufacturers can create systems that are more flexible, efficient, and responsive to changing market demands. Engineers in intelligent manufacturing environments have the ability to harness real-time data, optimize production processes, and predict issues before they become costly problems.
The true impact of intelligent manufacturing lies in its ability to self-optimize, adapt to dynamic conditions, and enhance productivity while minimizing waste. As this technology continues to evolve, it will transform industries across the globe, making production faster, smarter, and more sustainable.