Key Takeaway
A good manufacturing efficiency typically falls between 85% and 100%. Achieving 85% is considered world-class and indicates that your production process is highly optimized, with minimal waste, downtime, and defects. Reaching 100% means perfect efficiency, where every aspect of production is running at its full potential without any losses.
Most manufacturing companies, however, operate within the 60-80% range. This suggests there is room for improvement in areas like equipment uptime, production speed, or product quality. Striving to move closer to the 85% mark can lead to significant gains in productivity and cost savings, making your manufacturing operations more competitive and efficient.
Defining ‘Good’ Efficiency in Different Industries
The definition of “good” manufacturing efficiency can differ significantly across various industries. In high-volume industries like automotive manufacturing, good efficiency typically means operating at 85% to 95% efficiency, where small improvements can lead to significant cost savings due to the large scale of operations. In contrast, industries like pharmaceuticals or aerospace, which involve more complex and regulated processes, might consider 75% to 85% efficiency as good due to the stringent quality control and precision required. It’s important to tailor efficiency goals to the specific needs and challenges of the industry. For example, in the food and beverage industry, maintaining consistent efficiency while adhering to safety regulations is critical. Understanding these industry-specific benchmarks is essential for setting realistic and achievable efficiency targets that align with business goals and customer expectations.
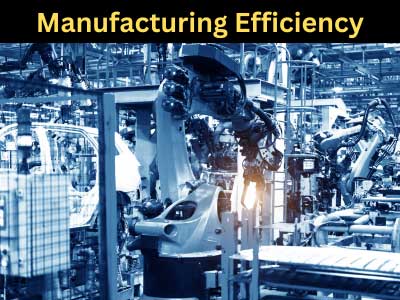
Industry Benchmarks for Manufacturing Efficiency
Industry benchmarks for manufacturing efficiency provide a reference point that helps companies understand where they stand compared to their peers. These benchmarks are typically derived from industry-wide surveys and studies that analyze the performance of various manufacturers within a sector. For instance, in the automotive industry, a manufacturing efficiency of 85% to 95% is often considered the gold standard. This high level of efficiency is achievable due to the highly automated and standardized nature of automotive production lines, where precision and speed are paramount.
In contrast, the pharmaceutical industry, which deals with more complex and regulated manufacturing processes, often sees benchmarks ranging from 75% to 85%. This is because the production of pharmaceuticals involves rigorous quality control measures, which can slow down the process but are essential for ensuring the safety and efficacy of the products. Similarly, in the electronics industry, where precision and quality are crucial, benchmarks might be slightly lower, around 80% to 90%, depending on the complexity of the products being manufactured.
These benchmarks are not just numbers; they represent the collective experience and best practices of leading companies within an industry. By understanding and striving to meet or exceed these benchmarks, manufacturers can improve their competitiveness, reduce waste, and increase profitability. However, it’s important to remember that benchmarks should be tailored to the specific circumstances of each manufacturing operation, as factors like production scale, product complexity, and market demands can all influence what is considered a “good” level of efficiency.
How to Measure and Improve Efficiency
Measuring and improving manufacturing efficiency involves a systematic approach that starts with accurate data collection. The first step is to establish your standard output rate, which represents the ideal number of units that should be produced under optimal conditions. Once you have this baseline, you can measure your actual output rate over a given period and use the manufacturing efficiency formula: (Actual Output / Standard Output) × 100. This will give you a percentage that reflects how efficiently your operation is running.
Improving efficiency requires identifying the factors that are causing deviations from the standard output rate. This could involve analyzing downtime, machine performance, labor utilization, and material waste. By pinpointing the specific areas where inefficiencies occur, you can implement targeted improvements. For instance, if downtime is a major issue, investing in preventive maintenance and better scheduling could significantly boost efficiency. Similarly, if material waste is high, revisiting your procurement and inventory management practices might be necessary.
Continuous monitoring and adjustment are key to maintaining and improving efficiency. Implementing lean manufacturing techniques, such as 5S, Kaizen, and Six Sigma, can help streamline processes and eliminate waste. Additionally, leveraging technology, such as Manufacturing Execution Systems (MES) and IoT-enabled devices, provides real-time data that can be used to make informed decisions and drive continuous improvement. Regularly reviewing efficiency metrics and making data-driven adjustments ensures that your manufacturing processes remain optimized and competitive.
Key Factors Influencing Manufacturing Efficiency
Several key factors influence manufacturing efficiency, and understanding these can help you optimize your production processes. Time management is one of the most critical factors; how well you manage production schedules and minimize downtime directly impacts efficiency. Poor time management can lead to bottlenecks, idle machinery, and missed deadlines, all of which reduce overall efficiency.
Resource utilization is another crucial factor. This involves the optimal use of materials, labor, and equipment. Efficient resource utilization means that materials are used without waste, labor is allocated effectively, and machinery is maintained and operated at peak performance. When resources are not used efficiently, it can lead to increased waste, higher production costs, and lower overall efficiency.
Process optimization also plays a significant role. This involves continuously analyzing and improving production processes to eliminate inefficiencies, reduce waste, and increase output. Techniques such as lean manufacturing and Six Sigma are often used to optimize processes and improve efficiency. By focusing on these factors, manufacturers can significantly improve their efficiency, reduce costs, and enhance competitiveness.
Lastly, workforce training and engagement are vital. A well-trained and motivated workforce is more likely to follow best practices, operate machinery efficiently, and identify potential areas for improvement. Regular training sessions, clear communication, and involving employees in the decision-making process can lead to higher efficiency and better overall performance.
Case Studies of High-Efficiency Operations
High-efficiency operations are often the result of a strategic focus on continuous improvement, process optimization, and effective use of resources. For example, Toyota’s production system, known for its lean manufacturing principles, has become a global benchmark for efficiency. Toyota’s emphasis on Just-In-Time (JIT) production and Kaizen (continuous improvement) has allowed the company to maintain high levels of efficiency, reduce waste, and produce vehicles with minimal defects. By focusing on eliminating non-value-added activities, Toyota has set the standard for efficient manufacturing in the automotive industry.
Another example comes from the electronics manufacturing sector, where a leading global manufacturer implemented automation across its production lines. By automating repetitive tasks and integrating robotics into assembly processes, the company was able to increase production speed and consistency, achieving an efficiency rate of over 95%. This high level of efficiency not only reduced labor costs but also allowed the company to scale its operations rapidly while maintaining high quality.
In the pharmaceutical industry, a company focused on optimizing its batch production processes to improve efficiency. By analyzing production data and implementing process improvements, they were able to reduce cycle times and increase throughput. This not only improved their manufacturing efficiency but also reduced costs and improved their ability to meet customer demand.
These case studies highlight the importance of adopting best practices and leveraging technology to achieve high levels of manufacturing efficiency. By learning from these examples, manufacturers can implement similar strategies in their own operations to drive efficiency, reduce costs, and remain competitive in their respective industries.
Conclusion
Achieving and maintaining optimal manufacturing efficiency is a continuous process that requires a strategic approach and a commitment to improvement. It involves understanding industry benchmarks, accurately measuring efficiency, and addressing the key factors that influence it, such as time management, resource utilization, and process optimization. High-efficiency operations not only reduce costs and increase profitability but also enhance product quality and customer satisfaction.
By learning from industry leaders and implementing best practices such as lean manufacturing, automation, and continuous improvement, manufacturers can drive significant gains in efficiency. The use of advanced tools and technology, such as Manufacturing Execution Systems (MES) and IoT-enabled devices, further enhances the ability to monitor, analyze, and optimize production processes in real-time.