Key Takeaway
Factory automation uses a variety of equipment to improve production efficiency. Key components include robotics systems for tasks like assembly and packaging, and Programmable Logic Controllers (PLCs) that control machinery operations.
Sensors and actuators provide real-time data and carry out actions based on that data, ensuring smooth operations. Human-Machine Interfaces (HMIs) allow operators to interact with automated systems. Additionally, conveyors and Automated Guided Vehicles (AGVs) move materials efficiently across factory floors. Together, these tools enhance productivity, reduce errors, and optimize manufacturing processes.
Robotics: Automating Repetitive Tasks
Robotics plays a vital role in factory automation, handling repetitive, dangerous, or precision tasks that humans find challenging. Unlike humans, robots don’t tire, making them ideal for long hours of error-free operations such as welding, assembly, and material handling. In automated factories, robots perform tasks like assembling car parts or packing goods. Collaborative robots (cobots) are gaining popularity, working alongside humans to improve safety and productivity without replacing human workers. Powered by machine vision, robots can make real-time decisions and adapt to variations in the production process. As factories evolve, robotics will continue expanding automation’s possibilities, increasing efficiency and flexibility.
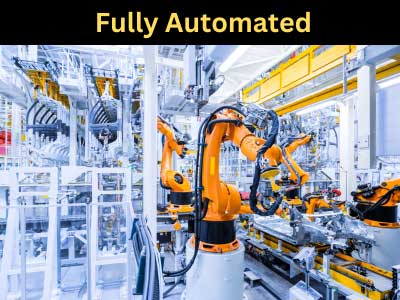
Conveyor Systems: Enhancing Material Handling
Conveyor systems are the backbone of material handling in most automated factories. These systems are designed to move products, materials, or components between different stages of production without manual intervention. This not only speeds up the manufacturing process but also ensures consistent and reliable movement of goods through the factory.
There are various types of conveyor systems, each suited to different industries. Belt conveyors, for instance, are used in industries like food processing, where fragile or soft products need to be transported gently. On the other hand, roller conveyors are commonly found in warehouses and distribution centers where heavy or bulky items need to be moved.
What makes conveyors essential in factory automation is their ability to integrate with other systems. Conveyor systems can work alongside robots, programmable logic controllers (PLCs), and sensors to ensure that materials arrive at the right place at the right time, keeping production smooth and efficient. In automated factories, conveyors are often the unseen heroes, quietly ensuring that the entire production process runs like clockwork.
You May Like to Read
Sensors: Monitoring Processes and Ensuring Safety
In an automated environment, sensors are the eyes and ears of the system. These devices monitor every aspect of the production process, ensuring that machines are functioning correctly, materials are in place, and products meet quality standards. Sensors can detect everything from temperature and pressure to speed and position, and they play a crucial role in maintaining the safety and efficiency of an automated system.
In terms of safety, proximity sensors and light curtains are commonly used to ensure that machines don’t operate when a human is too close. This reduces the risk of accidents and injuries in environments where heavy machinery is in use. In addition to safety, sensors provide real-time data that allows for predictive maintenance. For example, vibration sensors can detect when a machine part is starting to wear out, signaling the need for maintenance before a breakdown occurs.
Sensors also help with quality control. By using vision systems and other types of sensors, factories can inspect products during each stage of production, catching defects early and ensuring that only high-quality products reach customers. As automation grows, so too will the importance of sensors in maintaining seamless, safe, and high-quality production processes.
Programmable Logic Controllers (PLC): Core Control Systems
At the heart of factory automation lies the Programmable Logic Controller (PLC). These devices serve as the central control units for automated systems, processing inputs from sensors and other devices to execute specific tasks in the production line. Think of PLCs as the brains behind the machinery—they manage everything from the speed of conveyor belts to the movements of robotic arms, based on programmed instructions.
PLCs are known for their reliability and flexibility. They can be programmed to handle various tasks and are robust enough to operate in harsh industrial environments, such as those with extreme temperatures, humidity, or dust. In a fully automated factory, PLCs work in conjunction with other systems, such as Human-Machine Interfaces (HMIs) and Supervisory Control and Data Acquisition (SCADA) systems, to provide real-time control and monitoring.
What makes PLCs especially valuable is their ability to integrate with a wide range of equipment. Whether it’s a robot, conveyor, or sensor, the PLC ensures that every piece of machinery works together in harmony. As factories continue to adopt more complex automation solutions, the role of PLCs will only grow, providing a flexible and scalable solution for managing operations.
Human-Machine Interfaces (HMI): Interacting with Automation Systems
In an automated factory, Human-Machine Interfaces (HMIs) are the tools that allow operators to interact with the automation system. HMIs provide a visual representation of the production process, displaying critical information such as machine performance, sensor readings, and system alerts. They serve as the bridge between human operators and machines, ensuring that even in highly automated environments, humans can still monitor and control the system.
HMIs are designed to be intuitive and user-friendly, allowing operators to adjust parameters, troubleshoot issues, and monitor progress in real time. Whether it’s a touchscreen panel or a computer-based interface, an HMI provides operators with the information they need to make informed decisions. In some systems, HMIs can even alert operators to potential problems before they occur, thanks to the integration of sensors and predictive maintenance tools.
As automation continues to evolve, HMIs will play an increasingly important role in making complex systems manageable for human operators. They ensure that even in a fully automated factory, humans remain an integral part of the process, overseeing and optimizing operations to achieve the best possible outcomes.
Conclusion
In summary, factory automation is built on a foundation of essential equipment, each playing a critical role in creating a seamless production environment. Robotics, conveyor systems, sensors, PLCs, and HMIs work together to ensure that manufacturing processes are efficient, safe, and high-quality. As industries continue to push toward full automation, these technologies will evolve and become even more interconnected, allowing factories to reach new levels of productivity. Whether you’re a new engineer or a seasoned professional, understanding the equipment behind factory automation is key to driving innovation in the industrial world.