Key Takeaway
Additive manufacturing is transforming the manufacturing industry by offering faster prototyping, reduced waste, and increased customization. It allows the production of highly complex parts that would be challenging to create with traditional methods. Innovations like metal 3D printing and bioprinting are pushing the boundaries of what’s possible.
However, there are still challenges, such as limited material options and high initial costs. Despite these hurdles, the ability to produce on-demand parts and reduce dependency on complex supply chains makes it likely that additive manufacturing will become a major part of the future of production.
Current Trends in Additive Manufacturing
In recent years, additive manufacturing has gained significant traction, moving beyond prototyping and into full-scale production. Industries such as aerospace, healthcare, automotive, and consumer goods have embraced this technology to improve production efficiency and offer mass customization. One of the key trends is the growing demand for on-demand production, where manufacturers can print parts as needed, reducing inventory and waste.
Another trend is the shift from using only plastics to incorporating metals and composites. Advances in powder bed fusion and direct metal laser sintering (DMLS) have made it possible to print high-strength, functional metal parts, leading to applications in aviation and automotive industries.
Furthermore, the rise of distributed manufacturing—where parts are printed closer to their point of use—allows for faster delivery times, reduced shipping costs, and a more agile supply chain. As these trends continue, additive manufacturing is set to become a critical component of modern industrial production.
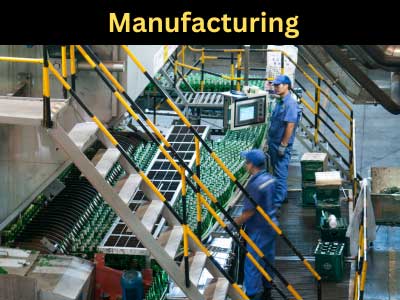
How Additive Manufacturing is Shaping Aerospace and Healthcare
Few industries have been as impacted by additive manufacturing as aerospace and healthcare. In aerospace, the demand for lightweight yet durable components has driven the adoption of 3D printing for creating complex structures that reduce weight without compromising strength. Companies like Boeing and Airbus use additive manufacturing to produce aircraft parts such as fuel nozzles and turbine blades, significantly cutting down on material waste and production costs.
In the healthcare sector, additive manufacturing is revolutionizing the production of medical devices, prosthetics, and implants. Surgeons can now use 3D printing to create patient-specific models for surgical planning, ensuring higher accuracy and better outcomes. For example, customized implants can be printed to fit a patient’s anatomy exactly, improving comfort and reducing recovery times.
The ability to create personalized medical solutions at a lower cost and in less time is one of the main reasons additive manufacturing is considered the future in both industries. As technology advances, we can expect further integration into bioprinting—the creation of living tissues and organs.
The Economic Benefits of Additive Manufacturing
One of the most compelling reasons that additive manufacturing is considered the future of production is the economic benefits it offers. Unlike traditional manufacturing, which often requires expensive tooling and setup costs, additive manufacturing requires minimal upfront investment, especially for custom or low-volume production.
For industries that rely on small-batch production or customized parts, such as automotive or luxury goods, additive manufacturing allows companies to produce items on demand, saving money on storage, inventory management, and excess production. This also makes it easier to adapt to changing market demands without being tied to fixed production methods.
Moreover, by minimizing material waste and shortening the design-to-production cycle, additive manufacturing reduces the overall cost of production. In fields like aviation, where raw materials such as titanium are expensive, the ability to use only the necessary material leads to substantial cost savings.
Additive manufacturing is also helping to reshape global supply chains. As production becomes more localized through distributed manufacturing, companies can reduce transportation costs and import duties, creating more sustainable and efficient systems.
Technological Advancements Pushing Additive Manufacturing Forward
The future of additive manufacturing is closely tied to ongoing technological advancements. Innovations in materials, hardware, and software are constantly pushing the boundaries of what is possible with 3D printing.
One major development is in the area of multi-material printing, where different materials can be printed simultaneously in a single object. This allows for parts that combine flexibility, rigidity, and conductivity—a game-changer for industries like electronics and wearable technology. Additionally, high-performance polymers and advanced metal alloys are opening up new opportunities for printing parts that can withstand extreme conditions, further expanding the range of applications.
On the hardware side, faster printing speeds and larger build volumes are making it more feasible to use additive manufacturing for mass production. Companies are also investing in AI-driven design tools that help optimize parts for additive manufacturing, ensuring that printed components are strong, lightweight, and cost-effective.
As these technologies mature, they will continue to enhance the capability of additive manufacturing to produce complex, high-performance parts, further solidifying its place in the future of manufacturing.
Challenges and Opportunities for the Future of Additive Manufacturing
While the potential of additive manufacturing is immense, several challenges remain. One of the most significant barriers is scalability. Although additive manufacturing is excellent for prototyping and small-batch production, scaling it for mass production remains a challenge due to print speeds and build size limitations. However, ongoing research into faster, more efficient printing technologies aims to address this.
Another challenge is standardization. Unlike traditional manufacturing, where there are established standards for processes and materials, additive manufacturing is still in its early stages, and universal standards are lacking. This can create issues with quality control and regulatory approvals, particularly in industries like healthcare and aerospace.
Despite these challenges, the future is bright for additive manufacturing. As companies continue to invest in research and development, the technology will likely become more cost-effective, scalable, and widely adopted. Additionally, sustainability concerns are driving industries to adopt additive manufacturing due to its ability to minimize waste and enable localized production.
Conclusion
Additive manufacturing is undeniably shaping the future of production. From its ability to create customized and complex parts to its economic and sustainability benefits, this technology offers unmatched flexibility and innovation. As industries like aerospace and healthcare continue to integrate 3D printing into their production processes, we will see even more groundbreaking advancements. However, challenges around scalability and standardization remain, but the opportunities far outweigh these obstacles.
For new engineers entering the field, understanding the trends and potential of additive manufacturing is key to staying ahead in the rapidly evolving world of manufacturing. The future will see greater adoption, technological integration, and a shift towards more efficient, sustainable production methods powered by 3D printing.