Key Takeaway
In dusty environments, place photoelectric sensors at a higher distance above the target to reduce direct exposure to dust. Clean the sensors regularly with a soft, dry cloth or compressed air to avoid buildup, which can affect performance.
Consider using air or water cooling systems to prevent overheating and ensure the sensors remain functional. Protective covers should also be inspected and maintained to shield the sensors from dust. Regular maintenance helps ensure long-term performance and accuracy in harsh conditions.
Common Challenges of Using Sensors in Dusty Environments
Photoelectric sensors are widely used in industrial settings, but dusty environments present unique challenges. Dust particles in the air can easily obstruct the sensor’s beam, leading to false readings, delayed responses, or even complete sensor failure. Dust buildup on the sensor lens or reflector can significantly reduce its ability to detect objects accurately. In high-dust environments like cement plants, wood mills, or mining operations, this issue is even more pronounced, with sensors often requiring frequent maintenance.
Moreover, dust can accumulate over time, slowly degrading sensor performance without immediate notice. This makes it difficult to diagnose the problem until the sensor fails entirely or starts providing inaccurate readings.
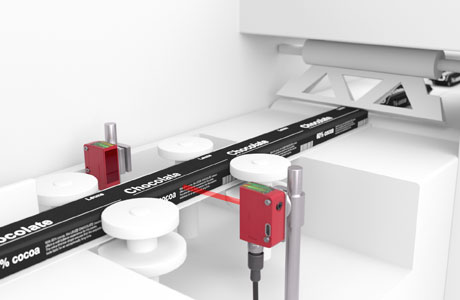
How Dust Affects the Performance of Photoelectric Sensors
Dust has a direct impact on the functionality of photoelectric sensors. As dust particles settle on the sensor lens or reflector, they block or scatter the sensor’s light beam, which leads to poor detection performance. In diffuse sensors, where the object reflects the sensor’s light back to the detector, even a thin layer of dust can cause the sensor to misread the distance, leading to false triggers or missed objects.
Through-beam sensors are also affected, although they tend to perform better in dusty conditions since their emitter and receiver are separated. However, if dust accumulates on either the emitter or the receiver, the sensor’s beam can weaken or become misaligned. This issue is especially prevalent in environments where fine dust particles linger in the air for extended periods.
Additionally, dust may interfere with the sensor’s electronics if it finds its way into unsealed components. This can cause short circuits or electrical malfunctions, further degrading performance. Over time, this exposure can lead to sensor failure, requiring costly replacements. Understanding how dust affects these sensors can help you implement protective measures to mitigate these issues, ensuring reliable performance.
Best Practices for Protecting Sensors from Dust and Contamination
To prevent dust from compromising the performance of photoelectric sensors, certain protective measures are essential. First, consider installing protective covers or enclosures around the sensor to shield it from direct exposure to dust. These enclosures are typically transparent, allowing the sensor to perform its duties while protecting it from external contamination. For environments with high dust levels, air purging systems can also be installed, which use a continuous flow of clean air to blow away dust from the sensor lens.
Regular lens cleaning is another important best practice. Depending on the environment, this may need to be done daily, weekly, or monthly. Using non-abrasive materials and lens cleaning solutions is critical to prevent scratching the sensor lens, which can impair its function. In cases where sensor downtime is unacceptable, self-cleaning lenses or systems that use air jets to keep the lens free of dust may be an ideal solution.
In addition, it’s important to mount sensors away from high-dust areas whenever possible. Elevating the sensor or placing it in a location with lower dust exposure can significantly reduce the need for constant cleaning and maintenance. By following these best practices, you can protect your photoelectric sensors and prolong their lifespan, even in the dustiest environments.
Maintenance Tips to Keep Sensors Functioning in Harsh Conditions
Regular maintenance is critical to keeping photoelectric sensors functioning optimally in harsh, dusty environments. One of the most effective maintenance tips is frequent inspections. Even if a sensor appears to be working fine, periodic checks for dust accumulation on the lens, wiring, and other components can prevent future malfunctions. Visual inspections can help spot dust buildup early, and addressing it quickly can stop the problem before it worsens.
In addition to inspections, scheduled cleaning is essential. Use soft brushes, compressed air, or non-abrasive cloths to gently clean the sensor’s lens and housing. For more challenging environments, implementing automated cleaning systems, such as air knives or wipers, can continuously clear dust without human intervention.
Another crucial tip is calibration checks. Dust can sometimes affect the sensor’s calibration settings, causing it to drift from its optimal range. Recalibrating sensors at regular intervals ensures that they remain sensitive enough to detect objects without false alarms.
Lastly, consider upgrading to dust-resistant models if the environment is particularly harsh. Some modern sensors are built with specialized coatings and materials that make them more resistant to dust and grime. These models often have built-in protection features that reduce the need for frequent maintenance.
Advanced Solutions for Using Sensors in Dusty Industrial Settings
In environments where dust is a constant challenge, advanced solutions are available to ensure that photoelectric sensors function effectively. One such solution is the use of polarized retro-reflective sensors. These sensors are designed to ignore reflective surfaces and dust, making them ideal for environments with high levels of airborne particles. The polarization ensures that the sensor only reacts to the intended target, reducing false triggers caused by dust.
Another advanced option is laser-based photoelectric sensors, which provide a much more focused beam than traditional LED-based sensors. This concentrated beam can cut through dust more effectively, improving the accuracy of detection. Laser sensors are ideal for industries such as mining or cement manufacturing, where dust levels are particularly high.
For extreme conditions, consider sensors with integrated air-blast systems. These systems automatically blow compressed air across the sensor’s lens to keep it clean during operation. This eliminates the need for manual cleaning and reduces downtime, making them an excellent choice for applications where sensor reliability is critical.
Smart sensors, equipped with diagnostic capabilities, can also detect when their performance is being affected by dust. These sensors can send alerts when maintenance is required, enabling proactive care before sensor failure occurs. By integrating these advanced technologies, industries can maintain sensor accuracy and reliability, even in the most demanding environments.
Conclusion
Maintaining photoelectric sensors in dusty environments requires a combination of regular maintenance, protective measures, and advanced solutions. From installing protective covers to using specialized sensor models designed for harsh conditions, there are numerous ways to ensure that these sensors perform optimally. By adhering to best practices for cleaning and calibration, and leveraging advanced technologies like polarized or laser-based sensors, industries can keep their operations running smoothly, even in the dustiest settings. Long-term sensor performance is not just about installation—it’s about ongoing care and attention.