Key Takeaway
Photoelectric sensors enhance safety in manufacturing plants by accurately detecting objects and people in hazardous areas. They create safety barriers around machinery, automatically shutting down equipment when someone crosses the barrier, preventing accidents.
These sensors also monitor production lines, ensuring objects are correctly positioned to prevent malfunctions that could lead to safety risks. Their long-range detection makes them ideal for large manufacturing plants, improving both operational efficiency and safety by providing reliable and precise detection.
The Role of Photoelectric Sensors in Machine Guarding Systems
Photoelectric sensors play a crucial role in machine guarding systems, a fundamental component in modern manufacturing plants. These sensors detect objects or personnel within hazardous areas and immediately trigger machine stops or alarms. The beauty of photoelectric sensors lies in their non-contact nature, meaning they can monitor dangerous zones without causing any obstruction to the machinery’s operation.
In industries with fast-moving machines, this is particularly vital to ensure smooth yet safe operations. Their ability to integrate with safety relays and controllers allows manufacturers to implement a layered approach to safety.
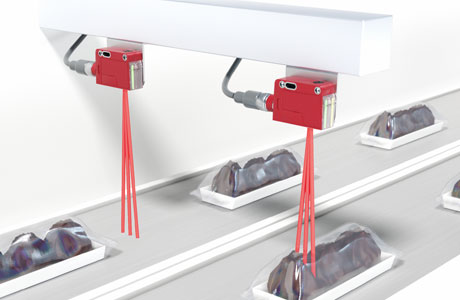
How Sensors Prevent Accidents in High-Risk Areas
In high-risk areas of manufacturing plants, accidents can occur within seconds. Photoelectric sensors provide a line of defense by acting as invisible shields around these zones. Positioned strategically around dangerous machines or areas where human intervention is frequent, these sensors detect any intrusion and immediately halt the machinery, preventing potential injuries or worse.
The simplicity of installation makes photoelectric sensors an easy and effective addition to safety systems. For example, around hazardous machines like industrial presses or cutting equipment, they can be deployed to monitor entrances, ensuring no one enters without triggering an alarm or stopping the machinery. This real-time protection is vital in environments where both speed and safety are critical.
Moreover, photoelectric sensors come in different configurations like through-beam, retro-reflective, and diffuse, allowing flexibility in how they are used. Each type serves a specific purpose depending on the area they monitor. Through-beam sensors, for instance, are ideal for large, open spaces where long-range detection is required. Retro-reflective sensors work well in compact spaces, and diffuse sensors excel in detecting objects within short distances. By deploying the right sensor for each high-risk area, manufacturers can minimize accidents while ensuring seamless operations.
Real-Time Hazard Detection with Photoelectric Sensors
Real-time hazard detection is a game-changer in manufacturing safety, and photoelectric sensors are at the heart of this advancement. These sensors continuously monitor their environment and can instantly identify the presence of any unexpected objects or personnel within their detection range. When an object breaks the beam, it sends a signal to halt operations, offering immediate protection.
One of the main benefits of real-time hazard detection is the speed at which photoelectric sensors respond. The instant a barrier is crossed, the machinery stops, preventing any accidents. This not only ensures the safety of workers but also minimizes damage to machinery or workpieces, preventing costly repairs and downtime. Additionally, the compact size of photoelectric sensors allows them to be installed in tight spaces, offering coverage in areas that would otherwise be difficult to monitor.
Their versatility extends to their ability to work in harsh environments, where factors like dust, humidity, or heat might otherwise compromise other safety systems. Photoelectric sensors maintain high performance in these conditions, ensuring that hazard detection remains reliable. By utilizing these sensors, manufacturing plants can create a safer working environment while keeping operations running smoothly and efficiently.
Integrating Safety Light Curtains for Enhanced Worker Protection
Photoelectric sensors are often integrated with safety light curtains to enhance worker protection in manufacturing environments. Safety light curtains use multiple beams of light to create an invisible protective barrier around machinery. If any of these beams are interrupted, the machine shuts down immediately. This feature is particularly useful in high-risk areas where heavy machinery is operated, such as assembly lines or packaging stations.
The combination of photoelectric sensors and light curtains provides comprehensive protection. While photoelectric sensors monitor specific areas or access points, light curtains offer broader coverage, making it nearly impossible for an operator to accidentally enter a hazardous zone without being detected. This layered approach to safety is critical in environments where workers need to interact closely with machines but must avoid direct contact with hazardous components.
Moreover, safety light curtains can be customized for different levels of sensitivity, ensuring that even small objects or tools are detected if they enter the danger zone. This level of protection helps to reduce workplace injuries while maintaining high productivity. By integrating these technologies, manufacturers can create a safer, more efficient workspace, where worker protection is a top priority.
How Photoelectric Sensors Ensure Compliance with Safety Standards
In today’s manufacturing world, compliance with safety standards is non-negotiable, and photoelectric sensors are a critical component in meeting these requirements. Regulatory bodies such as OSHA and ISO set stringent guidelines to ensure workplace safety, and photoelectric sensors help plants adhere to these standards by providing reliable, automated protection.
The integration of these sensors into safety protocols ensures that manufacturers meet both local and international safety requirements. These sensors offer real-time monitoring and control, which not only reduces the likelihood of accidents but also demonstrates a proactive approach to safety management. This is particularly important during inspections, where any lapses in safety can result in fines or operational delays.
Photoelectric sensors also offer a cost-effective solution for maintaining compliance. Rather than relying on manual supervision or physical barriers, which can be cumbersome and expensive, sensors provide continuous, automatic oversight. Additionally, modern photoelectric sensors are designed to integrate seamlessly with other safety equipment, making it easier for manufacturers to create comprehensive safety systems that meet all required standards. By ensuring compliance, manufacturers can operate with confidence, knowing that they are providing a safe environment for their employees and avoiding costly penalties.
Conclusion
Photoelectric sensors are indispensable in enhancing safety in manufacturing plants. By detecting hazards in real time, preventing accidents, and ensuring compliance with safety standards, they form a vital part of any comprehensive safety system. Their integration with other technologies, like safety light curtains, only adds to their effectiveness, providing layers of protection in high-risk environments. For manufacturers, the investment in photoelectric sensors translates into fewer workplace injuries, increased productivity, and peace of mind, knowing that their operations are both safe and efficient.