Key Takeaway
Photoelectric sensors are generally accurate, but several factors can influence their performance. For example, dark or transparent objects can be harder to detect, and environmental factors like dust or light interference can affect accuracy. Proper sensor alignment and calibration are crucial for maintaining precision.
In industrial settings, these sensors can offer high accuracy for detecting objects and measuring distances. However, regular maintenance and adjusting the sensor configuration are essential to ensure consistent performance across various applications.
Factors that Affect the Accuracy of Photoelectric Sensors
Several factors influence the accuracy of photoelectric sensors. The most significant is the environment in which they operate. Dust, dirt, and moisture can obstruct the light beam, leading to inaccurate readings. Even the material of the target can affect detection, as different surfaces reflect light differently.
Another factor is the distance between the sensor and the object. The greater the distance, the more likely it is that external light or environmental factors can interfere with the beam. Additionally, vibrations or mechanical disturbances in the sensor’s mounting can lead to deviations in accuracy. Sensor placement and alignment play a vital role too. Even a slight misalignment of the sensor can skew results. These factors must be carefully considered to ensure reliable performance in industrial settings.
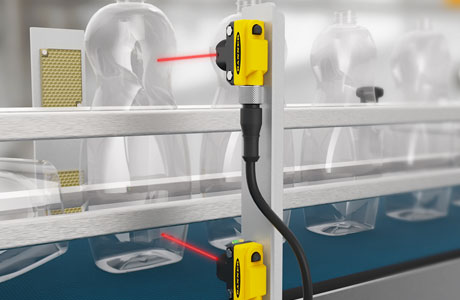
Measuring and Calibrating Sensor Accuracy in Industrial Settings
When it comes to photoelectric sensors, accurate measurements are the backbone of their functionality, especially in industrial settings. Calibration is not just a technical routine; it’s a safeguard against errors that could disrupt entire operations. The process typically involves comparing the sensor’s output against a known standard and making necessary adjustments to fine-tune its sensitivity and detection capabilities. This ensures that the sensor remains precise over time, regardless of the fluctuating environmental conditions it faces.
Moreover, industries such as automotive and electronics heavily rely on regular calibration to maintain the accuracy of their sensors. Minor deviations can lead to costly errors in these environments. Calibration isn’t something you do once and forget about; it requires continuous monitoring. Factors like temperature shifts, dust buildup, or component wear can gradually affect sensor performance. That’s why sensor accuracy measurement is an ongoing process, keeping the sensors reliable and efficient in industrial operations.
Comparing Accuracy of Photoelectric Sensors to Other Sensor Types
Photoelectric sensors stand out for their superior range and flexibility, especially when compared to other sensor types like inductive or capacitive sensors. While inductive sensors are limited to detecting metallic objects, photoelectric sensors can detect a wide variety of materials, making them ideal for diverse industrial applications. They also offer longer sensing distances, a critical feature for industries with complex, large-scale operations.
However, they are not without limitations. Capacitive sensors, for example, excel in detecting very small material changes at close ranges, offering extreme precision in tasks where tiny variations make a big difference. Knowing the strengths and weaknesses of each sensor type is essential for engineers to make the best choices. Sometimes, the decision between a photoelectric and another sensor type could mean fewer recalibrations and smoother automation in a manufacturing process.
Best Practices to Improve Photoelectric Sensor Accuracy
To get the most out of photoelectric sensors, proper installation and maintenance are key. The first step is aligning the sensor accurately with the target object, reducing the chances of false readings or missed detections. Many industries use alignment tools to ensure that sensors are correctly positioned for optimal performance. This simple step can make a significant difference in the sensor’s accuracy.
Maintaining a clean environment also plays a big role in sensor performance. Dust or grime buildup on sensors can distort readings, so regular cleaning is essential. Additionally, minimizing exposure to ambient lighting or direct sunlight prevents interference. Software tools can also be integrated, utilizing filtering algorithms to compensate for minor disturbances. Following these best practices keeps the sensors running smoothly and reduces the chances of error in demanding environments.
Accuracy Considerations in Different Industrial Applications
Accuracy needs can vary significantly depending on the industrial application. For example, in high-speed packaging lines, photoelectric sensors must swiftly detect various materials and sizes on a conveyor belt. A minor delay or inaccuracy in these cases could lead to production halts or defective products, emphasizing the need for real-time precision.
In automotive manufacturing, accuracy is even more critical. Sensors must detect minute details to ensure the correct assembly of parts. In safety applications, like safety light curtains, any inaccuracy can lead to severe risks. Therefore, engineers must carefully assess the sensor’s accuracy requirements based on the specific demands of the industry. Balancing the need for precision with cost-effectiveness is a key consideration in choosing the right sensors.
Conclusion
Accuracy in photoelectric sensors isn’t just a technical requirement—it’s essential for efficiency, safety, and reliability in industrial applications. Whether you’re an engineer managing a production line or a technician ensuring machinery operates without a hitch, understanding sensor accuracy can significantly impact your outcomes. By recognizing the factors that affect accuracy, knowing how to measure and calibrate it, and following best practices, you can ensure that these sensors perform at their best. In the end, accurate sensors lead to fewer errors, safer environments, and smoother industrial processes.