Key Takeaway
We use SCADA (Supervisory Control and Data Acquisition) to monitor and control industrial processes efficiently and in real time. SCADA collects data from sensors, PLCs, and other devices, then processes and displays it on user-friendly interfaces. This allows operators to track performance, detect issues, and respond quickly to maintain smooth operations.
SCADA is essential for improving efficiency, reliability, and safety in industries like manufacturing, energy, and water management. It enables remote control of equipment, stores historical data for analysis, and helps optimize processes. By simplifying the management of complex systems, SCADA reduces downtime, improves productivity, and ensures better decision-making. It’s a vital tool for modern automation and process control.
The Need for Real-Time Monitoring and Control
In industrial operations, real-time monitoring and control are crucial for ensuring seamless performance and quick responses to changing conditions. SCADA systems excel at providing this capability.
SCADA collects data from sensors, actuators, and other field devices, offering operators a live view of system performance. For example, in a power plant, SCADA displays key parameters like voltage, current, and frequency, enabling operators to ensure the system operates within safe limits.
Moreover, SCADA allows operators to control processes remotely. If a fault occurs, such as a pressure drop in a pipeline, operators can make adjustments immediately, preventing further damage. This level of responsiveness minimizes downtime and enhances overall system reliability.
The ability to monitor and control processes in real-time makes SCADA a vital tool for maintaining efficiency and stability in complex industrial environments.
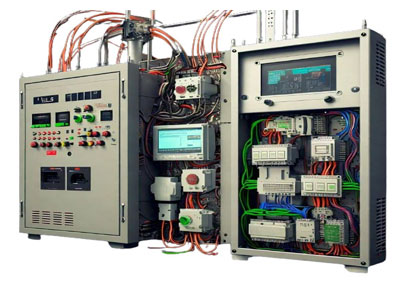
Improving Operational Efficiency with SCADA
Efficiency is a top priority for industries, and SCADA systems play a significant role in achieving it.
By automating routine tasks, SCADA reduces the need for manual intervention, allowing operators to focus on higher-level responsibilities. For instance, SCADA can regulate the speed of conveyor belts in a manufacturing plant based on product demand, ensuring optimal throughput while minimizing energy consumption.
SCADA also identifies inefficiencies by analyzing system performance. For example, in a water distribution network, SCADA might detect areas with excessive leakage. Operators can then address these issues to conserve resources and reduce costs.
With its ability to optimize processes and resources, SCADA ensures that industries operate at peak efficiency, boosting productivity and profitability.
You May Like to Read
Enhancing Safety and Fault Detection Through Automation
Safety is a primary concern in industrial operations, and SCADA systems are designed with robust safety features to address this need.
SCADA continuously monitors critical parameters like temperature, pressure, and flow rates. If any of these parameters deviate from predefined safe ranges, SCADA triggers alarms to alert operators. For example, in an oil refinery, if a reactor’s temperature exceeds the safe limit, SCADA can automatically shut down the equipment to prevent accidents.
Fault detection is another essential feature. SCADA can identify issues such as equipment malfunctions or pipeline leaks in real-time. This proactive approach ensures that problems are addressed before they escalate, reducing the risk of costly downtime or safety incidents.
By enhancing safety and fault detection, SCADA protects both personnel and assets, ensuring the smooth operation of industrial processes.
SCADA’s Role in Reducing Downtime and Maintenance Costs
Downtime and maintenance are significant challenges for industries, often leading to financial losses and production delays. SCADA systems help mitigate these issues by enabling predictive maintenance and efficient resource management.
SCADA continuously monitors equipment health, collecting data on factors like vibration, temperature, and operating hours. By analyzing this data, operators can identify signs of wear or inefficiency, scheduling maintenance before a failure occurs. For instance, in a manufacturing plant, SCADA might detect increased vibration in a motor, prompting a replacement before the motor fails.
Additionally, SCADA minimizes unplanned downtime by providing real-time alerts for faults and enabling quick responses. In power grids, for example, SCADA helps operators reroute electricity around faulted lines, ensuring uninterrupted service.
By reducing downtime and optimizing maintenance schedules, SCADA significantly lowers operational costs and enhances productivity.
Supporting Data-Driven Decision-Making in Industrial Processes
One of SCADA’s most powerful features is its ability to support data-driven decision-making through advanced data collection and analysis.
SCADA systems store historical data, allowing industries to identify trends and improve operations. For example, in a water treatment facility, SCADA can analyze historical flow data to optimize pump schedules and reduce energy consumption during off-peak hours.
SCADA also generates detailed reports, summarizing performance metrics, alarm histories, and system availability. These reports are invaluable for strategic planning, helping industries forecast demand, allocate resources, and comply with regulatory requirements.
By transforming raw data into actionable insights, SCADA empowers industries to make informed decisions that drive continuous improvement and long-term success.
Conclusion
SCADA systems are indispensable in modern industries due to their ability to provide real-time monitoring, improve efficiency, enhance safety, reduce downtime, and support data-driven decision-making. By integrating automation, fault detection, and performance analysis, SCADA ensures the smooth and reliable operation of complex industrial processes.
Whether managing power grids, refining oil, or optimizing manufacturing lines, SCADA enables industries to meet challenges with confidence and precision. For engineers and operators, leveraging SCADA’s capabilities is key to achieving operational excellence and staying competitive in today’s dynamic industrial landscape.