Key Takeaway
HMI panels are used in industrial systems to provide an intuitive interface for operators to monitor and control machinery. They display real-time data such as machine status, alarms, and performance metrics, making it easier for operators to understand and respond to system changes.
By using HMI panels, industrial systems can operate more efficiently and safely. Operators can quickly identify issues, adjust settings, and optimize performance, reducing downtime and errors. HMI panels also improve safety by allowing operators to control systems remotely, minimizing the need for direct interaction with dangerous equipment. These benefits make HMI panels essential in industries like manufacturing, automation, and energy.
The Role of HMI Panels in Simplifying Complex Processes
In industrial automation, managing complex processes is a critical task. Manufacturing plants, for instance, often involve numerous machines working together, each with its own set of parameters. Without a clear and simple way to manage these systems, operators would have to deal with many complex variables that could lead to confusion, delays, or errors. This is where HMI panels play a significant role.
Centralized Control:
HMI panels act as the central control point for all the machines and equipment in an industrial setup. Operators no longer need to walk around to inspect or adjust different machines. Instead, they can access all the information and control options from a single HMI screen. For example, an operator can monitor the status of a motor, adjust the speed of a conveyor belt, and set temperature controls—all from one interface. This centralized approach simplifies the process of controlling and monitoring industrial operations.
Data Visualization:
HMI panels make complex data easy to understand by displaying it visually. Instead of relying on spreadsheets or numerical data, operators can see real-time data through graphical displays. These could include charts, trend lines, and gauges, making it easier to interpret the data quickly. Whether it’s tracking pressure, speed, or temperature, HMI panels convert complex machine data into understandable and actionable insights. This greatly enhances the efficiency of operations.
Enhanced User Experience:
The user interfaces on modern HMI panels are designed to be intuitive. Buttons, sliders, and touchscreens are easily navigable, even for individuals without extensive technical training. This ease of use simplifies complex processes, allowing operators to focus more on managing the system rather than figuring out how to interact with it. Additionally, HMI screens are customizable, meaning the interface can be tailored to meet specific operational needs.
By simplifying complex processes, HMI panels make industrial operations more streamlined and user-friendly, ensuring that operators can stay focused on critical tasks and improving overall productivity.
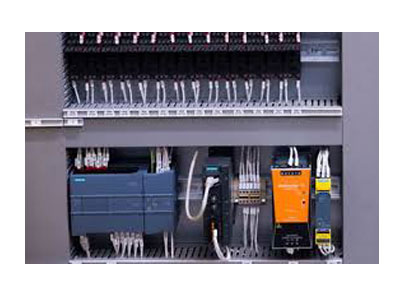
How HMI Panels Improve Operator Efficiency and Decision-Making
One of the most significant advantages of using HMI panels in industrial systems is their ability to improve operator efficiency and decision-making. In industrial settings, every second counts. Operators need to make quick decisions based on real-time data to keep systems running smoothly and avoid costly downtime. HMI panels help to facilitate this by providing an intuitive and efficient interface that empowers operators to make better decisions.
Real-Time Data Access:
HMI panels provide real-time access to crucial system data. For example, operators can monitor pressure, temperature, and machine status, all at a glance. This instant access to information allows operators to respond quickly to any fluctuations or abnormalities, minimizing the risk of system failure or damage. By providing clear, accurate, and up-to-date data, HMI panels allow operators to make informed decisions without delay.
Error Prevention and Quick Corrections:
In addition to improving decision-making, HMI panels help prevent errors. The visual nature of HMI interfaces makes it easy for operators to spot problems early. Whether it’s an alert showing that a temperature reading is too high or a graphical representation indicating a machine malfunction, HMI panels help operators identify issues before they escalate. Moreover, operators can take immediate corrective actions, such as adjusting settings or initiating shutdowns, through the same interface.
Process Automation and Optimization:
HMI panels help optimize processes by enabling operators to control several machine parameters simultaneously. Rather than adjusting each machine individually, operators can use HMI interfaces to fine-tune multiple systems in one place. For example, adjusting the speed of a conveyor belt, the temperature of an oven, and the pressure of a pump can be done from the same screen, helping to streamline workflows and reduce manual labor.
By improving efficiency and decision-making, HMI panels make industrial processes faster, more reliable, and less prone to human error, resulting in a more productive work environment.
You May Like to Read
Integrating HMI Panels with PLCs for Seamless Automation
Programmable Logic Controllers (PLCs) are the backbone of most industrial automation systems. They control machines and processes by receiving inputs from sensors and sending commands to actuators. However, PLCs alone cannot provide the intuitive interface that operators need to interact with the system. This is where HMI panels come in. They act as the bridge between the operator and the PLC, enabling seamless communication and control.
Bidirectional Communication:
HMI panels integrate with PLCs to provide a bidirectional flow of information. The PLC collects data from sensors and sends it to the HMI, where it is displayed in an understandable format. Conversely, the operator can send commands to the PLC through the HMI to adjust settings, start or stop processes, or change machine parameters. This seamless communication between the HMI and PLC ensures that the system operates smoothly and efficiently.
Real-Time Feedback and Control:
When HMI panels are integrated with PLCs, operators can receive real-time feedback on the performance of the entire system. If a PLC detects a fault in the system or a machine’s performance is outside the expected range, the HMI will immediately display the issue, allowing the operator to respond quickly. Additionally, operators can make real-time adjustments directly from the HMI, such as modifying machine speeds or resetting system parameters.
Enhanced System Automation:
HMI panels allow for greater automation in industrial processes by providing operators with the ability to control multiple processes at once. For instance, an operator can use an HMI to control not just one machine, but an entire line of interconnected machines managed by PLCs. This integrated system reduces the need for manual adjustments, freeing up operators to focus on higher-level decision-making.
By integrating HMI panels with PLCs, industrial systems can operate more efficiently, with less need for manual intervention and a greater level of control and automation.
Enhancing System Monitoring and Control Through HMI Interface
Monitoring and control are two of the most critical aspects of managing industrial systems. HMI panels significantly enhance both by providing operators with an intuitive interface to manage complex systems. They give operators the ability to keep track of every part of the system in real time, making it easier to detect problems, adjust settings, and ensure everything runs smoothly.
Centralized Monitoring:
HMI panels allow operators to monitor all key system parameters from a single interface. Whether it’s monitoring temperature, pressure, flow rates, or machine speed, the HMI provides an overview of all critical metrics in real time. Operators can access detailed data on each component and track the health of the entire system. This centralized approach to monitoring helps operators stay in control and catch potential issues before they escalate.
Detailed Control Options:
HMI panels not only display data but also allow for detailed control over the system. Operators can adjust settings such as motor speed, machine temperature, or production rates. With the ability to control multiple processes from a single panel, operators can streamline their workflow and make quicker, more informed decisions.
Customizable Dashboards:
Another key feature of HMI panels is the ability to create customizable dashboards. Operators can choose the data and controls they want to see, based on their roles and responsibilities. For example, a machine operator might want to see only the status of a specific machine, while a system administrator may prefer a broader view of the entire production line. These customizable dashboards make it easier for operators to focus on the most important aspects of the system, improving efficiency and reducing distractions.
By enhancing system monitoring and control, HMI panels help ensure smooth, reliable operations, allowing operators to make adjustments and stay in control of their systems at all times.
The Safety and Error Prevention Benefits of HMI Panels in Industry
Safety is a top priority in any industrial setting, and HMI panels play a crucial role in ensuring that safety standards are met. Through real-time monitoring, alerts, and diagnostics, HMI panels help operators prevent errors, avoid accidents, and maintain safe operating conditions.
Real-Time Alerts and Alarms:
HMI panels are equipped with sophisticated alert systems that notify operators of potential issues. Whether it’s an overheating motor, a high-pressure reading, or a malfunction in a machine, the HMI will display an alarm or send a notification. This allows operators to take immediate corrective action and prevent the problem from escalating into a more serious issue.
Preventive Maintenance:
HMI panels help improve safety by facilitating preventive maintenance. By continuously monitoring system performance and providing detailed diagnostic data, HMIs can alert operators when components are showing signs of wear or malfunction. This early warning system helps prevent equipment failures, reducing the likelihood of accidents and downtime.
Emergency Shutdown Features:
In extreme cases, if a system is in danger of causing an accident or further damage, the HMI can trigger an emergency shutdown. Operators can immediately press a button or follow a pre-programmed procedure to halt the system and prevent further harm. This feature is critical for ensuring the safety of both workers and equipment.
By preventing errors, providing real-time safety alerts, and facilitating maintenance, HMI panels play a critical role in ensuring the safety and reliability of industrial systems.
Conclusion
HMI panels are indispensable in industrial systems, offering a wide range of benefits that improve system control, enhance operator efficiency, and contribute to safety and error prevention. Through intuitive interfaces, real-time data access, and seamless integration with PLCs, HMI panels help simplify complex processes and ensure smooth operations. As industrial systems continue to evolve, the role of HMI panels will only become more critical, making them an essential tool for engineers and operators alike.