Key Takeaway
An ACB (Air Circuit Breaker) is designed for high-current and high-voltage systems. It works by using air to extinguish the electrical arc when a fault occurs. ACBs are often used in industrial settings where large amounts of current need to be controlled and are typically more robust in handling heavy electrical loads.
On the other hand, an MCCB (Molded Case Circuit Breaker) is more suitable for medium-range applications, offering adjustable trip settings. MCCBs are often used in residential or commercial settings to protect electrical circuits from overload and short circuits.
While both offer excellent protection, ACBs are generally better for high-voltage and industrial use, whereas MCCBs are more versatile for smaller, medium-voltage applications. The choice depends on your specific requirements—ACB for heavy-duty and MCCB for general protection.
Understanding the Basics of ACB (Air Circuit Breaker) and MCCB (Molded Case Circuit Breaker)
In the electrical world, protection against short circuits and overloads is a critical aspect of maintaining system integrity. Two popular types of circuit breakers used in various electrical applications are Air Circuit Breakers (ACB) and Molded Case Circuit Breakers (MCCB). These breakers serve the same purpose—to protect the electrical circuits from damage due to overcurrent or fault conditions—but they do so in different ways.
An ACB is typically used in high-current applications and is designed to handle significant power interruptions. ACBs are mostly used in low-voltage systems and have a mechanism that utilizes air to extinguish the arc when the circuit is interrupted. These devices are ideal for large industrial setups where heavy-duty protection is needed.
On the other hand, an MCCB is used in both residential and industrial settings, providing a more flexible solution for moderate to high current ranges. It is known for being more compact and is typically found in low to medium-voltage systems. Unlike ACBs, MCCBs offer adjustable trip settings, providing more precise protection, and they can be used in smaller enclosures.
While both breakers protect electrical systems, understanding the underlying differences between these two options will help engineers make an informed decision based on the specific needs of their electrical setup.
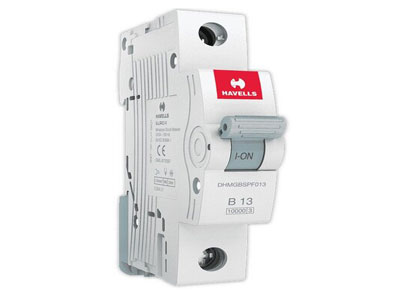
Key Features and Functions of ACB vs. MCCB in Electrical Protection
When it comes to electrical protection, the ACB and MCCB offer unique features tailored to different needs and applications. Understanding these features is essential for selecting the right breaker.
ACB Features:
ACBs are typically designed for higher fault current ratings. They are capable of interrupting large amounts of electrical energy, making them suitable for high-power applications. One notable feature of ACBs is their use of air as an arc-quenching medium. Air provides a reliable method to extinguish the arc created when the circuit is broken. ACBs can handle short-circuit protection, overloads, and in some cases, under-voltage protection. They are also equipped with adjustable trip settings for precise control of fault interruption.
MCCB Features:
MCCBs, on the other hand, are generally used for lower and medium voltage systems. They are characterized by their molded case, which provides durability and protection from environmental factors. Unlike ACBs, MCCBs are more compact and ideal for installations where space is limited. They come with adjustable settings for overload and short-circuit protection, offering more flexibility in adjusting the protection level based on the load requirements. Additionally, MCCBs have a higher degree of precision when it comes to overload settings and trip characteristics, making them versatile for different applications.
The major distinction between the two is the size, functionality, and range of voltage they can handle. ACBs are generally more robust and designed for heavy-duty industrial settings, while MCCBs provide an excellent option for residential and commercial use, especially where precise protection is needed.
You May Like to Read
Performance Comparison: ACB vs. MCCB for Different Load Capacities
When comparing ACBs and MCCBs, one of the most critical factors to consider is their performance across different load capacities. The type of circuit breaker used can greatly influence the performance and efficiency of the electrical system, depending on the nature of the load.
ACB Performance:
Air Circuit Breakers are designed to handle very high current ratings, often exceeding those that MCCBs can manage. These breakers are ideal for heavy industrial settings, where the electrical load can be massive and fluctuating. They are excellent in applications where the fault currents can reach extremely high levels, such as large motors or transformers. The high breaking capacity of ACBs ensures that they can interrupt fault currents effectively without compromising system stability. This makes them perfect for large-scale factories or power distribution systems.
MCCB Performance:
In contrast, Molded Case Circuit Breakers are better suited for moderate load capacities. While they can handle relatively high current ratings, their breaking capacity is generally lower than that of ACBs. However, the flexibility offered by MCCBs, especially their adjustable settings for overloads and short circuits, ensures they perform well under varying electrical load conditions. These breakers are perfect for applications in commercial buildings, smaller industrial facilities, or residential properties, where the electrical load is stable and relatively predictable. They offer precise protection tailored to the specific needs of the load, which makes them ideal for environments where load fluctuations are not as significant.
While ACBs are superior for managing high-load applications, MCCBs offer a more versatile, cost-effective solution for a range of medium-load settings.
ACB vs. MCCB for Different Load Capacities H2: How ACB and MCCB Differ in Terms of Cost, Maintenance, and Durability
When selecting between an ACB and an MCCB, it’s important to factor in their cost, maintenance, and durability, as these elements can significantly impact the long-term performance of the electrical system.
ACB Cost:
In general, ACBs are more expensive than MCCBs. The larger size, higher breaking capacity, and use of advanced mechanisms contribute to the higher initial cost of ACBs. However, when considering large industrial applications or systems with very high power demands, the investment in an ACB is justified by its durability and high fault tolerance.
MCCB Cost:
MCCBs are typically more affordable, especially in applications where moderate current ratings are required. The smaller size and more compact design reduce production and installation costs. For most commercial or residential settings, MCCBs provide an effective solution at a more affordable price point.
Maintenance:
In terms of maintenance, MCCBs have a significant advantage over ACBs due to their simple design. MCCBs require less frequent servicing and have fewer components that need attention over time. Additionally, the molded case design protects internal components from external damage, reducing the risk of wear and tear.
On the other hand, ACBs require more regular maintenance, as the arc quenching process involves the use of air, which can lead to contamination or wear on the breaker contacts. They also require a more thorough inspection and servicing due to their complexity.
Durability:
ACBs are more durable and reliable when used in heavy-duty environments. They are built to withstand the higher fault currents typical of large industrial systems. MCCBs, while highly durable, are more suited to moderate-duty applications and have a shorter lifespan in comparison to ACBs under heavy-duty conditions.
How ACB and MCCB Differ in Terms of Cost, Maintenance, and Durability H2: Applications of ACB vs. MCCB in Industrial, Commercial, and Residential Settings
Both ACBs and MCCBs find their place in various sectors, but their application depends on the size, power requirements, and load characteristics of the electrical system.
Industrial Settings:
In large-scale industrial setups, ACBs are typically the preferred choice due to their high breaking capacity and ability to handle large current loads. They are commonly used in applications such as transformer protection, generator circuits, and substations where high fault currents and continuous power supply are critical.
Commercial Settings:
For commercial applications, MCCBs are often used due to their compact size, affordability, and ability to handle moderate electrical loads. These circuit breakers provide excellent protection in areas such as shopping malls, office buildings, and light manufacturing plants, where electrical loads are predictable and require efficient protection from short circuits and overloads.
Residential Settings:
MCCBs are commonly used in residential settings, especially for main circuit protection or distribution boards. Their compact design, adjustable trip settings, and reliable protection make them perfect for homes and smaller apartment complexes.
Overall, the decision between ACBs and MCCBs largely depends on the nature of the electrical load and the environment in which the breaker is being installed. Industrial applications often lean toward ACBs, while MCCBs are better suited for residential and commercial environments.
Conclusion
In conclusion, both ACBs and MCCBs are excellent choices for electrical protection, but the best option depends on the application. ACBs are ideal for high-current industrial environments where the risk of large fault currents is significant. On the other hand, MCCBs offer a more cost-effective solution for residential and commercial applications, providing precise protection for moderate loads.
By carefully considering factors such as current rating, cost, maintenance needs, and application suitability, engineers can ensure they select the right circuit breaker for their specific needs, optimizing both safety and cost-efficiency in electrical systems.