Key Takeaway
Embedded systems are designed for industrial use. These specialized computers are compact and built to handle specific tasks within industrial applications. They are often integrated into machinery, equipment, or vehicles. Their primary function is to control and monitor various processes, ensuring smooth and efficient operations. Embedded systems are known for their reliability and durability in harsh environments. They can operate under extreme temperatures, vibrations, and dust. These systems are essential in industries like manufacturing, automation, and transportation. By using embedded systems, industries can achieve greater precision and efficiency in their operations.
Industrial PCs Overview
Industrial PCs, or IPCs, stand out from conventional computers due to their robustness and specialized features tailored for industrial settings. Unlike commercial PCs, which are designed for office or home use, IPCs are engineered to withstand harsh conditions such as extreme temperatures, humidity, dust, and vibrations commonly found on factory floors and industrial sites.
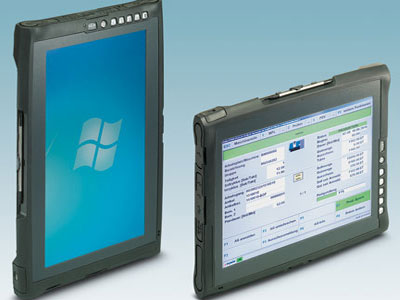
Comparison with Other Computers
When comparing Industrial PCs (IPCs) with standard desktop PCs or laptops, the distinctions are profound and pivotal for anyone entering the industrial computing arena. Consumer-grade computers, such as those found in homes or offices, are engineered primarily for style and multimedia performance. They boast sleek designs, vibrant displays, and robust audiovisual capabilities tailored for everyday tasks and entertainment.
In stark contrast, IPCs prioritize functionality over form, designed specifically to endure harsh industrial environments where reliability and compatibility with specialized equipment are paramount. These rugged machines are the backbone of sectors like manufacturing, automation, and process control, where uninterrupted operation is non-negotiable.
Design and Durability
The hallmark of IPCs lies in their rugged design and specialized components. Unlike their consumer counterparts, IPCs are built to withstand extremes—whether it’s fluctuating temperatures, airborne contaminants, or constant vibration on the factory floor. Their robust exteriors and industrial-grade components ensure longevity and operational stability, minimizing the need for frequent maintenance and downtime.
Enhanced cooling systems are a crucial feature of IPCs, crucial for managing heat dissipation effectively. This ensures that critical components remain within optimal operating temperatures, even under heavy loads or in confined industrial settings where ambient temperatures can fluctuate drastically.
Moreover, IPCs are equipped with specialized interfaces and ports tailored to industrial protocols and equipment. This ensures seamless integration with a wide array of industrial machinery, from PLCs (Programmable Logic Controllers) to SCADA (Supervisory Control and Data Acquisition) systems, facilitating efficient data exchange and control within industrial automation processes.
Key Design Features
Beyond their physical robustness, IPCs differentiate themselves through the reliability and performance of their internal components. Unlike standard PCs that often use commercial-grade components, IPCs are equipped with industrial-grade processors, memory modules, and storage devices optimized for continuous operation in demanding environments.
These industrial-grade components are designed to meet stringent quality standards, ensuring stable performance over extended periods. This reliability translates into minimized downtime and enhanced productivity for industrial operations, where any disruption can lead to significant financial losses and operational setbacks.
The operational reliability of IPCs is further bolstered by their compatibility with specialized software and operating systems commonly used in industrial automation. These systems are tailored to manage complex processes, monitor equipment performance in real-time, and facilitate predictive maintenance—all crucial for optimizing efficiency and ensuring regulatory compliance in industrial settings.
In essence, while standard desktop PCs and laptops cater to general computing needs with a focus on style and multimedia, IPCs stand out for their durability, reliability, and compatibility with industrial equipment and protocols. They are not just machines but essential tools that uphold the operational integrity and efficiency of modern industrial processes worldwide.
Industry-Specific Models
In the dynamic landscape of modern manufacturing, Industrial PCs (IPCs) play a pivotal role in enhancing operational efficiency and precision. These specialized computing devices are meticulously designed to cater to the unique demands of manufacturing environments, where real-time monitoring and control are paramount.
Manufacturing plants deploy IPCs equipped with sophisticated sensors and actuators, enabling seamless integration into complex production lines. These IPCs facilitate continuous data collection and analysis, empowering plant managers to optimize processes, minimize downtime, and ensure consistent product quality.
Real-Time Monitoring and Control Capabilities
IPCs embedded with advanced real-time monitoring capabilities serve as the nerve center of manufacturing operations. They gather data from various sensors across the production floor, providing instant insights into equipment performance and process variables. This real-time visibility allows operators to make informed decisions swiftly, preempting potential issues before they escalate.
Integration into Production Processes
The seamless integration of IPCs into manufacturing processes is facilitated by their compatibility with industrial automation systems. These PCs act as central hubs, orchestrating the synchronized operation of robotic arms, conveyors, and other machinery. By interfacing with Programmable Logic Controllers (PLCs) and Human-Machine Interfaces (HMIs), IPCs ensure harmonious workflow management and enhance overall productivity.
Leading Manufacturers
In the realm of transportation, Industrial PCs (IPCs) serve as robust computing solutions designed to withstand the rigors of vehicle operation. Unlike conventional consumer-grade computers, IPCs deployed in transportation sectors are engineered with rugged casings and enhanced connectivity features, ensuring reliability in challenging environments.
Robust Connectivity Features
Transportation IPCs are equipped with robust connectivity options, including Wi-Fi, Bluetooth, and Ethernet, to facilitate seamless communication within vehicle networks. These IPCs support data exchange between onboard systems, enabling real-time telemetry, GPS tracking, and remote diagnostics. Such connectivity empowers fleet managers to monitor vehicle performance, optimize routes, and ensure passenger safety.
Ruggedized Design for Durability
The durability of IPCs in transportation is bolstered by their ruggedized construction, which protects against vibrations, shocks, and extreme temperatures. Encased in hardened enclosures, these PCs withstand harsh conditions prevalent in automotive, railway, and aerospace applications. Their robust design ensures uninterrupted operation during transit, minimizing the risk of system failures and ensuring continuous data availability.
Conclusion
Choosing the right computer for industrial use is pivotal for optimizing operational efficiency and maintaining productivity in industrial settings. Industrial PCs, with their rugged design, specialized features, and compatibility with industrial equipment, emerge as the preferred choice for industries ranging from manufacturing and logistics to energy and healthcare. By prioritizing durability, reliability, and performance, IPCs play a crucial role in driving innovation and enhancing competitiveness in today’s industrial landscape.