Key Takeaway
The principle of SCADA is to monitor and control industrial processes in real-time. It works by collecting data from remote devices, such as sensors and Remote Terminal Units (RTUs), which are spread across different locations. This data is then sent to a central system.
At the central control station, the Human-Machine Interface (HMI) allows operators to view the data and control the processes. The system continuously monitors conditions, such as temperature or pressure, and alerts operators if something goes wrong. By automating control and providing real-time insights, SCADA helps improve efficiency and safety in industries like manufacturing, energy, and utilities.
The Concept of Real-Time Data Acquisition and Monitoring
At the heart of SCADA lies the principle of real-time data acquisition and monitoring. This fundamental concept ensures that industrial processes are continuously observed and data is collected without delays.
SCADA systems rely on sensors and Remote Terminal Units (RTUs) to capture real-time data from the field. For example, a temperature sensor in a power plant may continuously monitor heat levels and send updates every second to ensure operations stay within safe limits. This real-time data is crucial for identifying trends, detecting anomalies, and making immediate adjustments.
Operators use this data to gain a comprehensive understanding of the system’s performance. They can see live updates on Human-Machine Interfaces (HMIs), which display information in graphs, charts, and alarms. For instance, if a pressure reading crosses a predefined threshold, an alarm is triggered, prompting immediate action.
Real-time monitoring also helps in preventive maintenance. By observing subtle changes in parameters, operators can predict potential failures and address them before they escalate. This reduces downtime and improves overall efficiency.
Without real-time data acquisition, SCADA systems would lose their ability to provide accurate and timely insights. This principle is what enables industries to maintain control over their processes, ensuring smooth and reliable operations.
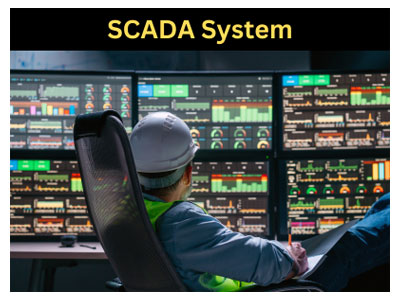
How SCADA Integrates Control Systems for Automation
SCADA’s second core principle is its ability to integrate control systems to achieve automation. It acts as a bridge between raw data and automated actions, ensuring that industrial processes run with minimal human intervention.
Automation begins with Programmable Logic Controllers (PLCs) or RTUs, which execute commands based on the data they receive. For example, if a water level sensor in a tank detects that the water is too low, the SCADA system can automatically activate a pump to refill it. This eliminates the need for manual monitoring and operation.
SCADA systems also enable complex control logic. Through software, operators can program multiple conditions and responses, ensuring that the system adapts to varying scenarios. For instance, in a manufacturing plant, conveyor belts can be set to speed up or slow down depending on the production requirements.
What makes SCADA invaluable is its ability to integrate multiple systems into one cohesive operation. It can synchronize the activities of various machines, ensuring efficiency and reducing the chances of errors.
Automation doesn’t just save time—it enhances safety and productivity. By integrating control systems, SCADA reduces the workload on operators while ensuring that processes adhere to precise standards. This seamless integration is what makes SCADA a cornerstone of modern industrial automation.
The Role of Feedback Loops in SCADA System Operations
Feedback loops are essential to SCADA operations, ensuring that processes are continuously refined and optimized. This principle revolves around the system’s ability to compare actual performance with desired outcomes and take corrective actions.
At its simplest, a feedback loop works like this: A sensor captures data about a specific parameter, such as motor speed. This data is sent to the SCADA system, which compares it to a preset value. If the actual speed deviates from the target, the system sends a command to the motor to adjust its speed accordingly.
There are two types of feedback loops in SCADA: open-loop and closed-loop. Open-loop systems execute commands without checking if the desired result was achieved. In contrast, closed-loop systems monitor outcomes and make adjustments as needed, ensuring greater accuracy and reliability.
Feedback loops are particularly important in dynamic environments where conditions can change rapidly. For example, in an oil refinery, fluctuations in pressure or temperature require immediate corrections to maintain safety and efficiency.
By leveraging feedback loops, SCADA ensures that processes remain consistent and efficient. These loops are the foundation of a system that learns and adapts, making SCADA indispensable in industries where precision is key.
The Principle of Remote Monitoring and Control in SCADA
One of SCADA’s most powerful principles is its ability to enable remote monitoring and control. This capability allows operators to oversee and manage processes from virtually anywhere, enhancing flexibility and efficiency.
Remote monitoring begins with data collection at the field level. Sensors, RTUs, and PLCs gather information and transmit it to centralized servers. From there, the data can be accessed via HMIs, web interfaces, or mobile devices. For example, a factory manager can use a tablet to check production levels and even adjust machine settings while traveling.
Control functions are equally accessible. Operators can issue commands remotely to adjust processes, shut down equipment, or respond to emergencies. This is especially valuable in industries with geographically dispersed assets, such as oil pipelines or wind farms.
The principle of remote access also improves response times. If an issue arises, operators can address it immediately without needing to be on-site. This reduces downtime and minimizes potential losses.
To ensure security, SCADA systems use encryption, firewalls, and multi-factor authentication for remote access. This safeguards sensitive data and prevents unauthorized control of critical infrastructure.
In today’s interconnected world, remote monitoring and control are not just conveniences—they’re necessities. This principle enables industries to operate smarter and more efficiently, no matter where their assets are located.
The Importance of Data Processing and Decision-Making in SCADA
Data processing and decision-making are at the core of SCADA’s functionality. The system’s ability to turn raw data into actionable insights is what sets it apart from traditional control systems.
SCADA systems process massive amounts of data in real-time. This includes everything from temperature readings to equipment performance metrics. Advanced algorithms analyze this data to detect patterns, predict failures, and optimize processes. For instance, if a machine’s performance begins to degrade, the system can recommend maintenance before a breakdown occurs.
Decision-making in SCADA is both automated and manual. Automated decisions are based on pre-programmed logic. For example, if a pressure sensor detects a value outside the safe range, the system might automatically shut down the equipment to prevent damage.
Manual decision-making is supported by SCADA’s data visualization tools. Operators can review dashboards, trend graphs, and reports to make informed choices. These tools simplify complex data, presenting it in a way that’s easy to understand.
Data processing also aids long-term planning. Historical data is stored and analyzed to identify inefficiencies, optimize resource allocation, and improve overall performance.
This principle ensures that SCADA systems don’t just react to situations—they anticipate them. By processing data effectively, SCADA empowers industries to operate proactively, ensuring reliability and efficiency.
Conclusion
The principle of SCADA revolves around real-time data acquisition, automated control, feedback mechanisms, remote access, and informed decision-making. Together, these elements create a system that not only monitors and controls industrial processes but also optimizes them for maximum efficiency and reliability.
For new engineers stepping into the industry, understanding these principles is critical. SCADA is more than just a system—it’s the backbone of modern industrial automation. Mastering its principles will equip you with the knowledge needed to thrive in a world driven by precision and innovation.