Key Takeaway
The minimum pressure for a solenoid valve varies depending on its design and purpose. Generally, solenoid valves are designed to operate at a specific pressure range. Too low pressure may not provide enough force to open the valve.
It’s essential to consult the valve specifications or manufacturer for exact requirements. In some cases, solenoid valves may require a minimum pressure of around 0.5 bar to function correctly. If the pressure is below this threshold, the valve may fail to open, leading to operational issues. Maintaining the right pressure ensures efficient performance and longevity of the valve.
Understanding the Minimum Pressure Requirements for Solenoid Valves
Solenoid valves play a vital role in automation systems, acting as control elements that manage the flow of liquids and gases. These valves are electrically operated, using a solenoid coil to convert electrical energy into mechanical movement, allowing them to open or close with precision. Their fast response times and reliability make them ideal for automation applications where precise control is required. Solenoid valves can be used in a variety of settings, including manufacturing, HVAC systems, and automotive industries, where they contribute to the efficiency and effectiveness of automated processes.
Automation systems benefit greatly from solenoid valves due to their ability to be remotely controlled and integrated into larger control systems. This integration allows for seamless coordination between different components within the system, enhancing overall productivity and reducing the need for manual intervention. Additionally, solenoid valves are available in various configurations and materials, allowing for customization based on specific application requirements. This adaptability ensures that solenoid valves can meet the diverse needs of different industries, providing reliable and efficient fluid control solutions.
To optimize the performance of solenoid valves in automation systems, it is essential to consider factors such as valve type, pressure requirements, and environmental conditions. Proper selection and installation are crucial to ensure that the valves operate efficiently and without failure. Regular maintenance and inspection can help identify potential issues before they lead to significant problems, prolonging the lifespan of the valves and the overall system. By understanding the role of solenoids in automation systems and addressing these considerations, industries can achieve enhanced performance, cost savings, and increased system reliability.
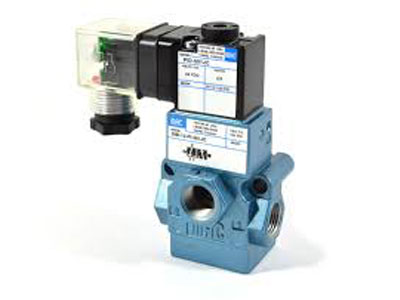
How Low Pressure Affects the Performance of Solenoid Valves
Low pressure can significantly affect the performance of solenoid valves, influencing their ability to control fluid flow effectively. Solenoid valves rely on a minimum pressure differential to operate, and insufficient pressure may lead to incomplete valve actuation. This can result in restricted flow or even valve failure, disrupting the fluid control process. Therefore, understanding the impact of low pressure is crucial for maintaining valve efficiency and preventing operational issues.
To mitigate the effects of low pressure, solenoid valves must be selected and configured appropriately. Valves designed for low-pressure applications often have specialized features, such as larger orifices or reduced spring force, to ensure proper operation even with minimal pressure. Additionally, external pilot assistance may be employed to enhance valve performance under low-pressure conditions. These adaptations help maintain consistent flow control and prevent performance degradation.
Regular maintenance and monitoring are essential to ensure solenoid valves function optimally at low pressures. This includes checking for signs of wear or damage, as well as confirming that the pressure levels remain within the valve’s specified range. By proactively addressing potential issues, operators can prevent unexpected failures and ensure reliable fluid control. Understanding the relationship between pressure and valve performance is key to optimizing solenoid valve operation and extending their service life.
You May Like to Read
Applications Requiring Low-Pressure Solenoid Valves
Low-pressure solenoid valves are essential in systems that require controlled fluid or gas flow under low-pressure conditions. One of the primary applications is in water treatment systems, where these valves regulate the flow of water through filtration, purification, and chemical dosing stages. These systems rely on low-pressure solenoid valves to ensure that water is processed efficiently without overburdening the system, preventing damage to sensitive components and ensuring optimal flow control. Additionally, in irrigation systems, these valves help in the even distribution of water, promoting water conservation and efficient use.
In HVAC systems, low-pressure solenoid valves are critical for controlling refrigerant flow, particularly in air conditioning and refrigeration units. These valves are used to regulate the flow of refrigerants in evaporators and coils, ensuring that the system operates at optimal temperature and pressure. Their role in maintaining low-pressure conditions is crucial to prevent overpressurization, which could lead to system failure or inefficiencies. Proper regulation by low-pressure solenoid valves helps maintain energy efficiency and the longevity of HVAC systems, contributing to cost savings and environmental sustainability.
Low-pressure solenoid valves are also widely used in medical devices, where precision is crucial. In devices such as oxygen concentrators, anesthesia machines, and nebulizers, these valves regulate the flow of gases at low pressures, ensuring the safety and comfort of patients. The precise control of airflow is vital in medical equipment, where even minor variations in pressure could lead to adverse effects. These valves are designed to operate reliably, ensuring that medical systems function safely and consistently in critical applications.
How to Select Solenoid Valves Based on Minimum Pressure
Selecting solenoid valves based on minimum pressure requirements is critical for ensuring effective system performance. The minimum pressure specification refers to the least amount of pressure required for the valve to operate correctly. Choosing a valve with an appropriate minimum pressure rating is essential to avoid operational issues.
When selecting solenoid valves, consider the application’s pressure demands and ensure the valve can handle the minimum pressure levels. Valves with inadequate pressure ratings may not seal properly, leading to leaks or reduced flow control. Proper valve selection helps maintain system reliability and efficiency.
Understanding the role of minimum pressure in solenoid valve operation aids in making informed decisions during valve selection. By considering pressure requirements alongside other factors like media type and flow rate, operators can choose the right valve for their specific needs. This careful selection process ensures optimal performance and longevity of the fluid control system.
The Role of Valve Design in Low-Pressure Applications
Valve design is a critical factor in the performance of low-pressure applications, where precise control and minimal resistance are necessary. In such applications, the valve must be able to operate effectively at low pressures without causing significant pressure drops or flow disruptions. The design typically incorporates features like large flow paths and low friction materials to maintain efficiency and accuracy. This is particularly important in industries like water treatment, food processing, and pharmaceuticals, where consistent flow rates and pressure are crucial for maintaining product quality and process integrity.
Moreover, effective valve design considers the fluid characteristics and operating environment. For low-pressure applications, materials that resist corrosion and wear, such as stainless steel or specialized polymers, are often used to ensure durability and longevity. The valve’s configuration—whether it be globe, ball, or butterfly—must be selected based on the specific requirements of the application to optimize performance and reduce maintenance needs. This tailored approach ensures that the valve operates reliably under varying conditions without compromising efficiency.
Additionally, the role of valve design in low-pressure applications extends to ease of integration and automation. Modern valve designs often incorporate smart technologies and compatibility with control systems for seamless operation and monitoring. This integration allows for real-time adjustments and predictive maintenance, enhancing system responsiveness and reducing downtime. Ultimately, the right valve design in low-pressure settings not only improves operational efficiency but also contributes to cost-effectiveness and sustainability.
Conclusion
The minimum pressure for a solenoid valve to operate depends on its design, with some models requiring a minimum differential pressure. Others, like zero-pressure valves, work without a baseline pressure.
Knowing the pressure requirements ensures proper valve selection, preventing operational issues and ensuring compatibility with system specifications. This knowledge optimizes system performance.