Key Takeaway
The main function of an HMI (Human Machine Interface) control panel is to allow operators to interact with and control machines or systems. It acts as a bridge between the user and the equipment, displaying important information like system status, alarms, and performance data in real-time.
HMI control panels enable users to monitor processes, adjust settings, and troubleshoot issues. By providing visual data and control options, they help improve operational efficiency, reduce human error, and enhance safety. These panels are commonly used in industries like manufacturing, automation, and energy to simplify complex tasks and improve the management of machinery.
Defining the Role of HMI in Industrial Automation
The role of HMI in industrial automation is pivotal. HMIs are the primary interface between human operators and automated systems. In the past, operators would have to rely on physical controls like switches, dials, and gauges. Today, HMIs replace these with digital interfaces, making it much easier to manage complex systems.
Real-Time Feedback and Monitoring:
HMIs provide operators with real-time feedback on various parameters like temperature, pressure, speed, and other critical system metrics. This information is displayed visually through graphs, dials, and alerts, enabling operators to make informed decisions quickly. For example, if a pressure reading exceeds a safe threshold, the HMI will display an alert, prompting the operator to take corrective action.
Data Visualization and Interaction:
Rather than dealing with rows of numbers or text-based data, operators can interact with the system through touchscreens and graphical representations. These visualizations make it easier to understand system performance and detect potential issues. Whether it’s a graphical flowchart, a trend graph, or a simple numeric readout, the HMI ensures that operators can interpret data more intuitively.
Enhanced Control:
In addition to monitoring, HMIs allow operators to control the machinery directly. For example, an operator can adjust machine speed, start or stop processes, or reset alarms—all from the same HMI interface. This centralization of control makes the system more efficient and reduces human error.
Overall, the HMI is integral in simplifying the complexity of industrial automation systems, making operations more transparent, efficient, and user-friendly.
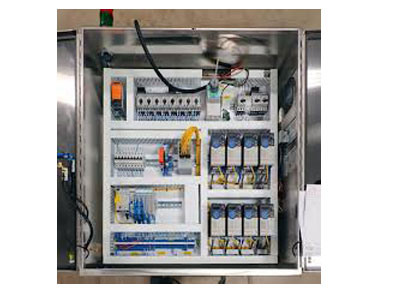
How HMI Control Panels Facilitate Real-Time Monitoring
Real-time monitoring is one of the key functions of HMI control panels. In an industrial setting, where processes are continuously running and machinery operates at high speeds, having a system that provides real-time data is essential. HMI panels offer operators immediate access to vital system parameters, allowing them to monitor operations as they unfold.
Constant Data Updates:
Unlike traditional systems, which might require manual inspection or data logging, HMIs automatically update in real time. Whether it’s checking motor speed, temperature, or power consumption, operators have immediate access to the most current data available. This constant feedback loop allows for timely responses to any fluctuations in system performance.
Alarm and Alert Systems:
HMIs are equipped with alarm and alert functions that notify operators when parameters fall outside of safe ranges. For example, if a machine starts overheating or a pressure reading reaches a dangerous level, the HMI will issue a visual or audible alarm. These alerts allow operators to take swift action before the situation becomes critical, preventing damage or downtime.
Trend Monitoring:
Modern HMI systems often include trend graphs that allow operators to track parameters over time. These trends are valuable because they can help predict potential issues. For example, a gradual increase in pressure over time may indicate a blockage or malfunction, and operators can take preemptive action based on these trends. This level of monitoring is essential for ensuring optimal system performance and preventing failures before they occur.
By providing real-time monitoring, HMIs allow operators to maintain control over the system, respond to issues instantly, and keep industrial processes running smoothly.
You May Like to Read
Enhancing Communication Between Operators and PLCs with HMIs
Programmable Logic Controllers (PLCs) are the heart of industrial control systems, managing everything from simple machines to complex automation systems. However, PLCs are not designed for human interaction—they require an interface that allows operators to communicate with them. This is where HMIs come into play.
PLC Integration:
HMIs are designed to interface directly with PLCs, allowing operators to monitor and control processes managed by the PLC. Through this integration, an operator can view the status of inputs and outputs, control motor speeds, adjust temperature settings, and more, all by interacting with the HMI.
Bidirectional Communication:
The communication between the HMI and PLC is bidirectional. This means that the HMI can send commands to the PLC (e.g., starting a pump) and receive feedback from the PLC (e.g., confirmation that the pump is running). This two-way communication ensures that operators have a clear understanding of system status and can make necessary adjustments in real time.
Error Handling and Diagnostics:
When a fault occurs, the HMI can display error codes and diagnostic information from the PLC. For example, if a machine component malfunctions, the HMI might display an error code or indicate the specific part that needs attention. This seamless communication between the HMI and PLC improves troubleshooting and ensures that operators are equipped with the information they need to resolve issues quickly.
In essence, HMIs serve as the link between human operators and the complex machinery controlled by PLCs. By facilitating smooth communication, HMIs enhance the overall functionality and reliability of industrial control systems.
Key Features of HMI Control Panels for Improved Control and Diagnostics
HMI control panels come equipped with a wide range of features that improve both control and diagnostics in industrial settings. These features help streamline operations, reduce errors, and improve system uptime.
User-Friendly Interface:
The interface on most HMI panels is designed to be user-friendly. Operators are provided with intuitive touchscreens, buttons, and icons, making it easier for them to control the system and navigate through different options. The interface is often customizable, allowing operators to prioritize the information that’s most relevant to their role.
Advanced Diagnostic Tools:
HMIs are equipped with advanced diagnostic tools that help operators identify and resolve issues faster. These may include error logs, fault diagnostics, and real-time data visualizations. By providing clear and detailed diagnostic information, HMIs reduce troubleshooting time and minimize downtime.
Graphical Displays and Visualizations:
The ability to visualize data is one of the most powerful features of HMIs. Instead of relying on raw numerical data, operators can view graphs, trends, and digital readouts that help them understand system performance at a glance. This can include everything from real-time system metrics to historical performance trends, allowing for more informed decision-making.
Custom Alarms and Alerts:
HMIs allow for customizable alarms, so operators can set specific parameters that trigger notifications. Whether it’s a critical machine failure, a system anomaly, or an operational threshold being crossed, HMIs ensure that operators are immediately alerted to any issue. This capability is essential for maintaining safe and efficient operations.
The features available on modern HMI control panels are designed to improve the precision, efficiency, and reliability of industrial systems, enabling operators to perform their duties with confidence and accuracy.
How HMI Control Panels Contribute to System Safety and Reliability
Safety and reliability are paramount in industrial environments, where even small mistakes can lead to costly downtime or accidents. HMI control panels contribute significantly to both safety and system reliability through their monitoring, alerting, and diagnostic capabilities.
Real-Time Safety Monitoring:
By providing operators with immediate feedback on system parameters, HMIs help to ensure that all systems remain within safe operating ranges. If any parameters fall outside of these ranges, the HMI immediately triggers an alarm, warning the operator of a potential safety issue. This proactive monitoring helps to prevent accidents and damage.
Preventive Maintenance:
HMI control panels also support preventive maintenance. By continuously tracking equipment performance and providing trends and diagnostic data, HMIs allow operators to spot potential issues before they result in failure. For example, a slight increase in vibration or temperature over time can indicate wear or damage to a component, prompting maintenance before a breakdown occurs.
Improved Operator Response:
The intuitive interface and real-time alerts provided by HMIs enable operators to respond more effectively to safety-critical situations. With the right information at hand, operators can quickly take corrective actions, such as shutting down machinery, adjusting parameters, or activating safety protocols.
Enhanced System Uptime:
Through better monitoring, diagnostics, and preventive maintenance, HMIs help improve system uptime. By preventing failures and reducing the time spent troubleshooting issues, HMIs enhance overall system reliability, contributing to a more efficient and productive operation.
In summary, HMIs play a critical role in maintaining the safety and reliability of industrial systems. Their ability to monitor, alert, and provide diagnostic information ensures that operators can respond to issues swiftly and effectively, reducing risks and improving system performance.
Conclusion
The main function of an HMI control panel is to provide a user-friendly, intuitive interface for operators to interact with industrial automation systems. By facilitating real-time monitoring, improving communication with PLCs, and offering advanced diagnostic tools, HMI control panels enhance the efficiency and reliability of industrial operations. They also play a critical role in system safety by alerting operators to potential issues and enabling preventive maintenance.
As industrial systems continue to grow in complexity, the role of HMI control panels will become even more crucial. Understanding their function and features will enable engineers, especially those newly joining the industry, to contribute more effectively to their organizations. With HMI technology, industrial automation becomes more accessible, safe, and efficient for everyone involved.