Key Takeaway
Rotary valves and linear valves differ in their movement and applications. Rotary valves use a rotating motion to control flow, making them ideal for applications requiring quick shut-off and precise control. Linear valves, on the other hand, use a straight-line motion, suitable for applications needing gradual flow control.
Understanding these differences helps in selecting the right valve for your needs. Consider factors like flow rate, pressure, and application environment when choosing between rotary and linear valves to ensure efficient and reliable operation.
Defining Rotary and Linear Valve Mechanisms
Rotary and linear valve mechanisms are two different types of actuated valve systems used in industrial applications to control the flow of fluids and gases. A rotary valve mechanism relies on a rotating element, such as a ball or disk, that changes the flow path as it rotates. Rotary valves are often used in applications where compactness and ease of control are important, such as in pipelines carrying gas, liquids, or powders. They are typically actuated by rotary actuators that rotate the valve element to either open or close the flow passage.
In contrast, linear valve mechanisms use a stem or piston to move a valve element in and out of the flow path, allowing for a more direct control of flow. These valves are often used in situations where precise flow control is required, such as in regulating pressure or temperature. Linear valves can offer more precise control in certain situations but are generally bulkier than rotary valves and require more space for installation. The actuation of linear valves can be achieved using linear actuators that push or pull the valve stem to the desired position.
Both rotary and linear valve mechanisms have their unique advantages, and their application depends on the specific needs of the process. Rotary valves are often favored for their compact design, ease of control, and suitability for high-volume flows, while linear valves are preferred in applications requiring more precise control over flow rates.
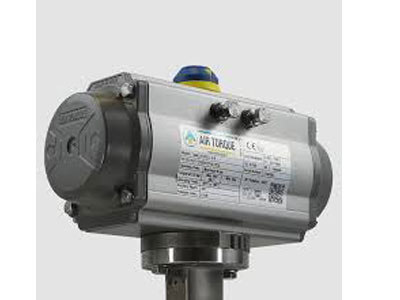
Key Applications for Rotary Valves
Rotary valves are widely used in various industries, especially where space constraints and quick shut-off capabilities are essential. These valves excel in handling fluids and gases under high pressure or temperatures, making them ideal for power plants, chemical processing, and oil and gas industries.
In power plants, rotary valves are often used to control the flow of steam or air through critical systems. Their quick action and ability to perform in high-pressure environments make them an ideal choice for regulating the flow of gases to turbines or other machinery.
Rotary valves are also common in chemical and pharmaceutical industries. They are used for controlling the flow of raw materials or products in processes where precision and speed are critical. The smooth, consistent operation of rotary valves is especially beneficial in these industries, where the flow of hazardous or sensitive materials needs to be tightly controlled.
The food processing industry often employs rotary valves for dosing and feeding dry powders or bulk solids. Their ability to control the flow of materials without causing blockages or jams is crucial in maintaining the efficiency of manufacturing lines. Rotary valves are also used in pneumatic conveying systems to ensure proper flow control and minimize leaks.
Additionally, rotary valves find applications in HVAC systems, where they regulate the flow of air or refrigerants. Their compact design and reliability under varying conditions make them a preferred option in such systems.
You May Like to Read
Key Applications for Linear Valves
Linear valves are commonly found in applications where precise, adjustable flow control is necessary. Their ability to gradually adjust the flow rate makes them suitable for industries such as water treatment, oil refining, and HVAC systems, where consistent and controlled flow is essential.
In water treatment plants, linear valves are used to regulate the flow of water through various stages of the treatment process, such as filtration, disinfection, and chemical dosing. The smooth, linear motion ensures that the flow is adjusted precisely to meet system requirements, which is crucial for maintaining water quality.
In the oil and gas industry, linear valves are employed in pipelines to control the flow of crude oil, natural gas, or refined products. Their design allows for accurate throttling, which helps maintain optimal pressure levels and ensures the safety of the pipeline. Linear valves are also used in refineries, where they regulate the flow of raw materials and chemicals through processing units.
Linear valves play a significant role in HVAC systems by controlling the flow of water or refrigerants in heating and cooling systems. These valves are typically used in chillers, cooling towers, and heating systems to ensure that the correct amount of fluid flows through the system, optimizing energy efficiency and maintaining the desired temperature.
In pharmaceutical manufacturing, linear valves are used to control the flow of sensitive materials and ensure accurate dosing. Their ability to provide fine control over the flow rate is essential for maintaining consistency and quality in the final product.
Benefits and Limitations of Each Type
Rotary valves offer several benefits that make them highly suitable for specific applications. One of the key advantages is their ability to handle high-pressure and high-temperature environments. Their compact design also makes them ideal for installations with limited space. Additionally, rotary valves offer fast and reliable operation, making them essential for systems that require quick shut-off or isolation. These valves are generally more durable and reliable, which reduces maintenance costs and downtime in critical systems.
However, rotary valves do have limitations. They are not as effective when it comes to precise control over flow rates. While they provide on/off functionality and basic flow regulation, they are not ideal for applications that require fine-tuned adjustments. Rotary valves may also struggle with slurries or highly viscous fluids, which can lead to clogging or reduced efficiency.
Linear valves, in contrast, excel in applications that require gradual, precise control over flow rates. They offer more accurate throttling capabilities, making them ideal for processes that need to maintain a consistent flow. Linear valves are generally more versatile and can handle a wider range of fluids, including those with higher viscosities or particulate content. They are also more suitable for applications that involve the regulation of pressure in addition to flow.
However, linear valves tend to be larger and more complex than rotary valves, which can make them more expensive and harder to maintain. Their larger size may also pose challenges in installations with space limitations. Additionally, linear valves may require more frequent maintenance compared to rotary valves, particularly in high-flow applications where wear and tear are a concern.
Selection Criteria Based on Use Case
When selecting between rotary and linear valves, the application’s requirements play a significant role. If precise, incremental flow control is needed, linear valves are typically the better choice. These valves are ideal for systems that require throttling or gradual changes in flow, such as water treatment, oil refining, and HVAC systems. Linear valves offer better control over flow rates and are better suited for materials with varying viscosities or particulate content.
For applications where space is limited and quick shut-off is essential, rotary valves are often the preferred option. Their compact design allows for easy installation in tight spaces, and their fast operation is crucial in systems where rapid flow regulation or isolation is needed. Rotary valves are commonly used in industries such as power plants, chemical processing, and bulk solids handling, where durability and reliability under harsh conditions are paramount.
Another consideration is the type of material being handled. Rotary valves are often preferred for handling gases or dry materials, as they provide reliable operation without causing blockages. On the other hand, linear valves are better suited for fluids that require precise adjustments to flow rates, such as liquids in pipelines or processing units.
Cost and maintenance requirements also play a role in the selection process. While rotary valves are typically more affordable and require less maintenance, linear valves may be more expensive and need more frequent servicing, especially in high-flow applications.
Conclusion
The difference between rotary and linear valves lies in their operation and applications. Rotary valves provide rotational movement, while linear valves offer straight-line motion. Understanding these differences is crucial for selecting the right valve for specific needs.
By considering factors such as motion type, load, and environment, users can effectively integrate valves into their systems, enhancing productivity and reliability.