Key Takeaway
The main difference between PLC and relay control panels lies in their functionality and complexity. A PLC control panel uses a Programmable Logic Controller (PLC) to handle complex automation tasks. It can be programmed to perform multiple functions, process data, and adapt to changing requirements. PLC panels are ideal for modern industries requiring flexibility and advanced control.
A relay control panel, on the other hand, relies on electromechanical relays to manage circuits. It is simpler, designed for fixed and straightforward tasks, and doesn’t require programming. While PLC panels are suited for advanced applications with logic-based operations, relay control panels are more cost-effective for basic control needs. Both serve unique purposes depending on the application.
Overview of PLC Control Panels and Their Role in Automation
PLC control panels are at the heart of modern automation systems. A PLC is a digital computer designed to control the manufacturing processes or any activity that requires high reliability, ease of programming, and process fault diagnosis. Unlike traditional relays, which rely on hardwired circuits, a PLC is programmable and can handle complex tasks with a series of inputs and outputs.
PLC systems offer versatility, as they can handle multiple control processes simultaneously and are often used in applications ranging from simple machinery control to complex industrial automation. The control panel houses the PLC itself, input/output modules, and power supplies, among other components.
One of the primary benefits of PLC control panels is their ability to automatically control a wide range of machines and processes through predefined instructions or programs. For instance, in a manufacturing facility, a PLC might be used to control a conveyor belt, manage alarms, or oversee multiple machines working together.
What makes PLC control panels indispensable in industrial settings is their advanced diagnostic capabilities. They can track the health of each connected component and alert operators about potential issues. This built-in monitoring capability reduces downtime and ensures continuous, smooth operations.
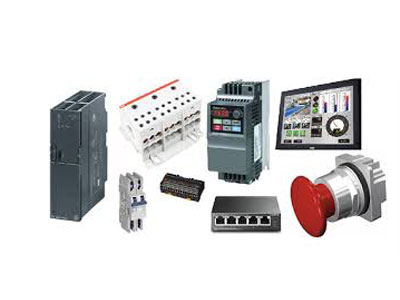
Understanding Relay Control Panels and Their Functionality
On the other hand, relay control panels are based on simpler technology compared to PLCs. Relays are electromechanical switches that operate by opening or closing electrical contacts when triggered by a control signal. Relay control panels use these relays to control the flow of electricity to other devices, such as motors, lights, or other mechanical systems.
While PLC control panels are programmable, relay panels are hardwired systems. They perform a straightforward function: turning electrical devices on or off based on the signals received from the control panel. Relay panels are used for simpler tasks that don’t require complex automation or programming.
In a relay control panel, the relays are typically arranged in rows, with each relay controlling one particular device or action. These systems are reliable, cost-effective, and easy to maintain, but they lack the flexibility and adaptability that a PLC system offers. Relay control panels are suitable for applications where only basic on/off control is needed, such as starting motors, activating alarms, or controlling lights.
Relay control panels are more mechanically driven than PLCs, using electrical contacts to switch devices on and off. While they might not offer the advanced capabilities of PLCs, relay panels are still widely used in smaller automation projects or in environments where flexibility and programmability are not as critical.
Key Differences in Control and Automation Capabilities Between PLC and Relay Panels
When comparing PLC and relay control panels, the most significant difference lies in their control and automation capabilities.
1. Automation Level
PLC panels are inherently programmable, meaning they can handle more complex tasks. For example, a PLC can manage multiple devices simultaneously and can be programmed to carry out a sequence of operations with minimal human intervention. On the other hand, relay control panels are more rigid. They control devices by switching relays in response to input signals but can only perform on/off operations without any higher-level control or decision-making.
2. Flexibility
PLC systems are extremely flexible, allowing you to easily modify or change the automation process by updating the program. This is especially beneficial in industries where processes change frequently. Relay control panels, however, are much harder to adjust once installed. Any changes would require manual rewiring or replacing components.
3. Complexity
PLCs are designed to handle complex, multi-step control processes. This includes timing, sequencing, and interlocking of different devices. Relay panels are best suited for basic functions, such as switching a device on/off based on a signal, but they do not have the capacity to handle complex logic or multi-device coordination.
4. Diagnostic and Monitoring Capabilities
PLCs provide real-time monitoring and diagnostic feedback. They can detect faults or irregularities in the system, such as a faulty sensor or a broken circuit, and display this information on a connected HMI (Human-Machine Interface). Relay control panels, in contrast, do not provide these sophisticated diagnostics. Troubleshooting relay control systems often requires manual inspection.
Comparing the Flexibility and Scalability of PLC vs Relay Control Panels
When it comes to flexibility and scalability, PLCs shine in most industrial applications. The major advantage of a PLC system is its ability to scale up or down as needed. For example, if a facility adds new machines or processes, the same PLC system can be programmed to control the new devices without significant hardware changes. In some cases, simply adding more I/O modules or expanding the program is enough to integrate new functionality.
In contrast, relay control panels are less flexible in this regard. If you need to add new devices or change the control logic, you’ll often need to add more relays or redesign the wiring. This can be time-consuming and costly, especially in larger systems where frequent changes are required.
PLC systems also offer better adaptability to complex processes that require real-time adjustments. For example, in a production line, a PLC can adjust the operation of machines depending on the input from sensors and feedback from operators. Relay control panels, however, cannot adapt in the same way without substantial manual intervention.
Cost, Maintenance, and Efficiency Considerations in Choosing Between PLC and Relay Panels
When choosing between a PLC and relay control panel, cost, maintenance, and efficiency are important considerations.
1. Cost
Relay control panels are typically cheaper to design and implement compared to PLC systems. This is because relay control panels consist of basic components and don’t require the same level of programming or advanced technology. For smaller projects or basic applications, a relay panel is often the more cost-effective solution.
However, the initial savings with relay panels can be offset by the long-term costs of maintenance, particularly if the system needs frequent adjustments or expansions. As relay control panels become more complex, their cost can rise, especially if custom wiring or additional relays are required.
2. Maintenance
PLC systems are typically more reliable and require less frequent maintenance. While they may require occasional updates or modifications to the program, they are designed to last longer and often include self-diagnostic tools to help detect and correct issues before they become serious.
Relay control panels require more manual attention. Components like relays and contactors can wear out over time, especially in high-cycle applications. Troubleshooting and maintaining a relay panel can also be more difficult, as manual inspection is usually required to detect issues.
3. Efficiency
In terms of efficiency, PLC control panels are generally superior. PLCs allow for more precise control, better error detection, and optimized sequencing. They can also be programmed to improve energy efficiency by controlling devices based on real-time data and system feedback. Relay panels, being more basic, are less efficient in managing energy or adjusting operations dynamically.
Conclusion
In summary, both PLC and relay control panels have distinct roles in industrial automation. PLC systems excel in complex, scalable, and flexible automation tasks, offering advanced diagnostics and monitoring capabilities. They are ideal for industries that require high adaptability, precision, and efficiency. Relay control panels, on the other hand, are simpler and cost-effective solutions for basic on/off control tasks. They are reliable for smaller applications but lack the flexibility and scalability of PLC systems. The choice between a PLC and a relay control panel ultimately depends on your specific system requirements, budget, and the level of automation needed for your processes.