Key Takeaway
The difference between Industrial Ethernet and Fieldbus technologies lies in speed, scalability, and functionality. Industrial Ethernet uses Ethernet-based communication for high-speed data transfer and supports large networks with real-time capabilities. It is ideal for modern automation systems requiring precision and flexibility.
Fieldbus technologies, like PROFIBUS or Modbus, rely on serial communication and are better suited for smaller, simpler systems. They offer robust and reliable data exchange but operate at slower speeds compared to Industrial Ethernet. Fieldbus is often used in legacy systems, while Industrial Ethernet is preferred for advanced automation tasks. The choice depends on system requirements, with Industrial Ethernet being more future-proof and scalable.
Overview of Fieldbus Technologies in Industrial Automation
Fieldbus technologies emerged in the late 20th century as a solution for connecting industrial devices. Before Fieldbus, communication was primarily point-to-point, which meant excessive wiring and limited scalability. Fieldbus introduced a digital, multi-drop communication system, reducing wiring and improving efficiency.
1. How It Works: Fieldbus systems connect multiple devices, such as sensors and actuators, to a single controller through a shared communication line. Popular Fieldbus protocols include PROFIBUS, Modbus, and CAN bus.
2. Legacy Strengths: Fieldbus is known for its reliability and simplicity, particularly in smaller, isolated systems. It excels in environments where deterministic communication (predictable and timely data exchange) is critical.
3. Limitations: Fieldbus networks are typically slower and less scalable compared to Ethernet-based systems. They also face compatibility challenges as industries adopt more advanced technologies.
For example, in a water treatment plant, Fieldbus might be used to connect pumps and sensors to a central PLC. While effective, such systems struggle with large-scale integration and high-speed requirements.
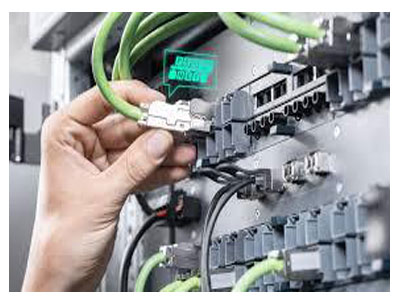
Key Differences Between Fieldbus and Industrial Ethernet
The primary distinction between Fieldbus and Industrial Ethernet lies in their communication technology and capabilities.
1.Technology Base: Fieldbus operates on proprietary or standardized protocols over serial communication. Industrial Ethernet, on the other hand, is based on Ethernet standards used in IT networks, adapted for industrial use.
2. Data Transmission: Industrial Ethernet supports both cyclic (real-time) and acyclic (non-real-time) communication, offering greater flexibility than Fieldbus.
3. Compatibility: Fieldbus systems often struggle with interoperability between devices from different manufacturers. Industrial Ethernet leverages global standards, making integration seamless.
4. Bandwidth and Speed: Ethernet offers higher bandwidth and faster data transfer rates, which are crucial for modern applications involving large data volumes or high-resolution sensors.
For instance, while Fieldbus might suffice for a small conveyor system, Industrial Ethernet is better suited for a smart factory with interconnected machines and IoT devices.
Communication Speeds: Fieldbus vs. Ethernet
Communication Speeds: Fieldbus vs. Ethernet
Fieldbus vs. Ethernet H2: Scalability and Flexibility in Industrial Ethernet vs. Fieldbus
Scalability and flexibility are essential for modern industrial networks, especially as industries embrace IoT and digital transformation.
1. Fieldbus Limitations: Fieldbus systems are often confined to specific applications and struggle to accommodate additional devices or increased data loads. Their proprietary nature further limits scalability.
2. Ethernet Advantages: Industrial Ethernet networks can easily scale to support thousands of devices, making them ideal for large facilities. The use of standardized protocols ensures compatibility with a wide range of devices and systems.
3. Flexibility: Ethernet supports mixed data types, allowing the same network to handle control commands, video streams, and diagnostic information. Fieldbus systems are typically limited to specific data types.
For example, a pharmaceutical plant expanding its production lines would benefit from Ethernet’s scalability, allowing seamless integration of new devices and systems without overhauling the existing network.
Scalability and Flexibility in Industrial Ethernet vs. Fieldbus H2: Transitioning from Fieldbus to Industrial Ethernet
Many industries are transitioning from Fieldbus to Industrial Ethernet to leverage the benefits of modern technologies.
1. Drivers of Transition:
Increased demand for higher speeds and bandwidth.
The need for seamless integration with IT networks.
Compatibility with IoT devices and cloud-based systems.
2. Challenges: Transitioning requires upgrading legacy devices or using gateways to bridge Fieldbus and Ethernet systems. Engineers must also address training gaps to manage the new technology effectively.
3. Hybrid Systems: Many facilities adopt hybrid systems where Fieldbus and Ethernet coexist. This allows a gradual transition while maintaining operational continuity.
For instance, a power plant might integrate Ethernet for new equipment while retaining Fieldbus for legacy systems, using gateways to enable communication between the two networks.
Conclusion
Fieldbus technologies have served industries well for decades, offering reliable and deterministic communication. However, the demands of modern automation—higher speeds, greater scalability, and seamless integration—have made Industrial Ethernet the preferred choice.
For engineers, understanding the differences between these technologies is critical for designing networks that meet current and future needs. Industrial Ethernet’s flexibility, speed, and compatibility make it the backbone of smart factories and advanced industrial systems, ensuring long-term success in a rapidly evolving landscape.