Key Takeaway
The main difference between a PC and an industrial PC lies in their design and usage. A regular PC is built for everyday tasks like browsing, office work, and gaming. In contrast, an industrial PC is designed for harsh environments and industrial applications. It is rugged, resistant to dust, vibrations, and extreme temperatures. Industrial PCs are used in manufacturing, oil and gas, and transportation industries. They offer reliable performance under tough conditions, ensuring continuous operation and minimal downtime. Their robust build and durability make them ideal for critical industrial processes.
Hardware Differences
Firstly, the hardware of a PC and an IPC varies significantly. A typical PC is designed for general-purpose use, focusing on consumer needs like office tasks, gaming, and multimedia. It usually features components optimized for cost-efficiency and performance in standard environments.
On the other hand, an Industrial PC is built to withstand harsh industrial conditions. It boasts robust hardware components that prioritize durability and reliability over consumer-level specifications. These components are often designed to operate flawlessly in environments where temperature fluctuations, dust, moisture, and vibration are common occurrences.
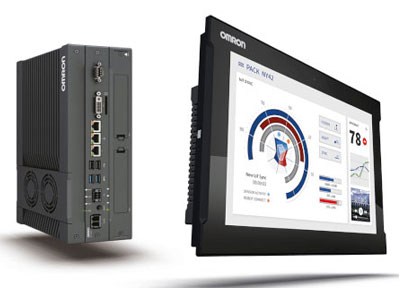
Durability and Reliability
Industrial PCs (IPCs) stand apart from regular PCs due to their exceptional durability and reliability, engineered specifically to endure the rigors of industrial environments. Unlike standard computers that may falter under demanding conditions, IPCs are built to deliver consistent performance without compromising on uptime.
Durability Under Extreme Conditions
In industrial settings, where machines operate continuously, reliability is paramount. IPCs are designed to withstand harsh conditions such as extreme temperatures, vibrations, and electromagnetic interference that are common in factories and industrial plants. This robustness ensures minimal downtime, crucial for maintaining productivity and efficiency in manufacturing processes.
Longevity and Minimal Downtime
One of the key advantages of IPCs is their longevity. These computers are not just robust; they are built to last, reducing the frequency of replacements and maintenance downtime. This reliability translates to significant cost savings over time, making IPCs a preferred choice for industries where continuous operation is essential.
Environmental Resistance
Apart from durability, another critical feature of IPCs is their environmental resistance, making them suitable for a wide range of challenging settings.
Protection Against External Elements
IPCs are equipped with sealed enclosures that protect them from dust, moisture, and other contaminants that could otherwise compromise performance. This environmental resistance is crucial in environments such as manufacturing floors or outdoor installations where exposure to dust and humidity is inevitable.
Wide Temperature Range Operation
Unlike regular PCs that may struggle in extreme temperatures, IPCs are designed to operate reliably across a broad temperature spectrum. Whether in freezing cold conditions or sweltering heat, these computers maintain optimal performance, ensuring continuous operation without overheating or freezing up.
Performance and Specifications
Industrial PCs (IPCs) stand out in the realm of computing due to their specialized design and robust performance tailored specifically for industrial environments. Unlike conventional PCs meant for general use, IPCs are engineered to withstand the rigors of industrial applications, where reliability and durability are paramount.
Performance Excellence in Industrial Environments
In industrial settings, where processes often rely on continuous and uninterrupted operation, the performance of IPCs is crucial. These computers are optimized to handle real-time data processing, manage complex automation systems, and control machinery with precision. Their computational power is finely tuned to ensure efficiency and responsiveness, even under high-stress conditions. For instance, in manufacturing plants, IPCs play a vital role in coordinating operations across multiple machines, ensuring synchronized workflows and minimizing downtime.
Meticulously Chosen Specifications
The specifications of IPCs are meticulously chosen to meet the demanding requirements of industrial applications. This includes selecting components that can endure extended operation cycles, extreme temperatures, and challenging environments typical of industrial settings. Components such as industrial-grade processors, robust storage solutions, and specialized cooling systems are integrated to enhance reliability and longevity.
Applications and Uses
While both personal computers (PCs) and industrial PCs (IPCs) are computers at their core, their applications and uses diverge significantly based on their design and intended environments.
Versatility of Personal Computers (PCs)
Personal computers are versatile tools suitable for a wide range of tasks in office settings, homes, schools, and various commercial applications. They excel in tasks such as word processing, internet browsing, multimedia consumption, and gaming. PCs are designed for general-purpose computing, offering flexibility and ease of use that cater to everyday needs of individuals and businesses alike.
Specialized Applications of Industrial PCs (IPCs)
In contrast, industrial PCs (IPCs) find their niche in specialized environments requiring robustness, reliability, and precise control. They are indispensable in industrial automation, where they serve as the backbone of control systems for manufacturing processes, robotics, and critical infrastructure. IPCs are engineered to operate flawlessly in harsh conditions, including dust, moisture, vibrations, and extreme temperatures, ensuring uninterrupted operation essential for industrial productivity and safety.
Conclusion
In conclusion, while both PCs and Industrial PCs share fundamental computing principles, their design, capabilities, and applications vary significantly. Industrial PCs are the cornerstone of modern industrial automation and control systems, offering unmatched durability, reliability, and performance tailored for challenging environments. Understanding these differences is essential for engineers entering the industrial sector, ensuring they choose the right tool for the job based on specific operational requirements.
By grasping these distinctions, engineers can leverage the strengths of Industrial PCs to enhance efficiency, reliability, and operational continuity in industrial settings. Whether it’s managing automated production lines, monitoring critical infrastructure, or controlling sophisticated machinery, Industrial PCs play a pivotal role in driving technological advancements and operational excellence across various industries.
This overview aims to provide a clear, concise understanding of the differences between PCs and Industrial PCs, empowering engineers with the knowledge needed to make informed decisions in their professional endeavors.