Key Takeaway
A pulse power supply accumulates energy over a longer period and releases it in a short, intense burst. This method increases the instantaneous power output significantly. Pulse power supplies are used in various applications, such as food processing, water treatment, medical equipment, and even weapon systems. They are crucial for tasks that require high power for brief moments. For example, in food processing, they help in sterilization by delivering high-energy pulses to kill bacteria instantly. This technology is essential for industries needing powerful, short-duration energy bursts.
Definition and Characteristics
A pulse power supply is a type of power source designed to deliver energy in short, controlled bursts. Unlike continuous power supplies, which provide a steady output, pulse power supplies deliver intermittent energy pulses. These pulses can vary in duration, frequency, and amplitude, making them versatile for various industrial applications. Key characteristics include high peak power, short pulse duration, and precise control over pulse parameters. This allows for efficient energy transfer and minimizes heat generation, which is crucial in applications where thermal management is essential.
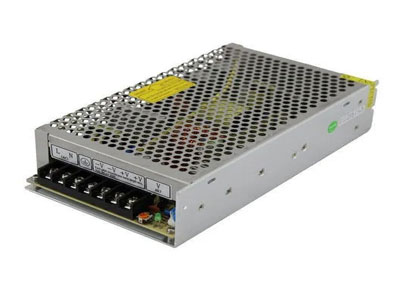
Working Principle
Understanding the working principle of pulse power supplies is essential for engineers in various industrial applications. These power supplies store energy in components such as capacitors or inductors and release it in short bursts. This method involves the rapid discharge of stored energy through a switch, typically a transistor or thyristor, controlled by a pulse generator. The pulse generator ensures that energy is delivered at precise intervals, allowing for high efficiency and exact control.
The timing and duration of these pulses are crucial. For instance, in industrial applications like laser cutting, precise energy bursts are necessary to achieve clean cuts and detailed engravings. The ability to control pulse parameters with accuracy ensures that the power supply delivers the required energy without wasting resources. This precise control makes pulse power supplies ideal for applications demanding short, high-power energy bursts. Understanding these principles allows engineers to optimize performance, ensuring reliability and efficiency in their industrial processes.
Applications and Use Cases
Pulse power supplies find extensive use in various industrial applications that require controlled energy bursts. In laser systems, these supplies are vital for cutting and engraving materials with high precision. The short, high-power pulses provided by the power supplies enable accurate and efficient processing, crucial for high-quality output. This precise energy delivery ensures that laser operations can achieve the desired results without wasting resources or compromising on detail.
In the medical field, pulse power supplies are essential in equipment such as defibrillators. These devices require precise energy delivery to restore normal heart rhythm effectively and safely. The controlled bursts of energy provided by pulse power supplies are critical for patient safety and treatment success.
In the manufacturing sector, pulse power supplies are used in welding processes. Here, the ability to control energy precisely ensures strong and reliable welds, enhancing product quality and process efficiency. Additionally, these power supplies are integral to testing and measurement equipment, where accurate power bursts are necessary for precise data acquisition. Each application leverages the unique ability of pulse power supplies to deliver controlled, high-power energy efficiently, making them indispensable in industrial settings.
Advantages and Disadvantages
Pulse power supplies offer several notable advantages. Their high efficiency and precise control over energy delivery are significant benefits. By delivering energy in short bursts, these supplies reduce thermal stress on components, extending the lifespan of the equipment. This efficiency is particularly advantageous in applications requiring consistent performance over long periods. Additionally, the precise control of pulse parameters allows customization for specific application needs, enhancing overall effectiveness.
However, there are also challenges associated with pulse power supplies. The complexity of the circuitry can lead to higher initial costs and the need for specialized maintenance. Engineers must be mindful of these factors when designing and implementing these systems. Improper use or design can result in inefficiencies or even equipment damage, underscoring the importance of careful planning and execution. Balancing these advantages and disadvantages is crucial for maximizing the benefits of pulse power supplies in industrial applications. Understanding these pros and cons helps engineers optimize their designs, ensuring reliability and performance in various industrial processes.
Future Trends
The future of pulse power supplies is promising, driven by ongoing advancements and the need for more efficient energy delivery systems. One emerging trend is the development of more compact and efficient components, such as advanced capacitors and switching devices. These innovations are aimed at enhancing the performance and reliability of pulse power supplies while reducing their physical footprint.
Integration with digital control systems is another significant trend. This integration allows for more sophisticated pulse shaping and timing control, providing greater flexibility and precision in various applications. Additionally, as industries increasingly prioritize sustainability, there is a growing focus on designing pulse power supplies that are more energy-efficient and environmentally friendly. Staying informed about these trends is essential to leverage the latest technologies, improving the performance and efficiency of industrial processes.
Emerging trends include the development of more compact and efficient components, such as advanced capacitors and switching devices. These innovations are aimed at enhancing the performance and reliability of pulse power supplies while reducing their physical footprint. Integration with digital control systems is another significant trend. This integration allows for more sophisticated pulse shaping and timing control, providing greater flexibility and precision in various applications.
Conclusion
Understanding pulse power supplies is crucial for engineers in the industry, as these devices play a vital role in various high-power, precision applications. By delivering controlled energy bursts, pulse power supplies offer efficiency and precision that continuous power supplies cannot match. With applications ranging from medical equipment to industrial manufacturing, the importance of these devices is clear. Future advancements promise even greater efficiencies and capabilities, making it essential for engineers to stay informed about new developments. Mastering the principles and applications of pulse power supplies will enable engineers to design and implement more effective and reliable industrial systems.