keytakeaway
MES and PLC are essential systems in industrial automation, but they serve different functions. A PLC, or Programmable Logic Controller, is a digital computer used to automate machinery on factory assembly lines. It’s designed for real-time control in rugged industrial environments, ensuring that machines operate correctly and efficiently.
On the other hand, an MES, or Manufacturing Execution System, manages and monitors work on the factory floor. It provides real-time data and insights to optimize manufacturing processes, tracking everything from raw materials to finished products. While PLCs handle the direct control of machinery, MES oversees the entire production process, ensuring everything runs smoothly and efficiently.
Understanding MES and PLC in Manufacturing
Manufacturing Execution Systems (MES) and Programmable Logic Controllers (PLC) are two essential elements in the modern manufacturing environment. MES serves as a software platform that oversees the entire production process, monitoring everything from materials to equipment performance. It allows manufacturers to collect real-time data, analyze production metrics, and make informed decisions to improve workflow efficiency. MES is critical for businesses looking to optimize production lines, reduce waste, and ensure product quality.
On the other hand, PLCs are hardware devices responsible for controlling the actual machinery on the shop floor. PLCs are tasked with executing commands and automating processes such as starting and stopping machines, adjusting speeds, and controlling robotic arms. While MES provides an overarching strategy and visibility, PLCs perform the hands-on work of controlling the equipment. Together, MES and PLC systems ensure that production processes are not only efficient but also adaptive to real-time changes.
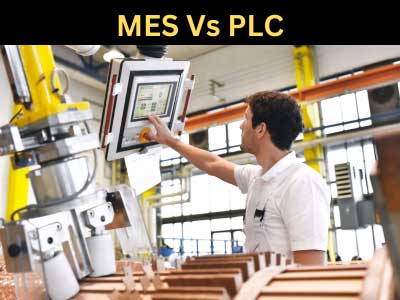
How PLCs Communicate with MES Systems
In manufacturing, communication between PLCs and MES systems is vital for maintaining a well-coordinated and efficient production line. PLCs are responsible for gathering real-time data from the machinery, such as temperature, pressure, speed, and operational status. This data is then communicated to the MES, which evaluates the production environment and can make adjustments as needed. MES processes this information to monitor performance, identify issues, and optimize workflows, ensuring that the entire system operates smoothly.
The two-way communication between MES and PLC ensures that any anomalies in the production process are quickly addressed. For example, if a PLC detects that a machine is operating outside the desired parameters, it immediately sends this data to the MES. The MES, using its analytical capabilities, can either adjust the settings automatically or alert an operator to intervene. This closed-loop system ensures minimal downtime and rapid response to any potential inefficiencies. Moreover, this communication enables predictive maintenance by allowing MES to detect wear and tear in machinery before it causes a breakdown, further enhancing productivity and reducing costly delays. In today’s automated manufacturing environments, this level of integration between MES and PLC is critical for maximizing operational efficiency.
MES vs. PLC: Key Differences
While MES and PLC are both essential in modern manufacturing, they serve different roles and functions within the production ecosystem. MES operates at a higher level, overseeing the entire production process and offering a bird’s-eye view of operations. It manages scheduling, quality control, resource allocation, and workflow optimization. MES also collects and analyzes data in real-time, allowing manufacturers to make strategic decisions about the entire production line, including identifying bottlenecks, improving productivity, and ensuring that quality standards are met.
In contrast, PLCs focus on the physical control of machinery. PLCs execute real-time commands, such as controlling motors, actuating valves, or adjusting conveyor speeds. They are the “hands” of the operation, performing tasks in response to instructions from MES or pre-programmed logic. PLCs work on the machine level, ensuring that every part of the production process operates as intended. While MES offers a broad, high-level view of production, PLCs are the tactical components that carry out specific machine-level functions. Without MES, manufacturers would struggle to oversee their operations, and without PLCs, machines would not function as efficiently. Both systems are interdependent, with MES offering the strategy and PLCs delivering execution.
Integrating MES with PLC for Improved Efficiency
Integrating MES with PLC systems unlocks new levels of efficiency and productivity in a manufacturing operation. MES uses real-time data provided by PLCs to continuously monitor and control the production process. By analyzing this data, MES can make adjustments to machine settings or production workflows to maintain optimal performance. This integration allows MES to send precise commands to PLCs, ensuring that machinery operates at the correct speed, pressure, or temperature for each production stage.
For example, MES can use PLC data to identify inefficiencies, such as a machine operating slower than expected. Based on this data, MES can adjust the production schedule, reallocating resources or shifting tasks to maintain overall efficiency. In turn, MES sends instructions to PLCs to modify machine settings, correcting the issue in real time. The benefit of this integration extends to predictive maintenance, where MES monitors equipment through PLC data and schedules maintenance when early signs of wear and tear are detected, preventing breakdowns and reducing downtime.
By working together, MES and PLC create a closed-loop system that enables real-time decision-making, better resource management, and automated workflows. This integration is essential for smart factories aiming to achieve lean manufacturing, where waste is minimized, and efficiency is maximized.
The Role of PLC in Automated Production with MES
PLCs are the foundation of automation in modern manufacturing, and when integrated with MES, they create a highly efficient and flexible production system. In automated production, PLCs control individual machines or production lines, executing specific tasks like switching machines on or off, adjusting speeds, and controlling robotic arms. PLCs are programmed to perform these tasks with precision, ensuring that machines operate as expected without the need for manual intervention.
When paired with MES, PLCs can do even more. MES provides the strategic oversight necessary for optimizing production, while PLCs ensure that tasks are executed accurately on the shop floor. For example, if MES detects a bottleneck in production, it can adjust the production schedule and instruct PLCs to modify machine speeds or pause operations in certain areas to balance the workload. This dynamic adjustment improves the overall efficiency of the production line, reducing downtime and ensuring that everything runs smoothly. Additionally, the use of MES with PLCs enables more advanced automation, such as predictive maintenance and just-in-time manufacturing, where resources are used only when needed. Together, MES and PLCs form the backbone of a smart, automated production system that maximizes output while maintaining high standards of quality.
conclusion
MES and PLC systems are integral to modern manufacturing, each playing a distinct but complementary role in ensuring production efficiency and quality. MES oversees the entire production process, offering high-level insights and decision-making capabilities, while PLCs execute the precise commands needed to control machinery. Together, they create a seamless system where real-time data and automated control work in harmony.
By integrating MES and PLC, manufacturers can take full advantage of automation, improving production efficiency, reducing downtime, and ensuring product quality. This synergy between MES and PLC is the key to unlocking the full potential of smart manufacturing, where automated decision-making and machine control deliver unparalleled levels of productivity and agility.