Key Takeaway
Industrial Ethernet is a specialized version of Ethernet designed for industrial environments. It connects devices like sensors, controllers, and machines within a network to enable seamless communication. Unlike standard Ethernet, Industrial Ethernet is built to handle extreme conditions such as high temperatures, vibrations, and electromagnetic interference.
It ensures reliable, high-speed data transfer, which is essential for automation and control systems. Industrial Ethernet supports real-time communication, scalability, and integration with advanced technologies like IoT and Industry 4.0. It is widely used in industries such as manufacturing, energy, and transportation to improve efficiency and maintain robust operations.
Definition and Core Concepts of Industrial Ethernet
Industrial Ethernet refers to a version of Ethernet technology specifically designed for industrial environments. Unlike standard Ethernet, which connects computers and devices in offices, Industrial Ethernet is built to handle the demanding conditions of manufacturing plants, factories, and other industrial settings.
At its core, it uses the same communication protocols, such as TCP/IP, to transmit data efficiently. However, the key difference lies in its enhanced durability and real-time capabilities. Industrial Ethernet can withstand extreme temperatures, vibrations, and electromagnetic interference—making it suitable for environments where standard Ethernet would fail.
One standout feature is its ability to support real-time communication. In industries like automotive manufacturing or food processing, machines must exchange data instantly to synchronize operations. This is where Industrial Ethernet excels.
Think of it as the rugged cousin of regular Ethernet, equipped to handle the chaos of an industrial setup while ensuring seamless connectivity. With its scalability, Industrial Ethernet is the cornerstone of modern automation systems.
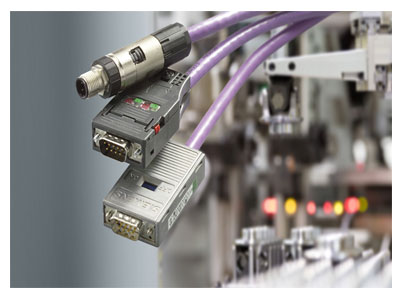
Key Features That Make Ethernet 'Industrial'
Industrial Ethernet isn’t just a buzzword; it’s packed with features that make it indispensable in industrial settings. First and foremost is ruggedness. The cables, connectors, and switches used in Industrial Ethernet are designed to endure harsh conditions. They’re resistant to dust, moisture, extreme temperatures, and even chemical exposure.
Another critical feature is real-time data transfer. Industrial applications often demand instantaneous communication between devices. For example, in a robotic assembly line, a delay of even milliseconds could disrupt the entire operation. Technologies like Ethernet/IP and PROFINET ensure real-time data exchange, making processes smooth and efficient.
Scalability is another highlight. Industrial Ethernet can adapt to networks of any size, from a small factory setup to an extensive system across multiple locations. Its compatibility with standard Ethernet means you can integrate new technologies without overhauling the entire network.
Additionally, Industrial Ethernet supports deterministic communication, meaning data packets follow a predictable path. This predictability is vital for applications like machine control, where timing is critical.
Lastly, it ensures high reliability and redundancy. Features like ring topologies and failover mechanisms minimize downtime, keeping operations running even during hardware failures.
These features collectively make Industrial Ethernet the backbone of modern factories, where efficiency, reliability, and speed are non-negotiable.
How Industrial Ethernet Differs From Standard Ethernet
How Industrial Ethernet Differs From Standard Ethernet
Applications of Industrial Ethernet in Harsh Environments
Industrial Ethernet thrives in environments where standard networking solutions would fail. It’s engineered to perform reliably under the most challenging conditions, making it the go-to solution for industries operating in harsh environments.
One major application is in manufacturing plants. Here, machines, sensors, and controllers need to communicate seamlessly to maintain productivity. Industrial Ethernet connects these devices, ensuring smooth data flow even amidst vibrations, heat, and electrical noise.
In the oil and gas industry, where equipment operates in extreme temperatures and hazardous conditions, Industrial Ethernet ensures uninterrupted data transmission. It enables real-time monitoring of pipelines and rigs, enhancing safety and operational efficiency.
Mining operations also benefit greatly. Underground mines rely on robust communication networks to control machinery and monitor environmental conditions. Industrial Ethernet’s rugged design ensures consistent performance, even in dusty, high-vibration settings.
The food and beverage sector is another example. Hygienic environments demand equipment that can withstand rigorous cleaning processes, including exposure to chemicals and water. Industrial Ethernet components are built to endure such conditions without compromising performance.
Finally, in transportation and logistics, Industrial Ethernet connects systems like automated conveyor belts and sorting machines. Its reliability ensures minimal downtime, which is crucial for high-speed operations.
In essence, Industrial Ethernet’s versatility and durability make it an indispensable tool in industries where reliable communication is non-negotiable.
Industrial Ethernet’s Role in the IIoT (Industrial Internet of Things)
The Industrial Internet of Things (IIoT) represents a shift towards smarter, interconnected industrial systems—and Industrial Ethernet is at the heart of this transformation.
IIoT relies on devices like sensors, actuators, and controllers to collect and share data across a network. Industrial Ethernet provides the infrastructure needed for this communication. Its high-speed, real-time capabilities ensure that data flows seamlessly between devices, enabling smarter decision-making.
For example, in a smart factory, Industrial Ethernet connects sensors on a production line to a centralized system. This setup allows operators to monitor performance in real-time and predict when machines need maintenance, preventing costly breakdowns.
Industrial Ethernet also supports the integration of advanced technologies like edge computing and artificial intelligence (AI). These technologies require fast and reliable data transfer to analyze and respond to changes in industrial processes.
Additionally, Industrial Ethernet enables remote monitoring and control. In sectors like energy and utilities, operators can use IIoT-enabled systems to manage equipment spread across vast geographical areas. This capability reduces the need for on-site personnel and improves efficiency.
Security is another critical aspect. As IIoT devices increase, so do potential vulnerabilities. Industrial Ethernet networks incorporate advanced security features to protect against cyber threats, ensuring data integrity.
In conclusion, Industrial Ethernet serves as the backbone of IIoT, enabling industries to transition towards smarter, more efficient operations. Its role in connecting devices, ensuring reliability, and supporting real-time data exchange makes it a cornerstone of modern automation.
Conclusion
As industries embrace automation and connectivity, understanding Industrial Ethernet becomes essential for engineers like you. Its ability to combine durability, reliability, and high-speed communication has made it a critical component of modern industrial systems.
Whether it’s powering IIoT solutions, ensuring real-time communication, or thriving in harsh environments, Industrial Ethernet is more than just technology—it’s a foundation for innovation. By mastering its concepts and applications, you’ll be well-equipped to tackle the challenges of industrial automation and contribute to the growth of your organization.