Key Takeaway
Cracking pressure is the minimum pressure at which a valve begins to open, allowing fluid or gas to pass through. It is a critical parameter for pressure relief valves (PRVs) and other types of valves, as it determines the point at which the valve starts to relieve pressure.
Accurate determination of cracking pressure is essential for ensuring the valve provides reliable protection and operates as intended. It helps prevent overpressure conditions and ensures the safe operation of equipment and systems.
Defining Cracking Pressure
Cracking pressure refers to the minimum pressure differential required to begin opening a pressure relief valve. This critical parameter determines when the valve starts to provide pressure relief, making it essential for proper system protection.
The determination of cracking pressure involves careful consideration of system requirements and safety margins. It must be set high enough to prevent nuisance opening while low enough to provide timely pressure relief when needed.
Regular testing and adjustment of cracking pressure is essential for maintaining valve performance. This includes periodic verification of valve response and adjustment of spring tension to maintain proper cracking pressure settings.
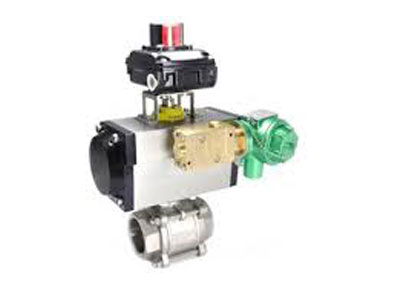
Importance in Valve Operation
The concept of cracking pressure in valve operation is critical for the correct functioning of Pressure Relief Valves (PRVs). Cracking pressure refers to the minimum pressure at which the valve starts to open, allowing fluid or gas to be released. This is an important aspect of valve performance because it defines the threshold at which the valve becomes active to protect the system from overpressure. Setting the cracking pressure too high can lead to excessive pressure buildup in the system, while setting it too low may cause the valve to open prematurely, leading to unnecessary loss of fluids or gases.
Accurately setting the cracking pressure ensures that the PRV only opens when absolutely necessary, protecting both the system and the environment. If the cracking pressure is set correctly, the valve will maintain system pressure within safe limits without triggering frequent or unwanted pressure releases. It also helps to minimize wear and tear on the valve, contributing to its longevity and effectiveness.
Regularly checking and calibrating the cracking pressure is essential to maintain optimal valve performance. Over time, factors such as corrosion, debris accumulation, and mechanical wear can alter the valve’s cracking pressure, leading to potential safety hazards. Proper maintenance and testing ensure that the valve continues to operate at the correct pressure threshold, preventing accidents and ensuring the system runs efficiently.
You May Like to Read
How to Measure Cracking Pressure
Cracking pressure refers to the minimum pressure at which a Pressure Relief Valve (PRV) begins to open, and it is a crucial factor in ensuring the valve performs as intended. Accurate measurement of cracking pressure is essential for maintaining system safety and avoiding underperformance of the valve. The process for measuring cracking pressure typically involves using a pressure gauge or a hydraulic testing device that can accurately monitor the pressure levels within the system as the valve is activated.
To measure cracking pressure, the valve is first installed in a controlled environment, where the system pressure is gradually increased. A pressure gauge is used to monitor the pressure at the valve’s inlet. As the pressure rises, the valve remains closed until the pressure reaches the set cracking point, at which it begins to open. The pressure at which the valve starts to open is recorded as the cracking pressure. This value is crucial because it indicates the pressure at which the PRV will begin to relieve excess pressure from the system.
The measurement of cracking pressure must be done with precision to ensure the valve opens at the desired pressure, preventing both overpressure and premature valve opening. The cracking pressure is usually set by the manufacturer, but it can be adjusted during installation or maintenance to meet the specific requirements of the system. Any variations from the expected cracking pressure can lead to performance issues, such as premature opening, or failure to open when needed, which can compromise the safety of the system. Regular testing is therefore essential to verify that the cracking pressure remains within the desired range.
Factors Influencing Cracking Pressure
Cracking pressure refers to the minimum pressure at which a Pressure Relief Valve (PRV) opens to release excess pressure. Several factors influence this pressure, including the type of valve, the spring tension, and the material used in the valve’s construction. A PRV with a higher cracking pressure is used in systems that require higher operating pressures, while a lower cracking pressure is ideal for systems that need more sensitive pressure regulation.
The size and design of the PRV also impact the cracking pressure, as larger valves generally have a higher cracking pressure. Additionally, the fluid’s characteristics, such as its viscosity and density, can affect how easily the valve opens under pressure. Therefore, understanding these factors is critical when selecting the appropriate PRV for a specific application.
Manufacturers typically provide cracking pressure specifications for their PRVs, but fine-tuning may be necessary to optimize valve performance for specific operational conditions. Properly calibrated PRVs ensure effective pressure management and prevent damage to equipment and systems.
Applications in Different Systems
PRVs play a crucial role in various systems, especially those involving cracking pressure. Cracking pressure refers to the minimum pressure at which a PRV begins to open to release excess pressure. Applications include pipeline systems, where PRVs regulate pressure buildup and ensure safe operation.
In hydraulic systems, PRVs are used to maintain a stable operating pressure by diverting excess fluid. This prevents component damage and ensures the system operates within its designated parameters. Such applications are vital in industrial and automotive settings.
PRVs are also essential in steam and gas systems, where they protect against dangerous pressure spikes. Their precise control over cracking pressure helps maintain safety and efficiency across diverse applications.
Conclusion
Cracking pressure is the minimum pressure at which a valve begins to open, allowing fluid or gas to pass through. It is a critical parameter for pressure relief valves (PRVs) and other types of valves.
Understanding cracking pressure is essential for ensuring the valve provides reliable protection and operates as intended. Accurate determination of cracking pressure helps prevent overpressure conditions and ensures the safe operation of equipment and systems.