Key Takeaway
A 3/2 directional control valve has three ports and two positions. It is commonly used in pneumatic systems to control single-acting cylinders.
In one position, the valve allows fluid to flow to the actuator. In the other, it exhausts the fluid. This makes it simple yet effective for basic control tasks.
Introduction to 3/2 Directional Control Valves
The 3/2 directional control valve (3/2 DCV) is one of the simplest and most commonly used types of DCVs in pneumatic and fluid systems. As the name suggests, a 3/2 valve has three ports and two positions, making it ideal for basic flow control tasks, especially in single-acting cylinders or other straightforward applications where two positions are required.
1. Port Configuration: The three ports of a 3/2 DCV consist of an inlet port, an outlet port, and an exhaust port. These ports allow the valve to either supply air to the actuator (for extension) or vent the air (for retraction), ensuring smooth and controlled operation of pneumatic components.
2. Flow Paths: The two positions of the valve provide two distinct flow paths. In one position, the inlet port is connected to the actuator’s inlet, while the exhaust port is connected to the actuator’s exhaust port, allowing the air to exit. In the second position, the flow direction is reversed, and the exhaust port vents the air from the actuator.
3. Applications: 3/2 valves are typically used in applications such as controlling the operation of a single-acting cylinder, where the movement only requires one direction of air flow, or in systems where a simple on/off control of air is needed. Their compact design and simplicity make them an excellent choice for less complex systems.
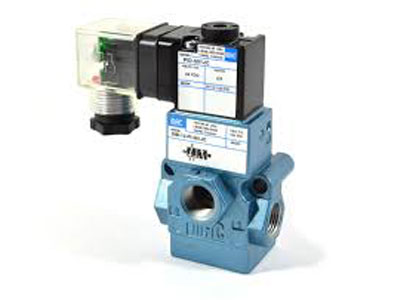
Working Principle and Functions
A 3/2 Directional Control Valve (DCV) is a crucial component in fluid control systems, typically used in pneumatic and hydraulic applications to manage the direction of airflow. The “3” in 3/2 refers to the three ports of the valve: inlet, outlet, and exhaust. The “2” signifies the two positions the valve can take, which control the flow of air or fluid in different directions. This design allows the valve to either allow the flow, block it, or direct it to an alternate port.
The working principle of a 3/2 DCV is based on a spool or poppet mechanism that shifts between two positions to control the flow path. When the valve is in one position, it connects the inlet port to the outlet port, allowing fluid or air to flow through the system. In the second position, the inlet port is blocked, and the flow is directed to the exhaust port, effectively shutting off the flow and venting any pressure.
The primary function of a 3/2 DCV is to control the flow direction in systems like actuators, pneumatic cylinders, and solenoid-actuated valves. It can be operated manually, electrically, or pneumatically, depending on the application. When used in automation systems, the valve’s ability to change flow direction is essential for controlling machines and equipment, such as reversing the direction of a pneumatic cylinder or controlling the action of a motor. By using a 3/2 DCV, operators can achieve precise control over fluid dynamics, enhancing efficiency and functionality in various industrial processes.
Comparison with Other DCV Types
When evaluating Directional Control Valves (DCVs), it is important to compare them with other types of valves commonly used in fluid systems to understand their unique characteristics and applications. One of the key comparisons is between pneumatic DCVs and hydraulic DCVs. While both are used for controlling the flow of air or fluid, hydraulic DCVs are designed to handle higher pressures and heavier flows compared to pneumatic ones. Pneumatic DCVs are typically more compact and lighter, making them suitable for applications where space and weight are a concern, such as in automation and robotics. In contrast, hydraulic DCVs are more commonly used in industries that require high-force applications, such as manufacturing and construction.
Another important comparison is between manual-operated DCVs and solenoid-operated DCVs. Manual valves require physical operation through a handle or lever, giving operators direct control over fluid flow. While this provides a more hands-on approach, it can be labor-intensive and may not be suitable for high-speed or automated processes. Solenoid-operated DCVs, on the other hand, use electrical signals to control the valve’s operation, enabling remote or automated control. These are ideal for systems where quick, precise, and automated operation is necessary. Solenoid-operated DCVs also offer faster switching times compared to manual valves, which is a critical factor in applications where speed is essential.
Furthermore, DCVs can be compared based on their actuation mechanisms. Spring-return DCVs are actuated by a spring mechanism that returns the valve to its default position when no external force is applied.
Applications in Pneumatic Systems
Solenoids find extensive applications in pneumatic systems, where they serve as essential components for controlling airflow. These systems utilize solenoid valves to regulate the distribution of compressed air, enabling precise control over pneumatic actuators and other devices. The ability to quickly open and close valves makes solenoids ideal for applications requiring rapid response times, such as in automated manufacturing and packaging processes.
The integration of solenoids in pneumatic systems offers several advantages, including enhanced efficiency and control. By allowing for the precise regulation of air pressure and flow, solenoids help optimize the performance of pneumatic systems, leading to improved energy efficiency and reduced operational costs. Additionally, the use of solenoids can enhance system safety by providing reliable and consistent control over pneumatic devices, reducing the risk of accidents or malfunctions.
Furthermore, solenoids enable the design of compact and versatile pneumatic systems. They are available in various configurations to suit different system requirements, allowing engineers to create tailored solutions for specific applications. This flexibility, combined with their reliability and ease of integration, makes solenoids a preferred choice in diverse industries, from automotive and aerospace to healthcare and food processing, where precise pneumatic control is critical.
Maintenance Tips for 3/2 DCVs
Maintenance of 3/2 Directional Control Valves (DCVs) is crucial for ensuring reliable system performance and longevity. These valves play a vital role in controlling fluid flow and directing air or hydraulic fluid in pneumatic and hydraulic systems. Regular maintenance helps prevent unexpected failures and extends the operational life of the system, reducing downtime and associated costs.
Key points in maintaining 3/2 DCVs include routine inspections, cleaning, and lubrication. Inspections should focus on identifying signs of wear and damage, such as leaks and corrosion, which can compromise the valve’s functionality. Cleaning the valve components removes debris and contaminants that may obstruct fluid flow or cause damage. Lubrication ensures smooth operation and reduces friction between moving parts, minimizing wear and tear.
Practical insights for effective maintenance involve developing a schedule based on the valve’s usage and environmental conditions. In high-demand or harsh environments, more frequent maintenance may be necessary to address the increased risk of wear and damage. Additionally, utilizing diagnostic tools and monitoring systems can provide valuable data on valve performance, enabling proactive maintenance and reducing the likelihood of failures.
In conclusion, regular maintenance of 3/2 DCVs is essential for optimizing system performance and preventing costly disruptions. By implementing a comprehensive maintenance strategy, companies can enhance the reliability and efficiency of their fluid systems, ultimately contributing to improved operational outcomes and long-term success.
Conclusion
A 3/2 directional control valve is a specific type of valve with three ports and two operational states.
It is commonly used to control single-acting cylinders in pneumatic systems, providing a simple yet effective way to manage the extension and retraction of the actuator. By directing compressed air to either the cylinder or the exhaust, the 3/2 valve facilitates efficient control of motion, making it a staple in various industrial applications.
The functionality of the 3/2 directional control valve highlights its importance in achieving compact and cost-effective system designs. By offering straightforward control over actuator movement, these valves contribute to streamlined operations and reduced system complexity. Understanding their operation and application is crucial for engineers seeking to implement reliable and efficient pneumatic solutions, enhancing overall system performance and productivity.