Key Takeaway
Real-time Ethernet protocols are specialized communication protocols designed for industrial applications where timing and reliability are critical. These protocols ensure precise data exchange between devices like PLCs, sensors, and actuators in automation systems. Common real-time Ethernet protocols include EtherCAT, PROFINET, Ethernet/IP, and SERCOS III. They offer low latency, synchronized communication, and high data transfer speeds, making them ideal for factory automation and robotics.
Each protocol has unique features. For instance, EtherCAT is known for its high-speed communication, while PROFINET focuses on flexibility and integration. Ethernet/IP is widely used in North America for seamless data sharing, and SERCOS III specializes in motion control. These protocols ensure efficient and reliable communication, reducing downtime and improving productivity in industrial environments. Choosing the right protocol depends on the application’s specific needs and system compatibility.
Introduction to PROFINET for Real-Time Communication
PROFINET (Process Field Network) is one of the most widely adopted Ethernet-based communication protocols in industrial applications. Developed by Siemens, it is designed to facilitate real-time data exchange across automation systems. Its versatility allows it to integrate seamlessly with various devices and systems, making it a cornerstone for modern manufacturing.
One standout feature of PROFINET is its capability to handle both cyclic and acyclic data. Cyclic data is transmitted at predictable intervals, perfect for time-critical tasks like motion control. On the other hand, acyclic data addresses non-time-sensitive processes, such as diagnostics or parameter adjustments. This dual functionality ensures efficiency and reliability in any industrial setup.
Another benefit is its support for redundancy. PROFINET networks can include multiple paths for data transmission, ensuring continuity even if one path fails. Its compatibility with standard Ethernet hardware also simplifies implementation, reducing costs and integration challenges.
In industrial applications, PROFINET excels in high-speed communication, plant automation, and remote system monitoring. Its ability to combine flexibility, speed, and reliability makes it an indispensable tool for industrial engineers.
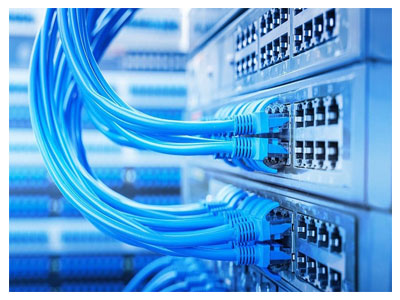
EtherCAT for High-Speed Data Transfer
EtherCAT (Ethernet for Control Automation Technology) is a protocol designed for ultra-fast data transfer in industrial systems. Unlike traditional protocols, EtherCAT processes data “on the fly.” As packets travel through a network, each device extracts or inserts its data without waiting for the entire packet to finish transmitting. This unique feature allows EtherCAT to achieve cycle times in the microsecond range.
This speed makes EtherCAT ideal for applications requiring precise synchronization, such as robotics and CNC machinery. For instance, in robotics, EtherCAT ensures that commands to each joint are delivered in perfect harmony, enabling smooth and accurate movements.
Another advantage is its scalability. EtherCAT can support up to 65,535 devices on a single network, making it suitable for both small-scale operations and large industrial plants. Additionally, it uses standard Ethernet cables and connectors, keeping installation simple and cost-effective.
EtherCAT also includes built-in diagnostic tools to monitor network health. It can detect faults such as cable breaks or misconfigured devices, ensuring minimal downtime and quicker troubleshooting.
With its unparalleled speed and flexibility, EtherCAT stands out as one of the best choices for real-time industrial automation, enabling smarter and faster systems.
How Time-Sensitive Networking (TSN) Enhances Real-Time Ethernet
How Time-Sensitive Networking (TSN) Enhances Real-Time Ethernet
Applications of Real-Time Ethernet in Manufacturing
Real-time Ethernet protocols are transforming manufacturing by enabling faster, more reliable communication between systems. One of the most common applications is in robotic systems. Real-time protocols like EtherCAT ensure precise coordination, allowing robots to perform tasks with incredible accuracy and speed.
Another critical area is process automation. Real-time Ethernet facilitates seamless data exchange between PLCs, sensors, and actuators, ensuring that production lines operate without interruptions. For example, in a bottling plant, Ethernet protocols synchronize conveyor belts, filling stations, and quality checks to avoid delays or defects.
Predictive maintenance is also a significant application. Real-time data collection allows manufacturers to monitor equipment performance and detect issues before they escalate. This reduces downtime and maintenance costs.
Additionally, these protocols support remote monitoring and control. Engineers can oversee operations, adjust parameters, and troubleshoot issues from anywhere, boosting efficiency and flexibility. With such diverse applications, real-time Ethernet is essential for modern manufacturing.
Comparison of Real-Time Ethernet Protocols
Choosing the right real-time Ethernet protocol depends on the specific needs of your application. Each protocol has its strengths and limitations, making some more suitable than others for particular tasks.
PROFINET is known for its flexibility and compatibility, making it ideal for general automation and process control. It’s easy to integrate with existing systems and supports redundancy for added reliability. However, its speed may not match other protocols in high-demand applications.
EtherCAT excels in speed and precision, making it perfect for robotics and motion control. Its unique “on-the-fly” data processing gives it an edge in time-critical tasks. However, its setup can be more complex compared to PROFINET.
TSN, on the other hand, enhances Ethernet’s real-time capabilities by prioritizing and synchronizing traffic. It is especially beneficial for complex networks with diverse devices. TSN’s biggest advantage is its future-proof design, ensuring scalability for IIoT applications.
Understanding these differences allows engineers to choose the right protocol, ensuring optimal performance and efficiency in their industrial networks.
Conclusion
Real-time Ethernet protocols are at the heart of modern industrial automation, enabling fast, reliable, and synchronized communication between devices. PROFINET, EtherCAT, and TSN each offer unique features tailored to different applications, ensuring that industries can achieve their automation goals.
By understanding these protocols and their applications, engineers can make informed decisions, optimizing their networks for performance and reliability. As industries embrace smarter and more connected systems, real-time Ethernet protocols will continue to drive innovation and efficiency in industrial operations.