Key Takeaway
PLC panels and MCC panels serve different purposes in industrial automation. A PLC panel focuses on process control and automation. It uses a Programmable Logic Controller (PLC) to process inputs from sensors and send commands to devices like motors and valves, ensuring efficient and precise operations.
On the other hand, an MCC (Motor Control Center) panel is designed to control and protect electric motors. It houses components like motor starters, circuit breakers, and relays. While PLC panels handle logic-based controls, MCC panels focus on powering and safeguarding motors. In many systems, both panels work together, with PLC panels managing automation and MCC panels controlling the motors.
Defining the Functionality of PLC Panels
PLC panels are used in industrial automation for controlling, monitoring, and managing complex processes. These control panels are designed to receive input signals from various sensors and devices, process the data through a series of pre-programmed instructions, and then send output signals to control machines, systems, or equipment. The primary function of a PLC panel is to automate processes, which can include anything from controlling conveyor belts in manufacturing lines to adjusting temperature or pressure in chemical plants.
A PLC panel houses a programmable logic controller, which acts as the brain of the system. It is programmed with specific logic that tells the system how to respond to input signals, such as turning on or off certain machines, controlling the speed of motors, or adjusting the operation of various systems. PLCs offer great flexibility in terms of programming, allowing engineers to modify control logic without having to physically rewire the system.
One of the most notable features of PLC panels is their versatility. They are capable of handling a wide variety of tasks across industries, from controlling simple switches to managing advanced processes like robotic arms and automatic assembly lines. These panels are also capable of integrating with other automation systems, such as SCADA (Supervisory Control and Data Acquisition) or HMI (Human-Machine Interface) systems, to provide real-time monitoring and control of operations.
In short, PLC panels are at the core of industrial automation, providing intelligent control, flexibility, and efficiency in a wide array of applications.
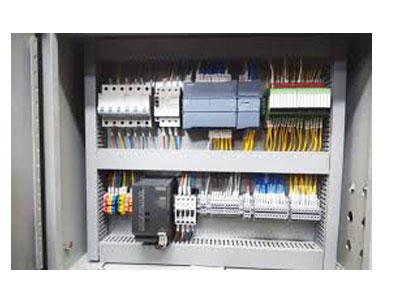
Understanding the Role of MCC Panels in Industrial Settings
While PLC panels are used for automation and process control, MCC panels are designed to manage and control motors and other electrical equipment. The primary function of an MCC panel is to provide a centralized location for controlling multiple motors, including their start/stop functions, speed regulation, and fault detection. MCC panels typically consist of a series of motor control units (MCUs), each of which controls a single motor or group of motors.
MCC panels are commonly found in industries where motors are used extensively, such as in pumping stations, water treatment plants, mining operations, and manufacturing. They provide a convenient and efficient way to manage motor operations in large facilities with multiple motors and electrical equipment.
MCC panels are often equipped with circuit breakers, contactors, and overload relays to protect motors from electrical faults. Additionally, variable frequency drives (VFDs) may be integrated into the panel to control the speed and torque of motors, offering more precise control over the operation of electrical machinery. These panels are designed to ensure that motors and electrical systems operate safely and efficiently, minimizing the risk of damage or failure.
One of the most important aspects of MCC panels is that they help improve the maintenance of motor-driven systems. Since MCCs provide centralized control, troubleshooting is simplified, and any faults in the motors can be quickly identified and rectified. This centralized approach also reduces the complexity of wiring and ensures that operators can easily access and control various motors from one location.
In summary, MCC panels play a critical role in managing and protecting motors and electrical equipment in various industrial applications.
Key Differences in the Control Mechanisms of PLC and MCC Panels
While both PLC panels and MCC panels serve as central control points in industrial automation, the key differences lie in their control mechanisms and the way they manage operations.
1. Control Logic:
A PLC panel uses a programmable logic controller to execute a set of instructions or control logic that can be easily modified through programming. The PLC can handle complex processes involving inputs and outputs, including sensors, switches, and machinery. It is highly flexible and capable of performing a wide range of control tasks, such as process sequencing, data logging, and real-time adjustments.
In contrast, an MCC panel uses a hard-wired control system to operate and control motors. It relies on mechanical switches, contactors, and overload relays to manage the flow of electricity to the motors. Unlike PLC panels, MCCs are not programmed but rather operate based on predefined electrical circuits and components.
2. Complexity of Operations:
PLC panels can handle complex automation tasks, including data analysis, remote monitoring, and process control, making them suitable for applications like robotics, assembly lines, and smart factories.
MCC panels, on the other hand, are designed for motor control and are generally more straightforward in their function. They are primarily used for controlling motors, which often only require on/off functions or speed control.
3. Flexibility:
PLC panels offer a high degree of flexibility since they can be reprogrammed easily to meet changing control requirements. If the process changes or new devices need to be integrated, the PLC panel can be reprogrammed without the need for extensive hardware modifications.
MCC panels, however, are less flexible. They are more focused on motor protection and control, and any changes to the system may require reconfiguration or rewiring of the control panels.
These differences make PLC panels better suited for applications where complex control and automation are required, while MCC panels excel in applications that primarily involve the management of motor operations.
How PLC Panels Enhance Automation Compared to MCC Panels
When it comes to industrial automation, PLC panels offer several advantages over MCC panels in terms of control and efficiency. A PLC panel can handle a much broader range of functions, including not just motor control, but also the automation of complex processes that involve various types of sensors, equipment, and systems.
For instance, in a production facility, a PLC panel can control the entire process, from starting and stopping motors to adjusting temperature, pressure, or speed in real-time. This level of control enhances the automation of the entire production line, reducing the need for manual intervention and ensuring that processes are optimized for maximum efficiency.
Additionally, PLC panels integrate seamlessly with other automation systems like SCADA, HMI, and MES to provide a comprehensive, real-time view of all processes in the plant. This integration allows for remote monitoring and data analytics, helping operators make informed decisions and optimize performance. MCC panels, while crucial for motor control, do not offer the same level of integration or control over non-motor processes.
In comparison to MCC panels, PLC panels are better equipped for flexible automation in environments where process complexity and adaptability are key. They offer the ability to automate entire systems that go beyond just motor control.
The Cost, Maintenance, and Flexibility of PLC vs MCC Panels
When choosing between a PLC panel and an MCC panel, several factors need to be considered, including cost, maintenance, and flexibility.
1. Cost:
PLC panels typically come with a higher initial cost due to their more complex design and programming capabilities. However, this cost is justified by the flexibility and advanced control features they offer, making them suitable for a wide range of applications.
MCC panels, being simpler in design, are generally more cost-effective, especially for motor-driven systems. Their straightforward design makes them an attractive option for companies looking for a more budget-friendly solution focused primarily on motor control.
2. Maintenance:
PLC panels require regular maintenance of both hardware and software components. Since they rely on programming and software, any system bugs or software issues may require skilled personnel to troubleshoot and resolve problems. However, their diagnostic capabilities allow for quick identification of issues, helping to reduce downtime.
MCC panels have fewer components and are easier to maintain. Most issues with MCC panels are related to electrical components like contactors or circuit breakers, which can be easily replaced or repaired.
3. Flexibility:
PLC panels offer unmatched flexibility and adaptability. They can be reprogrammed and expanded to accommodate new devices or process changes without the need for significant rewiring or hardware changes.
MCC panels, while more rigid in function, are highly effective at controlling motor-driven systems. However, they are less adaptable to changes in control logic or system requirements.
Conclusion
In conclusion, the choice between PLC panels and MCC panels ultimately depends on the specific needs of the application. PLC panels offer superior flexibility, advanced control, and integration with other systems, making them ideal for complex automation tasks. MCC panels, on the other hand, are more cost-effective and simpler to maintain, making them perfect for motor control applications.
As a new engineer, understanding the roles and differences between PLC panels and MCC panels will help you make informed decisions about which control system best suits your automation project. Whether you’re focusing on motor control or looking to automate entire processes, both panels have their place in the industrial world.