Key Takeaway
The costs associated with implementing a SCADA system depend on several factors, including system size, complexity, and features. The main expenses include hardware, such as sensors, PLCs, RTUs, and servers, which form the backbone of the SCADA system. Software licenses for SCADA platforms, along with customization and integration, also contribute significantly to the cost.
Additional costs include installation, networking, and cybersecurity measures like firewalls and encryption to protect the system. Ongoing expenses, such as maintenance, updates, and operator training, should also be considered. If you require advanced features like IoT integration or cloud storage, these can add to the total cost. While initial investment can be high, a well-implemented SCADA system improves efficiency, reduces downtime, and provides long-term savings. Proper planning ensures a cost-effective implementation tailored to your industry needs.
Initial Setup and Hardware Costs for SCADA Systems
The first significant expense in implementing a SCADA system is the cost of hardware. SCADA hardware includes components like programmable logic controllers (PLCs), remote terminal units (RTUs), sensors, servers, and communication equipment. Each of these components is essential for capturing data, transmitting it, and allowing operators to monitor and control processes.
For example, a manufacturing plant may need dozens of sensors and PLCs to cover its production lines. These devices must be robust enough to operate in industrial environments, often requiring specialized designs that can handle high temperatures, dust, or moisture.
Additionally, setting up a SCADA system requires investment in control room infrastructure. This includes workstations, large displays, and networking equipment to create a centralized hub for operators.
Depending on the scale of your operations, these initial hardware costs can range from a few thousand to several hundred thousand dollars. Planning carefully and sourcing hardware that balances performance with cost efficiency can help control this expense.
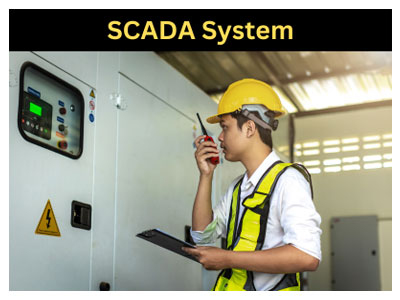
Software Licensing and Subscription Fees
The software component of a SCADA system is just as important as the hardware, and it comes with its own set of costs. SCADA software is often sold through licensing agreements or subscription-based models.
Licensing fees depend on the number of devices or users the system will support. For instance, a small water treatment plant may only need a single-user license, while a larger facility managing multiple sites might require a multi-user or enterprise license. These costs can vary widely, from a few hundred dollars per license to tens of thousands for more extensive setups.
Subscription models offer more flexibility, often including regular updates and support. However, they also mean ongoing payments that need to be factored into the budget.
Additionally, some SCADA solutions require separate licenses for advanced features like analytics, predictive maintenance, or IoT integration. Assess your needs carefully to avoid paying for unnecessary extras while ensuring you have all the tools required for optimal performance.
Costs Involved in Integration with Existing Systems
Integrating SCADA software with existing hardware and systems is another critical cost factor. Few facilities start from scratch, so your SCADA solution must work seamlessly with your current equipment.
Integration costs include the labor and time required to configure communication protocols, customize the software to fit your processes, and ensure compatibility with existing PLCs, RTUs, or sensors. For instance, if your facility uses older devices that operate on legacy protocols like Modbus or DNP3, additional effort may be needed to ensure they work with modern SCADA systems.
Customizations can also add to the cost. Many industries require tailored solutions, such as specific alarm settings, customized reports, or unique control interfaces. These adjustments require expertise, which might involve hiring consultants or specialized engineers.
Failing to account for integration expenses can lead to unexpected delays and budget overruns. A thorough assessment of your existing systems and clear communication with your SCADA vendor can help minimize these costs.
Ongoing Maintenance and Support Expenses
Implementing a SCADA system is not a one-time expense; maintaining it over time is equally important. Regular maintenance ensures that the system operates efficiently and adapts to changing operational needs.
Hardware maintenance includes replacing or repairing components like sensors, controllers, and communication devices. For example, sensors exposed to harsh environments may require more frequent replacements.
Software maintenance involves updating the SCADA system to fix bugs, improve security, and add new features. Many vendors offer annual maintenance contracts that cover these updates, but these contracts come at an additional cost.
Support services are another recurring expense. Whether it’s troubleshooting technical issues or providing system upgrades, having access to responsive vendor support can save time and prevent prolonged downtime. Factor these ongoing expenses into your budget to ensure the long-term success of your SCADA system.
Training and Workforce Development Costs
Even the best SCADA system won’t deliver value if your workforce doesn’t know how to use it effectively. Training is an essential part of implementation, and it comes with its own costs.
Operators and technicians need to be trained on the system’s interface, alarm management, and troubleshooting procedures. Depending on the complexity of the system, this training might take a few days to several weeks.
Training sessions can be conducted in-house by the SCADA vendor or at external training centers. Costs typically include instructor fees, travel expenses, and materials.
In addition to initial training, consider the cost of ongoing workforce development. As your system evolves with new features or upgrades, your team will need refresher courses to stay proficient. Investing in training ensures that your staff can maximize the system’s capabilities and respond effectively to operational challenges.
Conclusion
Implementing a SCADA system involves a wide range of costs, from initial hardware and software investments to ongoing maintenance and workforce training. Careful planning and thorough assessment of your requirements can help optimize your investment and avoid unexpected expenses.
By considering all aspects, including integration, scalability, and support, industries can design a SCADA system that not only meets current needs but also delivers long-term efficiency and reliability. For engineers and managers, understanding these costs is the first step toward making informed decisions and ensuring a successful implementation.