Key Takeaway
The output of a Variable Frequency Drive (VFD) is AC. Here’s how it works: First, the VFD converts the incoming AC power to DC using a rectifier. This DC power is then stored in a DC bus. Next, an inverter changes the DC power back to AC, but with variable voltage and frequency. This allows the VFD to control the speed and torque of the motor. So, while the VFD handles both AC and DC internally, its final output to the motor is AC.
Understanding VFD Output
The primary function of a Variable Frequency Drive (VFD) is to control the speed and torque of an AC motor. A VFD takes in AC power, converts it to DC, and then back to AC at a variable frequency and voltage. This conversion process allows precise control over motor operations, which is crucial in various industrial applications. For example, in conveyor systems, VFDs ensure motors run at the correct speed, optimizing throughput and preventing jams. Understanding VFD output helps in troubleshooting and optimizing processes, enhancing productivity, and reducing energy consumption. Regular maintenance and monitoring ensure efficient operation and system reliability.
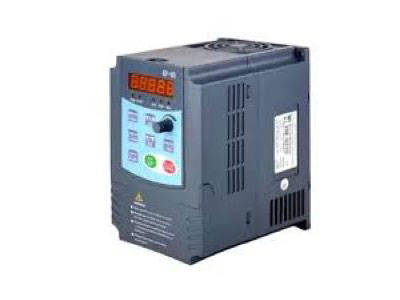
Conversion Process Inside VFDs
Understanding the conversion process inside a Variable Frequency Drive (VFD) is crucial for optimizing motor control in industrial applications. The journey begins with the rectifier stage. Here, incoming AC power, typically from the mains supply, is converted to DC. This DC power then passes through a DC bus, which acts as a stabilizing agent, smoothing out the voltage fluctuations. This stabilization is vital for consistent performance.
Next, the inverter stage comes into play. The DC power from the DC bus is converted back into AC power. However, this AC output is unique—it’s adjustable. Both the frequency and voltage of the AC output can be finely tuned. This ability to adjust the AC output is what allows a VFD to control motor speed and torque precisely, making it a versatile tool in various industrial applications.
Imagine needing different motor speeds for different tasks. With a VFD, you can achieve this effortlessly by tweaking the output frequency and voltage. This entire conversion process inside a VFD ensures that motors operate efficiently, conserving energy and reducing wear and tear. By mastering this process, you can significantly enhance the performance and longevity of your industrial machinery.
You May Like to Read
Applications Requiring AC Output
Most industrial applications of VFDs require AC output, as they are primarily used to control AC motors. These applications include conveyors, fans, pumps, and compressors. The ability to vary the motor speed enhances efficiency and performance, reducing energy consumption and wear on mechanical components.
For instance, in HVAC systems, VFDs regulate fan speed, ensuring optimal airflow and energy savings. Similarly, in pumping systems, VFDs adjust pump speed to match the required flow rate, leading to significant energy conservation.
Imagine a conveyor system in a manufacturing plant. The VFD allows precise control of the conveyor’s speed, adapting to the production line’s needs. This flexibility boosts productivity while minimizing energy use. Fans in industrial settings also benefit, as VFDs adjust their speed to maintain desired environmental conditions, cutting down on unnecessary power consumption.
VFDs in compressors help maintain consistent pressure levels, optimizing performance and extending the lifespan of equipment. By modulating the speed based on demand, these systems operate more efficiently and reliably.
Applications Requiring DC Output
While Variable Frequency Drives (VFDs) are predominantly used for controlling AC motors, there are specific industrial applications where DC output is necessary. These scenarios usually involve specialized processes or equipment that operate on DC motors. For instance, electroplating requires precise control over the plating process, making DC motors preferable.
In such applications, although VFDs primarily output AC, additional converters are employed to achieve the required DC output. This allows the control and flexibility of VFDs to be extended to DC motor applications, ensuring optimal performance and precision. However, these instances are relatively rare compared to the common use of AC motors in industrial applications.
Understanding these specialized uses is crucial for engineers, as it broadens the scope of VFD applications and highlights the versatility of VFD technology. Always consider the specific requirements of the application to determine whether AC or DC motor control is more suitable. By doing so, you ensure that the processes are efficient, precise, and meet the industry standards. This knowledge is essential for making informed decisions in various industrial settings.
Practical Examples and Case Studies
Consider a manufacturing plant where conveyor systems are essential. With Variable Frequency Drives (VFDs), the speed of these conveyors can be precisely controlled to align with production demands. This precise control improves efficiency and reduces downtime, ensuring seamless operations. For instance, during peak production periods, the conveyors can run faster to match output needs, while during maintenance or slower production times, the speed can be reduced to conserve energy.
Another excellent example is in water treatment facilities. Here, VFDs regulate pump speeds to maintain consistent water flow and pressure. This regulation is crucial for the optimal operation of the treatment process. By adjusting the pump speeds based on the water demand, VFDs ensure that the treatment process runs smoothly, avoiding the risks of overpressure or insufficient flow, which can lead to operational inefficiencies or damage to equipment.
These practical applications demonstrate the versatility and effectiveness of VFDs in various industrial scenarios. They highlight the importance of VFDs in modern automation, showing how they can enhance efficiency, save energy, and reduce wear and tear on machinery. VFDs are indispensable tools in achieving operational excellence and maintaining a competitive edge in industrial applications.
Conclusion
In summary, VFDs primarily provide an AC output, essential for controlling AC motors across numerous industrial applications. The conversion process inside a VFD, transforming AC to DC and back to variable AC, is key to its functionality. While some specialized applications may require DC output, the predominant use of VFDs is in AC motor control. Understanding this distinction is crucial for engineers and technicians working in the field of industrial automation. By grasping the nature of VFD output, you can better appreciate their role and optimize their use in various systems.