Key Takeaway
SCADA can be both wired and wireless. It depends on the setup and the requirements of the system. Wired SCADA systems use cables like Ethernet or fiber optics to connect sensors, devices, and control centers. This is common in environments where reliability and speed are critical, such as factories or power plants.
Wireless SCADA systems use technologies like Wi-Fi, radio, or cellular networks to transmit data. They are often used in remote locations like oil fields or water treatment plants where wiring isn’t practical. Both options have their advantages—wired systems are stable and secure, while wireless systems offer flexibility and easy installation. The choice between wired or wireless SCADA depends on factors like distance, cost, and the nature of the industrial process.
Overview of Wired and Wireless Communication in SCADA
In a SCADA system, communication is everything. It allows for the exchange of data between the control center and field devices. This communication can happen through wired or wireless networks, each offering different benefits suited for specific applications.
Wired communication typically refers to the use of physical cables (like Ethernet cables, fiber optics, or copper wire) to transmit signals between SCADA components. On the other hand, wireless communication uses radio waves, microwaves, or other wireless technologies such as Wi-Fi, LTE, or satellite links to send and receive data.
Wired connections have long been the standard in SCADA systems, especially in environments where stability and reliability are key. They offer high data transfer speeds and secure connections, making them ideal for real-time monitoring in critical applications. However, with the rise of industrial IoT (Internet of Things), wireless communication is becoming more prominent due to its flexibility, scalability, and ability to reach remote locations that are difficult to wire.
Ultimately, the choice of communication method depends on your specific requirements, including the size and complexity of the system, data volume, and operational environment. Let’s dive deeper into the pros and cons of each.
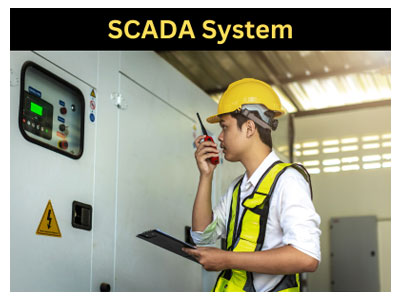
Advantages of Wired Connections in SCADA Systems
Wired connections in SCADA systems offer several significant advantages, making them the preferred choice in environments that demand high security, low latency, and high data integrity.
One of the primary benefits of wired communication is its reliability. Unlike wireless systems, wired systems are less prone to interference or signal degradation. This is crucial in industrial environments where consistent communication is vital for safety and efficiency. For instance, when managing a power plant or a water treatment facility, where real-time data and control are essential, a wired connection ensures that no data is lost or delayed.
Wired networks also offer higher bandwidth. Since the transmission of data is not limited by bandwidth constraints common in wireless systems, wired communication can handle large volumes of data without significant delays. This is especially important in SCADA systems that need to handle complex control systems and real-time processing of large datasets.
Moreover, security is a strong point for wired systems. They are less vulnerable to hacking and unauthorized access than wireless systems because physical access is required to tap into a wired network. This makes wired communication the choice for highly sensitive or classified operations like military or government installations.
In addition, installation and maintenance of wired systems are straightforward. While initial setup costs can be higher due to the need for cables and infrastructure, once set up, these systems are easier to maintain and troubleshoot, with clear indicators of failure when cables or connections are disrupted.
In essence, wired systems remain a robust and reliable choice for SCADA applications that demand high performance, security, and data throughput.
You May Like to Read
Benefits of Wireless Technology in SCADA Networks
While wired systems have their advantages, wireless communication is gaining momentum in SCADA applications due to its flexibility, cost-effectiveness, and ability to operate in hard-to-reach areas. Let’s look at some of the key benefits of wireless technology in SCADA networks.
One of the major benefits of wireless SCADA systems is their ability to expand network coverage to areas where it is difficult or impossible to lay physical cables. For example, in remote oil rigs, wind farms, or pipelines, wireless systems eliminate the need for long, expensive cable runs. Using technologies like Wi-Fi, LTE, radio frequency (RF), and satellite communication, wireless SCADA systems can efficiently transmit data from remote locations back to a central control center.
Wireless networks also offer easier scalability. As industrial environments grow, adding new sensors, devices, or equipment to a wireless SCADA system is relatively simple and cost-effective. With wired systems, adding new connections often means extensive re-wiring or digging up ground to lay cables, which can be time-consuming and expensive.
Another advantage of wireless technology is that it often results in lower installation costs. With fewer physical components to install, wireless systems can be up and running faster, making them a more attractive option for industries that require a quick turnaround time.
Additionally, wireless SCADA systems can improve mobility and flexibility. Operators and engineers can access and control the SCADA system remotely, using mobile devices or laptops, allowing them to monitor and make adjustments from anywhere within the network coverage area. This is particularly useful in industries where workforce mobility is a key factor.
Lastly, the maintenance and troubleshooting of wireless systems are often simpler. Remote diagnostics and over-the-air updates can be done without needing physical access to the equipment, which saves time and effort.
Overall, wireless SCADA technology provides flexibility, scalability, and cost-effectiveness, making it a suitable option for industries where real-time data collection from distant locations is needed.
Comparing Reliability and Scalability Between Wired and Wireless SCADA
When it comes to SCADA systems, two critical factors that determine the choice of communication method are reliability and scalability. Let’s break down how wired and wireless systems compare in these areas.
Reliability is one of the most important considerations for any SCADA system. As mentioned earlier, wired systems tend to have higher reliability because they are less susceptible to external factors like weather conditions, interference, or signal degradation. For industries that require high levels of precision and constant uptime, such as power generation or water treatment, a wired network often proves to be more dependable.
On the other hand, wireless SCADA systems are more vulnerable to disruptions. Wireless signals can be interfered with by environmental factors such as storms, buildings, or other machinery. Radio frequency interference or obstacles like large equipment can cause network congestion or signal drops, which could lead to delays or loss of data. While wireless technology has improved significantly, it’s still not as failproof as wired systems in terms of consistent, uninterrupted communication.
In terms of scalability, wireless systems have the upper hand. They can easily be expanded without significant infrastructure changes, whereas wired systems require running new cables or digging up areas to extend the network. As industries expand and more devices need to be connected, wireless SCADA systems can scale up with fewer constraints and lower costs.
However, hybrid systems that combine both wired and wireless technologies can offer the best of both worlds. For instance, a wired backbone can provide reliable communication for critical data, while wireless devices can connect remote locations or provide flexible solutions for areas where wiring is impractical.
Choosing the Right Communication Method for SCADA Applications
The decision to choose between wired and wireless communication for your SCADA system depends on a range of factors. Here are some key considerations to help guide your decision.
1. Data Volume and Speed: If your SCADA system needs to handle large amounts of data with high-speed requirements, wired communication may be the better choice. Wired systems can handle higher bandwidth and data transfer rates, ensuring smooth operation for large-scale industrial processes.
2. Remote Locations: For SCADA systems deployed in remote locations where wiring isn’t feasible, wireless technology is the obvious choice. Wireless systems can provide connectivity to hard-to-reach areas like offshore platforms, forests, or large outdoor facilities.
3. Security Concerns: If data security is a priority, wired systems generally offer stronger protection because they are less susceptible to external hacking attempts than wireless systems. While wireless systems can be secured with encryption and other security measures, they can still be more vulnerable.
4. Installation and Maintenance Costs: Consider the installation cost and ongoing maintenance requirements. Wired systems can have higher upfront costs due to the need for cables and infrastructure, but they might be cheaper to maintain over the long term. Wireless systems often have lower installation costs but may incur additional costs in ensuring good coverage and handling interference.
5. Network Expansion: If you anticipate the need for network expansion in the future, wireless systems are often more scalable and flexible, enabling easier addition of new devices without the need for extensive re-wiring.
Conclusion
In summary, SCADA systems can use both wired and wireless communication, each offering unique advantages depending on the operational environment and requirements. Wired systems are reliable, secure, and capable of handling high data volumes, making them ideal for critical, high-performance applications. Wireless systems, on the other hand, offer flexibility, cost-effectiveness, and scalability, making them perfect for remote or expansive installations. The right choice depends on factors such as data volume, system location, security, and cost considerations. Many modern systems opt for hybrid solutions that combine both methods to balance reliability with scalability, ensuring optimal performance across different environments.