Key Takeaway
PROFIBUS primarily uses RS-485 as its physical layer for communication. RS-485 allows multiple devices to communicate over a single network, supporting long distances and high-speed data transfer. This makes it ideal for industrial environments where PROFIBUS is widely used.
RS-232, while also a serial communication standard, is not typically used with PROFIBUS. RS-232 supports point-to-point connections and shorter distances, which limits its use in industrial networks. RS-485’s ability to connect multiple devices over longer distances is why it is preferred for PROFIBUS applications.
Overview of PROFIBUS Protocol and Its Communication Methods
PROFIBUS, or Process Field Bus, is an industrial communication protocol designed to enable seamless communication between automation systems and field devices. It is widely used in industries such as manufacturing, energy, and process automation to ensure reliable and fast data transfer.
The protocol operates on two main versions: PROFIBUS DP (Decentralized Periphery) for high-speed communication with sensors and actuators, and PROFIBUS PA (Process Automation) for use in hazardous environments. These versions rely on robust communication standards to meet industrial requirements.
PROFIBUS primarily uses RS-485 as its physical layer standard for communication. RS-485 offers high-speed, reliable data transmission over long distances, making it ideal for industrial environments. It allows multiple devices to communicate on a single network, enabling efficient fieldbus communication.
In some specialized applications, RS-232 may also be used. However, its role is limited due to its shorter communication distance and lack of multi-device capability. RS-232 is generally reserved for point-to-point connections or configuration tasks.
Understanding these communication methods will help you navigate PROFIBUS networks effectively and choose the right implementation for your application.
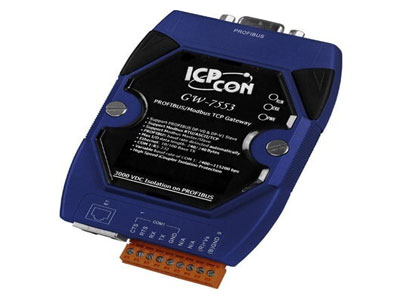
How PROFIBUS Utilizes RS-485 for Fieldbus Communication
RS-485 is the backbone of PROFIBUS communication in most industrial applications. It provides the physical layer for PROFIBUS DP, ensuring fast and reliable data transfer across devices.
One of the key reasons PROFIBUS relies on RS-485 is its ability to support multi-drop connections. This means multiple devices can be connected to the same bus, reducing the need for extensive wiring. A typical RS-485-based PROFIBUS network can support up to 32 devices without requiring repeaters, making it highly efficient for large-scale automation setups.
Another advantage of RS-485 is its long communication range. It can transmit data over distances of up to 1,200 meters (at lower baud rates), making it ideal for applications like factory automation and process control, where devices are often spread across vast areas.
RS-485 also ensures noise resistance. Industrial environments are notorious for electromagnetic interference (EMI) caused by heavy machinery and electrical systems. RS-485 uses differential signaling to minimize the impact of noise, ensuring stable and accurate data transfer.
For example, in a manufacturing plant, RS-485 enables PROFIBUS DP to connect controllers with sensors and actuators on the factory floor. Data flows seamlessly between these devices, ensuring precise and efficient operations.
In summary, RS-485’s robustness, scalability, and reliability make it the preferred communication standard for PROFIBUS in industrial environments.
Differences Between RS-485 and RS-232 in PROFIBUS
Differences Between RS-485 and RS-232 in PROFIBUS
hen PROFIBUS Uses RS-232 for Specialized Applications
While RS-485 is the backbone of PROFIBUS communication, RS-232 has a niche role in specialized applications. Its point-to-point communication capabilities and simplicity make it valuable in certain scenarios.
One common use of RS-232 in PROFIBUS networks is for device configuration and diagnostics. When setting up or troubleshooting a PROFIBUS device, engineers often use RS-232 to establish a direct connection between the device and a computer or programming tool. This allows for easy parameter adjustment and real-time diagnostics without interfering with the main RS-485 network.
RS-232 is also used in legacy systems where older equipment lacks RS-485 support. In such cases, RS-232 serves as a bridge, enabling these devices to communicate with modern PROFIBUS networks through protocol converters or gateways.
Another application is in testing and simulation. During the design phase of automation systems, RS-232 connections are used to test individual devices or simulate network conditions. This helps engineers verify device functionality and communication reliability before deployment.
However, RS-232’s limitations, such as its short communication range and lack of multi-drop capability, mean it is unsuitable for large-scale fieldbus applications. Its use is typically restricted to auxiliary tasks that do not require robust network performance.
In summary, RS-232 plays a supportive role in PROFIBUS networks, providing a simple and effective solution for configuration, diagnostics, and legacy system integration.
Ensuring Compatibility Between RS-485 and PROFIBUS Networks
Ensuring compatibility between RS-485 and PROFIBUS networks is critical for seamless communication and efficient system performance. Since RS-485 forms the foundation of PROFIBUS DP, proper implementation is essential.
1. Network Design
A well-designed PROFIBUS network ensures optimal communication over RS-485. Devices must be properly terminated at both ends of the network using 120-ohm resistors to prevent signal reflections. This step is crucial for maintaining data integrity, especially in long-distance installations.
2. Cable Selection
Using high-quality PROFIBUS cables is essential. These cables are designed to meet RS-485 specifications, ensuring resistance to electromagnetic interference (EMI). Proper shielding and grounding are also necessary to minimize noise and maintain signal clarity.
3. Addressing and Configuration
Each device in an RS-485-based PROFIBUS network must have a unique address to avoid conflicts. Addressing is typically configured during setup, ensuring that each device communicates correctly with the master controller.
4. Repeaters and Segmentation
For networks exceeding the RS-485 distance or device limits, repeaters can extend communication range and add more devices. Segmenting the network with repeaters improves reliability and simplifies troubleshooting.
5. Integration with RS-232
When integrating RS-232 devices into an RS-485-based PROFIBUS network, protocol converters or gateways are required. These devices translate RS-232 signals into RS-485-compatible formats, ensuring seamless communication.
By following these best practices, you can ensure compatibility and maintain the reliability of RS-485-based PROFIBUS networks. Proper design, configuration, and maintenance are the keys to successful integration.
Conclusion
PROFIBUS relies heavily on RS-485 for its robust and efficient communication in industrial applications. RS-232, while limited, plays a complementary role in configuration and diagnostics. Understanding how these standards work together helps engineers design and maintain reliable PROFIBUS networks that meet the demands of modern automation systems