Key Takeaway
Setting a proportioning valve involves adjusting it to achieve the desired flow or pressure ratio. Begin by consulting the manufacturer’s instructions to understand the valve’s adjustment mechanism, which may involve turning a screw or knob. Use a pressure gauge or flow meter to monitor the system’s output as you make adjustments.
Gradually adjust the valve while observing the system’s performance, ensuring that the desired proportions are achieved without causing instability. Once set, secure the adjustment mechanism to prevent unintentional changes and perform regular checks to maintain optimal performance.
Steps for Setting a Proportioning Valve
Setting a proportioning valve begins with understanding the system requirements and desired flow ratios. Initial setup involves verifying proper valve installation and ensuring all connections are secure. The valve must be properly oriented according to flow direction indicators.
Calibration involves adjusting the valve’s internal mechanisms to achieve the desired flow distribution. This typically requires measuring flow rates at each outlet and making fine adjustments until the target ratios are achieved. Proper tools and accurate flow measurement equipment are essential.
Final setup includes verifying stable operation across the expected range of system conditions. This involves testing the valve under various flow rates and pressures to ensure consistent performance. Documentation of final settings and performance data is important for future reference.
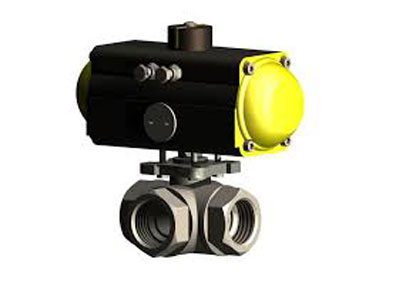
Tools Required for Accurate Setting
To accurately set proportional valves, specialized tools such as flow meters, pressure sensors, and electronic controllers are necessary. These tools ensure precise calibration of the valve to meet system requirements.
Flow meters are used to measure the flow rate, while pressure sensors monitor the system’s pressure to ensure the valve is performing correctly. Electronic controllers allow fine-tuning of the valve settings based on input signals.
Accurate setting of proportional valves also requires careful attention to the control signal range and the specific system parameters to ensure optimal performance without excessive energy consumption or system instability.
You May Like to Read
Common Mistakes and How to Avoid Them
One common mistake when setting a proportioning valve is making large adjustments too quickly. This can cause pressure spikes or erratic valve behavior, which leads to inefficient system performance.
Instead, make small, gradual adjustments and test the system after each one. Another mistake is failing to verify the system’s pressure and flow requirements before setting the valve. This can result in an improperly set valve that doesn’t provide the desired performance. Additionally, neglecting to monitor the valve’s performance during operation is a frequent oversight, which can lead to undetected issues in the system. To avoid these mistakes, always consult the valve’s manual, use the proper tools, and regularly test the valve after adjustments.
Testing and Calibration Procedures
Testing and calibrating a proportioning valve is an ongoing process to ensure it is operating at its best. After initial settings, it’s crucial to monitor the pressure and flow to ensure they remain stable under varying conditions. To calibrate, use a calibration kit or system tester to verify that the valve is responding correctly to control signals. During calibration, adjust the set points incrementally and observe the valve’s performance until it reaches the desired operational range.
After calibration, perform a stress test to confirm that the valve operates effectively under maximum load conditions. Regular testing is recommended to ensure continued accuracy, as changes in system conditions can affect valve performance over time.
Ensuring Long-Term Stability and Performance
Ensuring long-term stability and performance of a proportioning valve requires regular maintenance and checks. Over time, components such as springs, seals, and valve seats can wear down, affecting the valve’s ability to maintain accurate settings. Periodically inspecting these components for wear is crucial, and they should be replaced as needed to avoid performance degradation.
It’s also important to monitor the control signals and pressure regularly to ensure they remain within the proper range. If any discrepancies are noticed, recalibrating the valve can restore optimal performance. Regularly checking for accuracy ensures that the valve consistently functions as expected and minimizes the risk of system failure.
Additionally, regular cleaning of the valve and its components helps prevent debris build-up that could interfere with its function. Keeping the valve clean and free of obstructions improves the flow accuracy and extends the life of the valve. Following the manufacturer’s recommended maintenance schedule will help ensure the valve continues to operate reliably for years.
Conclusion
Setting a proportioning valve involves adjusting it to achieve the desired flow or pressure levels. This process requires understanding the valve’s operation and control mechanisms, as well as the specific requirements of the system.
Proper calibration ensures optimal performance and efficiency, preventing issues such as overpressure or inadequate flow. Regular maintenance and monitoring are also essential to maintain the valve’s functionality and extend its lifespan, ultimately contributing to the system’s overall reliability.