Key Takeaway
Designing a VFD control panel involves several key steps. First, you need to determine the motor specifications and the required voltage and frequency for your application. This will help you choose the right VFD unit.
Next, ensure the panel includes necessary components like overload protection, circuit breakers, and input/output terminals. Proper wiring and grounding are essential for safety and performance. The control panel should also be designed for easy monitoring and adjustments, so include indicators and control buttons.
Finally, ensure the VFD control panel meets safety standards and is housed in a suitable enclosure to protect against dust, moisture, and other environmental factors. Proper design ensures efficient motor control, energy savings, and long-term reliability.
Understanding the Key Requirements for VFD Panel Design
Before diving into the specifics of VFD control panel design, it’s crucial to understand the fundamental requirements. These include the motor’s specifications, the operational environment, and the purpose of the application. Every VFD control panel must meet the unique needs of the system it’s designed for.
First, evaluate the type of motor that will be controlled. Factors like motor size, type (squirrel cage, synchronous, etc.), and voltage ratings must be considered. The VFD should match the motor’s power rating, ensuring the system functions optimally. Additionally, consider the application’s load characteristics. Whether the motor will experience constant or variable loads will influence the design of the VFD.
The environment in which the control panel will be installed is also a significant factor. Temperature, humidity, and exposure to dust or chemicals can all impact the panel’s performance. The design must account for these environmental conditions to prevent system failure or damage.
Finally, safety standards and local regulations must be met. The design should adhere to national and international standards for electrical safety, including proper insulation, grounding, and protection against electrical faults. With these basic requirements in mind, the next step is selecting the right VFD for the application.
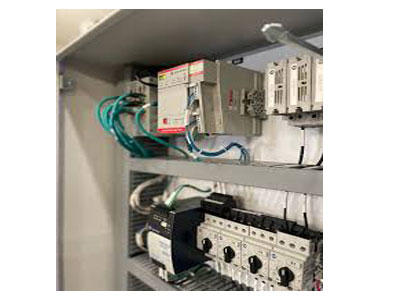
Selecting the Right VFD for Specific Applications
Selecting the right VFD is crucial to ensure that the motor and system work together efficiently. The VFD needs to be compatible with the motor in terms of power rating, voltage, and speed control requirements. The first step in selecting a VFD is to check the motor’s specifications, including its rated voltage, current, and horsepower. The VFD should match these values to avoid any mismatch that could cause operational issues or even damage.
The next consideration is the type of control needed for the application. For example, if precise speed control is needed, a VFD with vector control or direct torque control (DTC) might be required. These advanced control methods provide greater precision in managing motor performance compared to simpler VFDs that offer scalar control.
In addition to motor compatibility and control types, you should consider the installation environment. Is the VFD going to be used in harsh conditions, such as high temperatures, moisture, or exposure to dust? If so, ensure that the VFD has an IP rating that meets the environmental requirements.
Lastly, consider the future scalability of the VFD. If the motor or application demands change in the future, the VFD should be capable of handling additional loads or integrating with other control systems without requiring a full redesign.
By carefully selecting the right VFD, you ensure that your control panel operates at peak efficiency and reliability.
Components and Layout Planning for Efficient Design
The next step in designing a VFD control panel is planning the layout and selecting the components. A well-thought-out layout is crucial for both efficient operation and ease of maintenance. The components within the panel should be arranged in a way that ensures adequate airflow, minimizes heat buildup, and makes future repairs or upgrades straightforward.
Start by determining the size and dimensions of the control panel. This depends on the number and type of components it will house, including the VFD, circuit breakers, disconnect switches, fuses, contactors, and control relays. Sufficient space is needed to avoid overcrowding, which can lead to overheating or poor ventilation.
Next, plan the layout of these components. The VFD should be easily accessible, with sufficient space around it to facilitate cooling and prevent overheating. Components like circuit breakers and contactors should be placed for easy access during maintenance or replacement. Ensure that all components are positioned in a way that minimizes wiring complexity and prevents electrical interference.
Effective cable management is key to a successful VFD panel design. Properly route power and control cables to avoid potential damage and minimize electrical noise. Use wire ducts and cable ties to keep everything neat and secure. Adequate separation between power and control wiring is important to reduce electromagnetic interference (EMI) and ensure reliable signal transmission.
Finally, incorporate ample ventilation and cooling solutions, such as fans or vented panels, to maintain optimal operating temperatures within the panel. With these considerations in mind, you can create a control panel that is both efficient and easy to maintain.
Wiring and Protection Considerations in VFD Panel Design
Wiring is a critical aspect of VFD control panel design. Proper wiring ensures the safe and reliable operation of the entire system. When selecting wiring, make sure to choose the correct wire sizes that can handle the current and voltage requirements of the VFD and motor. Oversized or undersized wires can cause overheating or power loss, leading to operational inefficiencies.
For protection, include necessary devices such as circuit breakers, fuses, and surge protectors in your design. These components safeguard against electrical faults, such as overcurrent or short circuits. The circuit breaker should be rated for the VFD’s operating current, while the fuses should be rated for the maximum current the system can handle.
One of the most important protection features is the VFD’s overload protection, which prevents damage to the motor by limiting the current when the motor operates beyond its rated capacity. Additionally, ensure the VFD has thermal protection to prevent overheating and damage to the drive components.
Another key consideration is grounding. Proper grounding prevents electrical shock hazards and ensures the system’s stability. Use an appropriate grounding method that adheres to electrical safety standards.
Wiring should also account for the operational conditions of the VFD. If the system is exposed to extreme temperatures or moisture, ensure that the wiring is rated for those conditions. Proper insulation and weatherproofing will extend the lifespan of your control panel and its components.
Testing, Commissioning, and Troubleshooting VFD Control Panels
Once the design is complete and the panel is assembled, it’s time for testing and commissioning. This step ensures that the VFD control panel operates correctly and meets all performance requirements. Start by performing a visual inspection of all components, checking for any loose connections or potential hazards.
Next, perform functional testing. Verify that the VFD operates according to the specifications and controls the motor as expected. Check the control signals and feedback loops to ensure that the motor’s speed and torque are correctly regulated.
During commissioning, monitor the system for any abnormal behavior, such as motor overheating, erratic speeds, or excessive vibrations. Troubleshoot any issues that arise and ensure that the protection mechanisms, such as overcurrent and thermal protection, are functioning properly.
Finally, ensure the system is properly calibrated for its intended application. This includes setting the correct parameters for motor speed, acceleration, deceleration, and torque control. After testing, document the results and provide any necessary training to operators.
Thorough testing and commissioning are crucial for the successful operation of the VFD control panel, and it ensures that the system will run reliably for years.
Conclusion
Designing a VFD control panel involves a systematic approach that starts with understanding the application requirements and ends with thorough testing and commissioning. Key considerations, such as selecting the right VFD, planning the layout, and ensuring proper wiring and protection, are essential for building a reliable and efficient control panel. By focusing on these crucial elements, you can design a VFD control panel that enhances motor performance, reduces energy consumption, and ensures long-term system reliability.