Key Takeaway
To calculate the speed of a servo motor, you can use the formula speed = distance/time. For example, if a servo motor rotates 60 degrees in 0.2 seconds, the speed is calculated as 60 degrees/0.2 seconds, resulting in 300 degrees per second. This basic calculation helps determine how fast the motor can move to complete a task.
When calculating servo speed, it’s important to consider factors like acceleration time and load, which can affect the motor’s actual speed. Ensuring accurate calculations helps in optimizing the motor’s performance for your specific application.
Understanding the Basics of Servo Motor Speed Calculation
Calculating the speed of a servo motor is a fundamental task in ensuring that the motor performs optimally for its intended application. Servo motor speed is typically measured in revolutions per minute (RPM) and is calculated based on the distance the motor’s shaft moves within a given time. The basic formula used is speed = distance/time, where distance refers to the angular displacement (usually in degrees or radians), and time is the period taken for that movement. This simple calculation gives you a general idea of how fast the motor is operating, which is crucial for applications requiring precise control, such as in robotics or CNC machinery. Understanding these basics sets the foundation for more complex speed adjustments and ensures that the motor operates within its desired parameters.
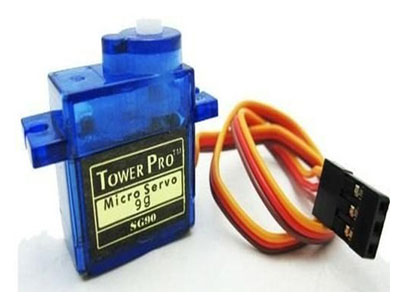
Formulas and Tools for Calculating Servo Speed
Accurately calculating servo speed involves using specific formulas that are tailored to the motor’s application. A basic example would be calculating angular speed: if a servo motor rotates 60 degrees in 0.2 seconds, the speed is calculated as 60 degrees divided by 0.2 seconds, which equals 300 degrees per second. This measurement can then be converted into RPM (revolutions per minute) if required, by multiplying the angular speed by a conversion factor. This straightforward calculation helps engineers determine how fast a motor is moving, which is crucial for tasks that require precise control, such as in robotics or automated machinery.
In addition to formulas, various tools are employed to measure and control servo speed. Tachometers are commonly used for direct speed measurements by detecting the frequency of the motor’s rotations, providing real-time data. Software-based encoders, often integrated into the motor, offer another way to measure speed with high accuracy. They count the number of rotations and translate this data into usable speed metrics, ensuring that the motor operates within the desired parameters. Furthermore, pulse width modulation (PWM) is frequently used to adjust and control speed, allowing for precise tuning based on the application’s needs. By using these tools and formulas, engineers can ensure that the servo motor performs optimally, meeting the specific requirements of each task.
Factors to Consider When Calculating Speed
When calculating the speed of a servo motor, several factors must be carefully considered to ensure accurate results. One of the most significant factors is the load on the motor. Heavier loads require more torque, which can reduce the motor’s speed. This relationship between load and speed must be factored into calculations to avoid overestimating the motor’s capabilities. Additionally, the input voltage plays a crucial role; higher voltages generally result in increased speed, but this must be managed carefully. Excessive voltage can lead to overheating, which not only decreases performance but also risks damaging the motor.
Environmental factors like temperature and humidity also impact the motor’s performance. High temperatures can cause components to expand, potentially slowing down the motor or causing it to operate inefficiently. Humidity can affect electronic components, leading to potential malfunctions that influence speed. Finally, it’s important to consider the motor’s mechanical limitations, such as the maximum RPM specified by the manufacturer. Operating the motor beyond these limits can result in mechanical strain or even failure. By taking these factors into account, engineers can make precise speed calculations, leading to better motor performance and longevity, ensuring that the motor operates within its safe and optimal range.
Examples of Speed Calculation in Real-World Applications
Accurate speed calculations are crucial in real-world applications where precision and efficiency are paramount. Take the example of a CNC machine, where precise control is necessary for cutting materials. The speed of the servo motor driving the cutting tool must be carefully calculated to ensure smooth and accurate operation. For instance, if the motor needs to rotate the tool 180 degrees in one second, the speed calculation would be 180 degrees per second. This figure helps determine the appropriate RPM needed to achieve the desired cut quality without causing excessive wear on the tool or the motor. Such calculations are vital to maintaining the integrity of the operation, preventing issues like tool breakage or overheating, which could lead to costly downtime.
In robotics, accurate speed calculations are equally important, especially in tasks that require quick and precise movements, such as assembly or welding. Here, the motor’s speed must be calculated to ensure the robot can perform its tasks with high accuracy and efficiency. For example, if a robot arm needs to move from one position to another in 0.5 seconds, the speed calculation will dictate how fast the motor needs to operate to achieve this movement seamlessly. These calculations ensure that the robot performs consistently, meeting the demands of high-speed production environments without compromising precision. These real-world examples underscore the importance of accurate speed calculations in optimizing performance and ensuring reliable operation across various applications.
Common Mistakes to Avoid in Speed Calculations
When calculating the speed of a servo motor, certain common mistakes can lead to inaccurate results, potentially compromising performance. One frequent error is neglecting to account for the motor’s load. The load can significantly impact the motor’s speed; heavier loads require more torque, which can slow the motor down. Assuming the motor will operate at its maximum speed without considering the load can result in overheating and mechanical strain, leading to premature wear or even motor failure. This mistake underscores the importance of incorporating load considerations into speed calculations to ensure that the motor operates within safe and effective parameters.
Another common mistake is overlooking the impact of input voltage on motor speed. Without proper voltage management, the motor may run too fast or too slow, leading to inefficiencies and potential damage. For example, applying too much voltage can cause the motor to exceed its rated speed, increasing the risk of overheating and reducing its lifespan. Additionally, environmental factors such as temperature changes are often overlooked in speed calculations.
Conclusion
Accurate calculation of servo motor speed is essential for optimizing performance and ensuring the longevity of the motor in various applications. By understanding the basic principles, using the correct formulas and tools, and considering all relevant factors, engineers can achieve precise speed control that meets the specific needs of their projects. Whether for high-speed robotics, precise CNC machining, or other applications requiring controlled motion, accurate speed calculations are key to maximizing efficiency and reliability. Avoiding common mistakes and regularly reviewing speed settings can help maintain optimal performance, ensuring that the servo motor operates within its intended parameters and delivers consistent results over time.