Key Takeaway
To calculate and size VFD panels for motors, start by determining the motor’s power rating, typically in horsepower (HP) or kilowatts (kW). The VFD should match or exceed the motor’s power rating to ensure proper operation.
Next, consider the input voltage and phase configuration of the motor. VFDs come in single-phase or three-phase configurations, so choose one that aligns with your motor’s needs. Additionally, factor in the environmental conditions where the VFD panel will operate, such as temperature and humidity, as this affects the panel’s cooling requirements.
Finally, ensure the VFD panel has proper protection features, like overload protection and short-circuit protection, to safeguard the motor and panel. By considering these factors, you can properly size the VFD panel to ensure efficient and safe operation.
Understanding the Basics of VFD Panel Sizing
When sizing a VFD panel for a motor, the first step is understanding the basic electrical requirements of the motor and the application. The VFD must be sized appropriately to handle the motor’s full-load current (FLC) and provide enough capacity to support the expected load without overloading. The right VFD ensures that the motor runs efficiently and is protected against electrical faults and overheating.
At the core of VFD sizing is the motor’s full-load current (FLC). The FLC is the current that the motor draws when operating at its rated power output. This figure is essential because the VFD must be able to supply enough current to the motor at full load. Additionally, the voltage rating of the VFD should match the motor’s voltage requirements, which is typically specified on the motor nameplate.
A general rule of thumb when selecting a VFD is that the drive should be able to supply 1.2 to 1.5 times the motor’s rated current. This ensures that the drive can handle any overload conditions that may occur during startup or during high-torque demands. It’s also important to ensure that the VFD panel’s power rating (in kilowatts or horsepower) is sufficient for the motor’s load requirements.
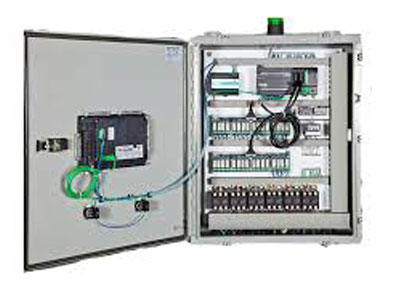
Key Factors to Consider When Sizing VFD Panels for Motors
There are several key factors to consider when sizing VFD panels for motors. These factors go beyond just the motor’s electrical characteristics and include environmental conditions, motor application, and specific performance requirements.
1. Motor Rating: As mentioned earlier, the motor’s full-load current (FLC) is one of the most critical factors in sizing a VFD. But beyond that, you should also take into account the motor’s horsepower (HP) and voltage ratings. A mismatch in voltage ratings between the VFD and the motor can lead to poor performance or even damage.
2. Motor Starting and Overload Conditions: The type of motor starting (such as across-the-line, star-delta, or soft starting) affects the VFD panel’s sizing. For example, a motor that requires high starting torque will need a larger VFD to accommodate the surge of current during startup. The VFD should be able to handle these brief overload conditions without tripping or overheating.
3. Load Type: The type of load that the motor is driving is a crucial consideration when sizing the VFD. For instance, centrifugal loads like fans and pumps typically require less torque and can run at a constant speed, while conveyor belts and crushers demand more torque variation. Understanding the nature of the load will help in selecting the appropriate VFD to ensure efficient operation.
4. Control Requirements: The control features required for your motor also impact the VFD sizing. If the motor needs precise speed control or torque regulation, you may need a VFD with advanced features like closed-loop control or vector control. The complexity of control demands higher capacity and more advanced VFD capabilities.
5. Environmental Conditions: Environmental conditions, such as temperature, humidity, and the presence of dust or corrosive substances, also influence the VFD panel size. In harsh environments, a VFD with higher protection ratings (such as an IP54 or IP65 enclosure) will be necessary to ensure the panel’s durability. Additionally, high ambient temperatures require VFDs with better cooling mechanisms.
You May Like to Read
How to Calculate the Motor's Full Load Current (FLC) for VFD Panel Sizing
Calculating the motor’s Full Load Current (FLC) is one of the most important steps in VFD panel sizing. The FLC represents the current the motor will draw when operating at its rated full load. It ensures that the VFD selected is capable of providing the right amount of current without causing damage to the motor or the VFD.
To calculate the FLC, you can use the following formula, which is commonly used for three-phase AC motors:
FLC = (Motor Horsepower × 746) / (Voltage × √3 × Efficiency × Power Factor)
Where:
Motor Horsepower (HP) is the power rating of the motor (1 HP = 746 watts).
Voltage (V) is the motor’s rated voltage.
Efficiency is the motor’s efficiency at full load.
Power Factor (PF) is a measure of how efficiently the motor uses electrical power.
For example, if a 10 HP motor has a voltage rating of 400V, efficiency of 90%, and a power factor of 0.9, the FLC can be calculated as follows:
FLC = (10 × 746) / (400 × √3 × 0.9 × 0.9)
FLC ≈ 15.5 Amps
This means that the VFD should be capable of supplying at least 15.5 amps of current at full load to ensure proper motor operation. To accommodate for startup surges, VFDs are usually sized with an additional 10-20% margin above the calculated FLC.
Determining the Right VFD Size Based on Motor Type and Application
Once you have the motor’s full-load current (FLC), it’s time to determine the appropriate VFD size based on the motor type and application. Different motor types require different considerations when selecting the VFD size.
1. Standard Induction Motors: Standard squirrel-cage motors are the most common type of motor and are usually the simplest to size for VFD panels. For these motors, a VFD sized based on the motor’s FLC, with an added safety margin, is typically sufficient. However, if the motor experiences high starting torque or frequent start-stop cycles, a larger VFD may be necessary to prevent overheating.
2. High Torque or High Inertia Loads: For motors driving high-torque loads (such as crushers or large pumps), the VFD should be selected with a larger capacity to handle the additional torque requirements. Similarly, high-inertia loads, such as large fans or heavy machinery, can require VFDs with more robust starting capability to handle the initial surge.
3. Continuous vs. Intermittent Duty: If the motor operates continuously (24/7), such as in HVAC applications, a VFD designed for continuous duty is necessary. For motors operating intermittently (such as in lifting equipment), you can size the VFD with a lower rating since the load will be intermittent and not require continuous high performance.
The VFD size should always be selected based on the worst-case scenario for the motor’s performance, ensuring that it can operate efficiently without overheating or failure.
Important Electrical and Environmental Considerations for VFD Panel Sizing
When sizing VFD panels, electrical and environmental factors play a significant role. These considerations ensure that the VFD operates efficiently and does not experience premature failure.
1. Electrical Considerations:
Voltage Compatibility: Ensure that the VFD voltage rating matches the motor’s voltage.
Current Rating: The VFD should be capable of handling the motor’s FLC and any potential surges.
Harmonics: VFDs can generate harmonic distortion, which can affect other equipment in the system. Harmonic filters may be needed for sensitive applications.
Short Circuit Protection: Proper protection devices, such as fuses or circuit breakers, should be incorporated to protect the motor and VFD from electrical faults.
2. Environmental Considerations:
Temperature: VFDs typically operate best in temperatures ranging from 0°C to 40°C. In hotter environments, forced air cooling or external cooling systems may be needed.
Humidity: Humidity can cause corrosion or condensation inside the VFD panel, so ensuring proper ventilation and protection is essential.
Dust and Debris: Dusty environments require VFDs with sealed enclosures (IP65 or higher ratings) to prevent damage from particles.
Conclusion
In conclusion, correctly sizing VFD panels for motors is critical for achieving optimal performance, energy efficiency, and longevity. By following the correct procedures and considering all the relevant factors—such as the motor’s full-load current, type, application, and environmental conditions—you ensure that your VFD system can handle the motor’s needs without overheating or damaging sensitive components. Always be sure to factor in a safety margin and consult the manufacturer’s recommendations for both the motor and the VFD to ensure the best match. With the right sizing, you can expect smoother operations, improved efficiency, and longer-lasting equipment.