Key Takeaway
Adjusting a flow control valve involves fine-tuning the valve to achieve the desired flow rate. Begin by identifying the flow requirement of your system and ensuring the valve is compatible with those parameters. Slowly turn the valve’s adjustment mechanism, such as a knob or screw, while monitoring the flow rate using gauges or system indicators. Small incremental adjustments are recommended to avoid overcompensation.
After setting the valve, verify its performance by observing the system’s behavior under operating conditions. Ensure the valve operates smoothly without causing pressure fluctuations or irregular flow. Periodic checks and recalibration are necessary to maintain system efficiency and prevent wear and tear.
Steps to Adjust a Flow Control Valve
Adjusting a flow control valve involves setting the valve to achieve the desired flow rate. Begin by consulting the manufacturer’s instructions to understand the adjustment mechanism.
Use a flow meter to monitor the system’s output as you make adjustments, ensuring the desired flow rate is achieved. Once set, secure the adjustment mechanism to prevent unintentional changes.
Regular checks and maintenance are essential to maintain optimal performance. This includes periodic inspections and recalibration to ensure the valve continues to provide reliable flow control.
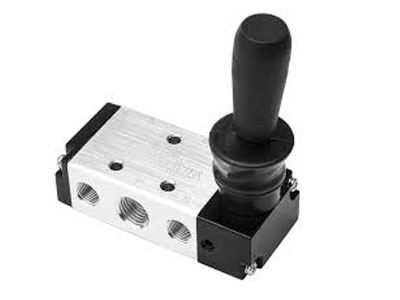
Tools Required for Adjustment
Adjusting flow control valves (FCVs) often requires a set of specialized tools to ensure precise control and system optimization. The adjustable wrench is a commonly used tool for loosening or tightening valve fittings and ensuring the secure placement of the valve. For precise settings, a torque wrench may be necessary, especially when working with valves in high-pressure systems to avoid over-tightening.
Digital tools, such as a flowmeter or pressure gauge, are essential for monitoring the fluid’s flow rate and pressure during adjustments. These tools provide real-time data, enabling operators to make fine-tuned adjustments to the valve. Additionally, an actuator calibration tool is needed when working with automated FCVs, ensuring that the actuator aligns perfectly with the control system for optimal functionality.
You May Like to Read
Common Mistakes and How to Avoid Them
When working with Flow Control Valves (FCVs), engineers and technicians must be aware of common mistakes that can lead to poor system performance, damage to equipment, and increased costs. One of the most frequent errors is improper valve sizing. Selecting a valve that is too large or too small for the system can lead to inefficient flow control, excessive energy consumption, or system failure. An oversized valve may result in high-pressure drops, increased wear on other system components, and unnecessary energy use, while an undersized valve may not provide enough flow regulation, leading to pressure surges or equipment malfunction. To avoid this mistake, it’s essential to carefully assess the system’s flow rate, pressure conditions, and other operating parameters before choosing the valve size.
Another common mistake involves the incorrect installation of FCVs. FCVs must be installed in the proper orientation to ensure optimal performance. For example, installing a valve backward can cause the valve to malfunction, as it will not be able to regulate flow correctly. Additionally, improper installation can lead to leaks, flow irregularities, or excessive wear on the valve components. Engineers should follow manufacturer guidelines and industry best practices for valve installation, ensuring that the valve is correctly aligned with the system and that all connections are secure and leak-free.
Lastly, neglecting regular maintenance is a mistake that can shorten the lifespan of FCVs and reduce their efficiency. Over time, FCVs can accumulate dirt, debris, or corrosion, which can obstruct the flow of fluids, cause wear on valve seats, or damage actuator components. Regular cleaning, inspection, and replacement of worn-out parts are essential to maintaining valve performance. Furthermore, recalibrating automated FCVs ensures that they continue to respond accurately to control signals, preventing issues like overcorrection or failure to adjust the flow rate. Proper training of maintenance personnel and keeping a maintenance schedule can help avoid these costly mistakes and ensure long-term valve performance.
Testing and Calibration Procedures
Testing and calibration of Flow Control Valves (FCVs) are critical for ensuring that they perform as expected. The first step in testing is to check the valve for proper installation and ensure it is correctly sized for the system. Next, the valve is subjected to flow conditions to observe its response to changes in pressure and flow rate. The primary objective of this process is to confirm that the valve opens and closes correctly within the required parameters, ensuring that it maintains consistent flow control throughout the system.
The calibration of FCVs involves adjusting their opening and closing points to match the system’s specific requirements. This ensures that the valve accurately controls the flow rate within the desired range. Calibration is typically done using specialized equipment that measures the pressure and flow conditions, allowing the technician to fine-tune the valve’s performance. This process helps prevent underperformance or failure due to incorrect flow rates.
Regular testing and calibration of FCVs are essential to maintaining system efficiency and safety. They help identify any potential issues, such as leakage or malfunctioning, which could lead to costly repairs or damage to the system. Routine inspections also ensure that the FCV remains in optimal condition, allowing for smooth and reliable operation over time.
Ensuring Long-Term Stability and Performance
Flow Control Valves (FCVs) are integral to maintaining the stability and performance of fluid systems. Proper valve selection is the foundation of long-term reliability. Ensure the valve matches the operating pressure, temperature, and flow requirements of the system.
Routine maintenance is essential to prevent issues like wear, corrosion, or debris buildup. Regularly inspect seals, gaskets, and moving parts, and replace any components showing signs of wear. Lubricating the valve’s mechanisms can improve performance and reduce friction-related damage over time.
Monitoring system conditions, such as pressure fluctuations or flow irregularities, helps detect potential problems early. Advanced control systems with real-time monitoring capabilities can enhance the performance of FCVs by enabling timely adjustments and preventive maintenance, ensuring consistent operation over the valve’s lifespan.
Conclusion
Adjusting a flow control valve involves setting the valve to achieve the desired flow rate. Begin by consulting the manufacturer’s instructions to understand the adjustment mechanism, which may involve turning a screw or knob.
Use a flow meter to monitor the system’s output as you make adjustments, ensuring the desired flow rate is achieved. Once set, secure the adjustment mechanism to prevent unintentional changes and perform regular checks to maintain optimal performance.