Key Takeaway
A servo drive varies the speed of a servo motor by controlling the frequency and voltage of the power it supplies. The most common method used is Pulse Width Modulation (PWM), where the drive sends pulses of varying widths to the motor. By adjusting the width of these pulses, the drive can control the amount of power delivered, which directly impacts the motor’s speed.
When the pulse width is increased, more power is sent to the motor, resulting in higher speed. Conversely, reducing the pulse width decreases the motor’s speed. This method allows for precise control over the motor’s speed, making it ideal for applications that require variable speed and accurate positioning.
Principles of Speed Variation in Servo Motors
The speed of a servo motor is primarily governed by the frequency of the electrical signals sent to it. A higher frequency results in increased motor speed, while a lower frequency reduces the speed. The servo drive adjusts these frequencies in real-time, responding to the control inputs it receives from the system’s controller. Additionally, the servo drive continuously monitors the motor’s performance through feedback mechanisms, making adjustments to maintain the desired speed and ensure smooth operation. This dynamic interaction between the servo drive and the motor allows for highly accurate speed control, even under varying load conditions.
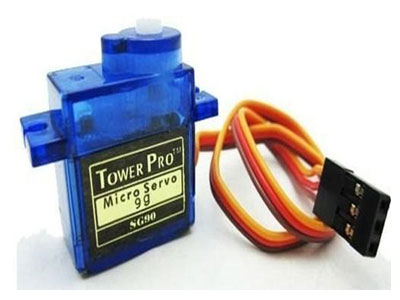
The Role of Pulse Width Modulation (PWM) in Speed Control
Pulse Width Modulation (PWM) is a fundamental technique used by servo drives to control the speed of motors with high precision. Essentially, PWM involves sending electrical pulses to the motor, where the width of each pulse determines the amount of power delivered. The servo drive adjusts the duration of these pulses to increase or decrease the motor’s speed. For example, a longer pulse duration within each cycle provides more power, resulting in a higher motor speed. Conversely, shorter pulses deliver less power, slowing the motor down. This method is highly efficient because it allows for fine control over the motor’s speed without the need for complex mechanical adjustments.
PWM is widely favored in industrial applications because it offers precise control while minimizing energy loss. Unlike continuous voltage control, PWM switches the power on and off rapidly, which reduces heat generation and improves overall efficiency. This precision is crucial in applications like robotics, CNC machining, and other automated systems where exact speed regulation is necessary to maintain accuracy and quality. Furthermore, the ability to rapidly adjust motor speed using PWM makes it ideal for dynamic environments where the load or operating conditions might change frequently.
Impact of Voltage and Current on Speed
In addition to PWM, the voltage and current supplied to the servo motor are critical factors that influence its speed and overall performance. Voltage is directly related to the maximum speed the motor can achieve—higher voltage allows the motor to reach higher speeds. However, simply increasing the voltage is not enough; it must be carefully calibrated to match the motor’s design specifications to avoid overheating or damaging the motor. The current, on the other hand, is closely tied to the torque output of the motor. A higher current enables the motor to produce more torque, which is essential for accelerating the motor to its desired speed or maintaining speed under varying loads.
Proper management of voltage and current is crucial in ensuring that the motor operates efficiently. If the voltage is too high, it could lead to excessive heat generation, reducing the motor’s lifespan. Conversely, if the voltage is too low, the motor might not achieve the desired speed, leading to inefficiencies. Similarly, inadequate current supply can cause the motor to struggle under load, resulting in poor performance and potential stalling. Therefore, a well-calibrated servo drive must balance voltage and current to ensure that the motor operates within its optimal range, delivering consistent and reliable performance across different operating conditions.
This balance is especially important in applications that demand high precision and reliability, such as in aerospace, medical devices, and automated manufacturing systems. By carefully managing these electrical parameters, engineers can maximize the motor’s efficiency and longevity, ensuring smooth and accurate operation in even the most demanding environments.
Techniques for Precise Speed Regulation
Achieving precise speed regulation in servo motors involves employing advanced control techniques that can adapt to varying conditions while maintaining the desired performance. One of the most effective methods is the use of closed-loop control systems. In a closed-loop system, the servo drive continuously monitors the motor’s speed through feedback devices, such as encoders or resolvers. The feedback provides real-time data on the motor’s actual speed, which is then compared to the target speed. If there is any deviation, the system automatically adjusts the input signals to correct the error, ensuring that the motor maintains its specified speed even when external factors, such as load changes or supply fluctuations, come into play. This feedback loop is essential for applications that require high precision, such as robotics, where exact positioning and speed control are critical.
In addition to closed-loop control, using high-resolution encoders is another technique that enhances speed regulation. These encoders provide detailed information about the motor’s position and speed, allowing the control system to make finer adjustments. Coupled with sophisticated control algorithms, such as Proportional-Integral-Derivative (PID) controllers, the system can achieve smooth and accurate speed regulation. These algorithms allow the system to predict and respond to changes quickly, minimizing the risk of overshoot or oscillation. The combination of these techniques ensures that the motor operates within the desired parameters, providing reliable performance in demanding environments.
Avoiding Common Speed Control Pitfalls
While modern servo drives offer advanced capabilities for speed control, several common pitfalls can undermine their effectiveness if not addressed properly. One of the most frequent issues is improper tuning of the control parameters. Tuning refers to the adjustment of the control system’s settings, such as the gains in a PID controller. If these parameters are not correctly set, the motor may exhibit undesirable behaviors, such as oscillations or instability, where it continuously overshoots or undershoots the target speed. This can lead to excessive wear on the motor and reduced precision in the application. To avoid this, it is crucial to perform careful tuning during the initial setup, often involving iterative testing and adjustment to find the optimal settings for the specific motor and load conditions.
Another significant pitfall is an insufficient power supply. The servo drive must be capable of delivering the necessary voltage and current to the motor, especially under varying loads. If the power supply is inadequate, the motor may struggle to reach the desired speed, or worse, it could experience voltage drops that lead to erratic performance or even damage. Ensuring that the power supply is appropriately rated for the motor’s demands is essential. This includes considering factors such as the motor’s peak current requirements during acceleration and the need for stable voltage levels to maintain consistent operation. By addressing these common issues through proper tuning and power management, engineers can ensure that the servo motor delivers precise and reliable speed control in any application.
Conclusion
Accurate speed control is essential for the successful operation of servo motors in various industrial applications. By understanding and leveraging the principles of frequency variation, PWM, and careful management of voltage and current, engineers can achieve precise control over motor speed. Avoiding common pitfalls through proper tuning and adequate power supply ensures that the servo drive performs reliably, delivering the accuracy and responsiveness needed for even the most demanding tasks. With the right approach, servo drives can provide exceptional performance, enhancing the efficiency and effectiveness of automated systems.