Key Takeaway
A single VFD can control multiple motors, but it’s essential to set the parameters correctly. Typically, you can run two motors of different sizes, but you must configure the VFD for the larger motor. This ensures the VFD handles the higher load. However, the smaller motor will lack overload protection, which can lead to potential issues. Always monitor both motors closely and consider using individual overload relays for added safety. This setup is common in applications where simultaneous motor control is needed.
Factors Influencing Motor Control Capacity
The capacity of a VFD to control multiple motors hinges on several factors:
VFD Rating: The power rating and current capacity of the VFD dictate how many motors it can handle.
Motor Characteristics: The size, power requirements, and load types of the motors affect the VFD’s capability.
Application Requirements: Different applications might demand simultaneous or independent motor control, impacting the VFD’s load.
Protection Mechanisms: Ensuring each motor has proper protection (like overload protection) is essential when multiple motors are controlled by a single VFD.
Understanding these factors helps in determining the practical limits and ensures the system operates efficiently.
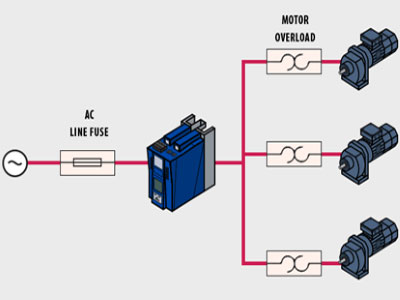
Practical Examples of Multiple Motor Control
Consider a conveyor belt system in a factory. Here, a single Variable Frequency Drive (VFD) can control multiple motors along the belt. Each motor starts simultaneously, providing synchronized movement. This ensures efficient material handling and reduced wear on the motors.
Another example is HVAC systems, where one VFD manages several fans to maintain consistent airflow and pressure. This approach not only saves energy but also extends the lifespan of the equipment by reducing mechanical stress.
These scenarios illustrate the efficiency and cost savings achieved by using one VFD for multiple motors. However, careful planning and setup are crucial. It’s essential to avoid overloading the VFD and ensure smooth operations. Proper configuration and regular maintenance are key to maximizing the benefits of this setup.
In practice, using a single VFD for multiple motors reduces installation costs and simplifies control mechanisms. It provides a unified solution that enhances overall system performance. Always consider the power requirements and operational limits of the VFD to prevent potential issues.
These examples highlight how VFDs can streamline industrial processes, making them more efficient and cost-effective. With proper implementation, this technology can significantly improve productivity in various applications.
You May Like to Read
Benefits and Challenges
Benefits:
Using a single Variable Frequency Drive (VFD) to control multiple motors offers several advantages, especially in industrial applications. Firstly, it’s cost-effective. Instead of installing a separate VFD for each motor, one VFD can manage multiple motors, reducing hardware costs significantly. This also simplifies installation, as there’s less equipment to set up and integrate into the system. Another key benefit is energy savings. With improved control, motors can run at optimal speeds, leading to enhanced energy efficiency. This not only lowers energy bills but also reduces the environmental impact of industrial operations. Additionally, having a centralized control system can simplify maintenance routines. Maintenance teams can monitor and adjust settings from a single point, potentially reducing downtime and improving overall productivity.
Challenges:
However, there are challenges to consider. Configuring a VFD to control multiple motors can be complex. Each motor may have different operational requirements, making the setup process more intricate. Load imbalance is another issue. If the motors are not evenly loaded, it can lead to inefficiencies or even damage the equipment. Managing faults in such a setup can also be challenging. Detecting and isolating faults in a system where multiple motors are controlled by one VFD requires sophisticated diagnostic tools and a high level of expertise. Balancing these benefits and challenges is crucial for successful VFD implementation. Ensuring proper configuration, load management, and fault detection can help harness the full potential of VFDs in multi-motor setups.
Tools and Techniques for Effective Control
To manage multiple motors effectively with one VFD, several tools and techniques are employed. Let’s break down these key methods, ensuring clarity for our understanding.
Load Sharing
Load sharing algorithms are essential for balanced load distribution across motors. They prevent any single motor from being overburdened, ensuring longevity and efficiency. These algorithms continuously monitor and adjust the load, maintaining equilibrium.
Soft Starters
Soft starters gradually ramp up the motor speed, reducing the inrush current. This method not only prolongs motor life but also minimizes mechanical stress. By controlling the acceleration, soft starters help in smooth operations and prevent sudden jerks that can damage equipment.
Overload Relays
Installing overload relays for each motor provides individual protection. These relays detect excessive current and disconnect the motor, preventing overheating and potential damage. They are critical in safeguarding motors against overloads, ensuring safe and reliable operation.
HMI Integration
Human-Machine Interface (HMI) systems allow real-time monitoring and control adjustments. HMIs provide a user-friendly interface to oversee operations, diagnose issues, and make necessary adjustments promptly. This real-time data helps in maintaining optimal performance and quick response to any anomalies.
Implementing these techniques enhances reliability and efficiency in multi-motor VFD applications. By integrating load sharing, soft starters, overload relays, and HMI systems, we ensure a robust and efficient control system for multiple motors, promoting smooth and uninterrupted industrial operations.
Future Trends in VFD Motor Control
The future of VFD (Variable Frequency Drive) motor control looks incredibly promising, with several emerging trends set to revolutionize the industry.
Advanced Algorithms
Enhanced algorithms are making VFDs smarter by improving load management and fault detection. These advanced algorithms can adapt to varying loads, ensuring optimal performance and reducing downtime.
IoT Integration
The integration of the Internet of Things (IoT) is a game-changer for VFDs. With IoT, remote monitoring and predictive maintenance become possible. This means potential issues can be detected and resolved before they cause significant problems, enhancing overall reliability.
Energy Efficiency
Continuous improvements in energy efficiency are at the forefront of VFD development. Modern VFDs are designed to meet stringent energy efficiency standards, which not only save costs but also contribute to environmental sustainability. They optimize energy use, ensuring that motors run at the most efficient speed for any given load.
Smart VFDs
The development of smart VFDs with AI capabilities is another exciting trend. These VFDs can perform autonomous control and optimization, learning from operational data to enhance performance and efficiency. This makes them highly adaptable to various industrial applications, offering unprecedented levels of control and precision.
Conclusion
Maximizing the efficiency of VFD motor control involves understanding the VFD’s capabilities, carefully planning the setup, and employing the right tools and techniques. With advances in technology and growing trends, VFDs will continue to play a crucial role in industrial applications. By leveraging their benefits and mitigating challenges, industries can achieve significant cost savings, enhanced performance, and operational excellence.