Key Takeaway
A pneumatic actuator works by using compressed air to produce mechanical motion. It consists of a cylinder with a piston inside. When compressed air enters the cylinder, it pushes the piston, causing it to move in a specific direction. This motion can be linear (back and forth) or rotary, depending on the actuator’s design.
The movement of the piston is controlled by valves that regulate the flow of compressed air. When air is directed into one side of the piston, it moves in one direction. When the air is released and directed to the other side, the piston moves back. Pneumatic actuators are quick, precise, and reliable, making them ideal for applications that require fast, repetitive motions.
Basics of Pneumatic Actuator Operation
Pneumatic actuators operate on the principle of using compressed air to produce motion. The basic structure of a pneumatic actuator includes a cylinder, a piston, and a set of valves to control the flow of compressed air. When air enters the actuator, it pushes against the piston, which then moves, performing the required mechanical task. The motion can be linear or rotary depending on the type of actuator. The movement’s speed and direction are controlled by valves, which regulate the amount of compressed air entering the system.
The pressure of the air within the cylinder is a critical factor in determining the force generated by the actuator. The actuator’s size, the cylinder’s diameter, and the air pressure determine how much force the actuator can generate. When the air is released from the cylinder, it can either return to the starting position or be redirected to perform a different function. This cycle can be repeated many times, providing efficient, continuous motion.
Pneumatic actuators are often preferred in environments where high-speed operation is essential, as they can produce rapid movements with minimal wear and tear. The ability to adjust air pressure and flow allows for fine control over the actuator’s movement, making it ideal for tasks requiring precision. Whether it’s used for lifting, pressing, or opening and closing mechanisms, pneumatic actuators provide an efficient and reliable means of converting compressed air into usable mechanical force.
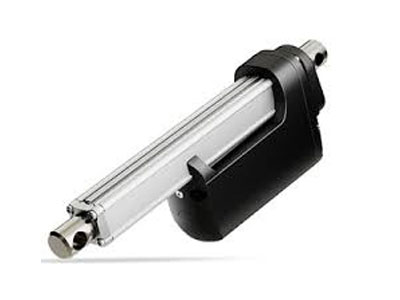
Role of Compressed Air in Pneumatic Actuators
Compressed air is the driving force behind pneumatic actuators, making it one of the most essential components of their operation. In pneumatic systems, air is compressed to a higher pressure than the surrounding environment, storing significant energy. This pressurized air is then directed into the actuator to drive motion. The role of compressed air in pneumatic actuators is crucial because it serves as the medium for transferring energy into mechanical movement.
When air enters the actuator, it fills the chamber behind the piston, creating pressure that pushes the piston in a specific direction. The amount of pressure and the size of the piston determine the force and speed of the actuator’s motion. Control valves regulate the flow of compressed air, allowing operators to control the direction, speed, and force of the actuator’s movement.
One of the key advantages of using compressed air is that it is widely available and can be produced by air compressors, which are common in industrial settings. Compressed air is also clean, non-toxic, and relatively inexpensive compared to other power sources, making pneumatic actuators a cost-effective and environmentally friendly solution. However, maintaining a consistent air supply and pressure regulation is essential to ensure optimal actuator performance, as fluctuations in pressure can lead to poor performance or equipment failure.
Components That Enable Actuator Movement
Several key components are essential for the smooth and efficient operation of a pneumatic actuator. These components work together to ensure that compressed air is effectively converted into motion to perform tasks across various applications. Understanding these components helps in maintaining and troubleshooting pneumatic actuators for optimal performance.
The cylinder is one of the most fundamental parts of a pneumatic actuator. It houses the piston, which moves when air is directed into the chamber. The cylinder’s inner walls are designed to keep the piston aligned while minimizing friction, ensuring smooth operation. The piston itself is a crucial component that moves back and forth inside the cylinder when compressed air is applied. The force generated by the piston is what drives the actuator’s movement.
Another important component is the valve system. The control valve regulates the flow of compressed air into the actuator, directing it to either side of the piston. This allows the actuator to extend or retract depending on which side of the piston the air is applied to. There are also check valves and directional control valves that ensure proper flow and prevent air from escaping or backflowing.
Air filters and regulators are also essential for maintaining the performance of pneumatic actuators. Filters clean the incoming air, preventing debris from entering the system, while regulators control the air pressure, ensuring the actuator receives consistent pressure for precise and reliable movement. Proper maintenance of these components is crucial for prolonging the life and performance of pneumatic actuators.
Step-by-Step Functioning of a Pneumatic Actuator
The operation of a pneumatic actuator follows a simple yet effective sequence of steps that convert compressed air into mechanical motion. Here’s a breakdown of the step-by-step functioning of a typical pneumatic actuator:
1. Air Compression and Supply: The process begins when compressed air is generated by an air compressor. The compressor increases the pressure of the air, which is then stored in air tanks or piping systems.
2. Air Flow Control: When the actuator needs to perform work, the air is directed into the actuator through a control valve. The control valve determines the direction and flow rate of the air, ensuring it reaches the actuator’s piston in a controlled manner.
3. Pressure Application: The compressed air enters the actuator chamber, applying pressure to one side of the piston. This pressure causes the piston to move, either extending or retracting, depending on the desired motion.
4. Motion Generation: As the piston moves, it drives the mechanical part connected to it. This movement can be linear, like pushing or pulling, or rotary if the actuator is designed for rotational motion.
5. Exhausting Air: Once the piston has completed its movement, the air is exhausted through the opposite side of the piston or through a vent. The exhaust air is directed back into the atmosphere or filtered if necessary.
6. Cycle Repeats: The cycle repeats every time the actuator is engaged. The control system continuously regulates the flow of compressed air to ensure that the actuator’s movement is precise, controlled, and timely.
Troubleshooting Common Issues in Pneumatic Actuators
While pneumatic actuators are highly reliable, they can experience issues that affect their performance. Identifying and troubleshooting these problems early can prevent costly downtime and repairs. Here are some common issues and how to address them:
1. Insufficient Movement or No Movement: One of the most common issues is when the actuator does not move or does not move as expected. This can occur if there is insufficient air pressure or air supply. Check the air compressor and ensure that the system is supplying the correct pressure. Additionally, check for leaks in the piping or hoses, as this can cause a loss of pressure.
2. Slow Movement: If the actuator moves slowly, it may be due to a clogged air filter, which restricts airflow, or a faulty pressure regulator that isn’t allowing enough air to flow into the actuator. Regularly inspect the filters and regulators and replace them as needed. Also, check the valve system to ensure it is functioning correctly.
3. Uneven or Jerky Movement: This could be a result of damaged seals or friction inside the cylinder. Inspect the piston seals and replace them if they appear worn. Also, ensure that the cylinder is properly aligned and lubricated.
4. Excessive Noise: Unusual noise during operation could be a sign of air leaks or a misaligned piston. Conduct a visual inspection of the actuator and its components to identify any sources of noise. Ensure the actuator is operating within the manufacturer’s recommended parameters.
5. Failure to Return: If the actuator does not retract properly, check the control valve and ensure that it is properly directing air to both sides of the piston. A malfunctioning valve can prevent the actuator from returning to its original position.
Conclusion
In conclusion, the operation of a pneumatic actuator involves the conversion of compressed air into mechanical motion, which is utilized to perform various tasks. Pneumatic actuators are widely used in industries for their ability to provide reliable and efficient power transmission. By utilizing compressed air, these actuators can produce linear or rotary motion, depending on the application requirements.
The design of pneumatic actuators allows them to operate in diverse environments, offering durability and ease of maintenance. They are favored for their safety features and cost-effectiveness, making them a practical choice in automation and control systems. As technology evolves, pneumatic actuators continue to be an integral part of modern machinery, contributing to enhanced performance and operational efficiency.