Key Takeaway
Sizing a rotary actuator involves determining the required torque and speed for your application. This ensures that the actuator can handle the load and operate efficiently. Consider factors such as the weight of the load, the speed of rotation, and the operating environment.
By calculating these factors, you can select an actuator that meets your needs, ensuring optimal performance and reliability. Proper sizing is crucial for preventing overloading and extending the life of the actuator.
Importance of Proper Sizing in Rotary Actuators
Proper sizing of rotary actuators is essential to ensure that they can generate the required torque and achieve the desired rotation in an application. Sizing involves selecting an actuator that matches the required specifications, such as the amount of torque needed, the angle of rotation, and the available space. Incorrect sizing can lead to underperformance or overloading, which may cause premature wear, inefficiency, or failure.
When selecting the appropriate rotary actuator, it is important to consider factors such as the pressure and flow rate of the pneumatic system, the weight of the components being moved, and the required speed and precision of the motion. A well-sized actuator will ensure that the system operates smoothly, efficiently, and within the expected parameters, providing optimal performance and reducing the risk of mechanical issues.
Furthermore, proper sizing can also improve energy efficiency. When an actuator is oversized for the task, it may consume more compressed air than necessary, increasing operating costs and reducing overall system efficiency. By accurately calculating the required torque and selecting the appropriate actuator size, operators can optimize system performance, reduce energy consumption, and extend the lifespan of the actuator and other components.
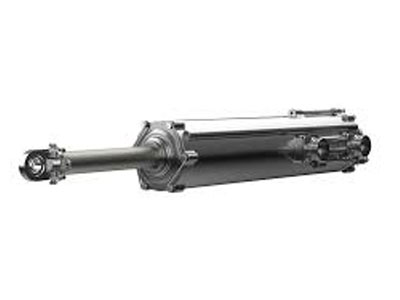
Key Parameters to Consider (Torque, Pressure, etc.)
Several key parameters must be considered when sizing a rotary actuator to ensure that it meets the performance requirements of the application. The most critical factors include torque, pressure, and the required range of motion.
Torque is one of the most important parameters when sizing a rotary actuator. It refers to the amount of rotational force that the actuator can generate. The required torque depends on the load the actuator will move and the application’s mechanical demands. If the torque is underestimated, the actuator may fail to perform the necessary task effectively. On the other hand, overestimating the torque can lead to inefficient operation, as the actuator will be unnecessarily oversized, wasting energy.
Pressure plays a vital role in the performance of the actuator. The pressure of the fluid (typically compressed air) supplied to the actuator influences the torque and speed of rotation. Higher pressure can generate more torque, but it also requires stronger seals and more durable components to handle the increased forces. Therefore, knowing the operating pressure of the system is crucial for sizing the actuator properly.
Additionally, range of motion is another important consideration. The actuator must be able to provide the desired rotation angle to perform the required tasks. This is typically specified in degrees of rotation (e.g., 90°, 180°), and the actuator’s size and internal design should allow for this range without risking damage to the system or other components.
You May Like to Read
Steps to Accurately Size an Actuator
To accurately size a rotary actuator, follow these essential steps:
1. Identify the Application Requirements: The first step is to understand the specific requirements of your application. This includes the load the actuator will move, the required speed, and the range of motion. It is important to gather as much information as possible about the task at hand.
2. Determine the Required Torque: Based on the load and required motion, calculate the amount of torque needed. Torque is usually calculated using the formula:
This will help determine whether the actuator has the necessary power to rotate the load efficiently.
3. Check the Operating Pressure: Ensure that the actuator can handle the pressure available in your system. The pressure will affect the actuator’s performance, so knowing the system’s pressure capacity is essential to selecting an actuator that can perform optimally.
4. Account for Speed and Cycle Time: Determine the required speed of the actuator. Speed depends on how fast you need the actuator to complete its motion. If speed is a critical factor, ensure that the actuator you select can handle the required cycle time without overheating or damaging the system.
5. Consider Environmental Conditions: Take into account any environmental conditions that may affect the actuator, such as temperature extremes, moisture, or exposure to harsh chemicals. These factors will influence the choice of actuator material and its durability.
By carefully following these steps and considering the key factors, you can accurately size the rotary actuator to ensure optimal performance and efficiency.
Common Mistakes and How to Avoid Them
When sizing a rotary actuator, there are a few common mistakes that engineers may make, which can lead to inefficient operation or failure of the system. Avoiding these mistakes can help ensure that the actuator performs as expected.
1. Underestimating the Required Torque: One of the most common mistakes is underestimating the torque needed for the application. This can lead to the actuator struggling to perform its task, or even damaging components in the system. Always err on the side of caution by overestimating the torque required to ensure the actuator can handle the load.
2. Overlooking Environmental Factors: Environmental conditions such as temperature, moisture, and dust can have a significant impact on actuator performance. Not accounting for these factors when selecting an actuator can result in premature failure. Always consider the environment in which the actuator will operate and choose one that can withstand these conditions.
3. Ignoring Maintenance and Duty Cycle: Failing to consider the actuator’s duty cycle or neglecting its maintenance needs can cause it to fail prematurely. Ensure that the actuator is designed to handle the specific operational demands of your system, including how often it will operate and for how long.
4. Not Considering the Pressure and Speed Requirements Together: Some engineers focus only on pressure or speed individually, but both play an essential role in actuator sizing. Overlooking how pressure and speed interact can result in an actuator that either lacks power or moves too slowly for the task.
By avoiding these mistakes and carefully considering each factor, you can size the actuator correctly and ensure reliable and efficient operation.
Tools and Software for Actuator Sizing
To make the process of sizing a rotary actuator more accurate and efficient, there are various tools and software available. These tools help engineers quickly calculate the required torque, pressure, and other parameters based on specific inputs.
Actuator Sizing Software: Many manufacturers provide actuator sizing software that allows users to input data such as load requirements, pressure, speed, and environmental conditions. The software then generates recommendations for actuator size and model based on the provided parameters. This can save time and reduce the risk of errors during manual calculations.
Torque Calculation Tools: For more precise torque calculations, many online tools and calculators are available. These tools enable engineers to input details such as the load weight, radius, and pressure to calculate the necessary torque for the actuator.
Simulation and Modeling Software: For more complex systems, simulation software can model how an actuator will perform under various conditions. This type of software is especially useful for high-precision applications where performance must be fine-tuned.
By utilizing these tools and software, engineers can ensure they make well-informed decisions when sizing rotary actuators.
Conclusion
Sizing a rotary actuator involves calculating the required torque and speed for specific applications, ensuring optimal performance and efficiency. Understanding the sizing process is crucial for selecting the right actuator.
By considering factors such as load, environment, and system requirements, users can effectively size rotary actuators for their systems, enhancing productivity and reliability.