Key Takeaway
Choosing a flow control valve involves considering factors such as the type of fluid or gas, operating conditions, flow rate, and pressure requirements. It is essential to select a valve that meets the system’s specifications and provides reliable flow regulation.
Consulting with manufacturers or industry experts can help ensure the right valve is chosen for the application. Factors such as valve design, material compatibility, and maintenance requirements should also be considered to ensure optimal performance and longevity of the system.
Factors to Consider When Choosing a Flow Control Valve
Choosing a flow control valve involves considering factors such as fluid type, flow rate, pressure, and temperature. These factors determine the valve’s suitability for specific applications.
Understanding the system requirements and operating conditions is crucial for selecting the right flow control valve. Proper selection ensures efficient operation and prevents potential issues such as overpressure or inadequate flow.
Advanced flow control valves often include features such as flow monitoring and automatic adjustment capabilities. These features enable precise control of flow distribution and help optimize system efficiency.
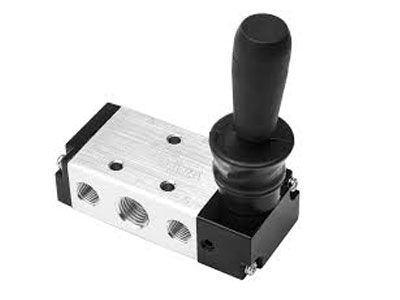
Key Features and Benefits
Flow control valves (FCVs) provide precise flow regulation, enabling efficient system operation. This precision reduces wear and tear on equipment and minimizes maintenance requirements.
Their ability to prevent pressure surges ensures the safety and longevity of connected components, making them indispensable in high-stress environments. FCVs also contribute to energy savings, as they regulate flow to avoid excess energy consumption.
These valves are widely used in industries like manufacturing, water treatment, and power generation for their reliability, durability, and efficiency.
Applications in Various Systems
Flow control valves (FCVs) are used in a wide range of industrial and commercial systems to regulate the flow of liquids, gases, and steam, ensuring smooth operations and protecting the integrity of the system.
1. Chemical Processing: In chemical manufacturing plants, FCVs help control the flow of various raw materials, ensuring precise and continuous production processes. This regulation prevents the overfeeding or underfeeding of chemicals into reactors, maintaining desired chemical reactions and ensuring the safety of the system.
2. Food and Beverage Industry: FCVs play an essential role in controlling the flow of ingredients during food production processes. Whether it is controlling the flow of liquids like milk or oils or regulating steam in cooking processes, FCVs ensure consistency and quality in food and beverage products.
3. Petrochemical Industry: FCVs are used in refining processes to regulate the flow of chemicals, gases, and crude oil through distillation columns, reactors, and other processing equipment. Precise flow control helps maintain operational efficiency and safety, particularly in high-pressure and hazardous conditions.
Advantages and Disadvantages
Flow control valves (FCVs) provide several advantages in maintaining optimal performance across various fluid systems. They are designed to precisely regulate flow rates, ensuring systems operate at peak efficiency, preventing energy waste, improving product quality, and extending the lifespan of system components. This capability is crucial in industries like water treatment, HVAC systems, and chemical processing, where consistent flow is essential for system stability. FCVs are adaptable to varying flow conditions, responding effectively to changes in system demands, which makes them highly versatile. Furthermore, FCVs prevent flow surges and excessive pressure buildup, thereby protecting downstream components, reducing the risk of mechanical failures, and enhancing system safety.
However, FCVs also have some disadvantages. Over time, their internal components, such as the valve stem or diaphragm, can experience wear and tear, particularly in systems with high-flow or abrasive fluids. This can lead to leaks, reduced performance, or valve failure, requiring regular maintenance to mitigate these issues. Additionally, high-quality FCVs designed for heavy-duty applications often come with a significant initial investment, making them less accessible for smaller operations. In some cases, the cost of advanced models may outweigh the benefits, particularly for low-demand applications. Furthermore, improper installation or calibration can lead to inefficiency or system failure, necessitating skilled professionals for installation and ongoing adjustments.
In conclusion, while FCVs offer numerous benefits such as efficiency, protection, and versatility, they require proper installation, regular maintenance, and a careful selection process to ensure their advantages outweigh the potential drawbacks. Proper handling and monitoring are crucial to ensuring these valves operate optimally and provide long-term value in various industrial systems.
Making the Right Choice for Your Needs
(FCV), it’s crucial to thoroughly assess the specific needs of the system. Key factors include the type of fluid (liquid, gas, or steam), operating pressure, temperature range, and flow rate requirements. These characteristics directly impact the valve’s material, design, and functionality.
Choosing the appropriate valve type—whether it’s a globe, ball, or butterfly valve—depends on the required precision of flow control. For applications requiring fine flow regulation, globe valves are ideal, whereas ball valves may be better for larger flow rates. Additionally, FCVs should be sized according to the system’s flow capacity to avoid issues such as cavitation or excessive pressure loss.
Maintenance and serviceability also factor into the decision. Consider valves that are easy to maintain and have readily available replacement parts. Ensuring that the valve meets industry standards and certifications (such as ASME or API) also guarantees safety and compliance with regulations, minimizing the risk of operational failures.
Conclusion
Choosing a flow control valve involves considering factors such as fluid type, flow rate, pressure, and system requirements. Understanding the specific needs of the application is crucial for selecting the right valve.
Consulting with manufacturers and reviewing technical specifications can help ensure the chosen valve meets the system’s requirements. Proper selection ensures efficient operation, reduces energy consumption, and prevents potential issues such as overpressure or inadequate flow.