Key Takeaway
Variable Frequency Drives (VFDs) save energy by precisely adjusting the speed of electric motors to match the specific needs of the application. This ability to control motor speed ensures that energy is used efficiently, reducing overall electricity consumption. By operating motors at optimal speeds rather than running constantly at full capacity, VFDs prevent energy wastage and lower operational costs significantly. Additionally, VFDs improve the power factor of electrical systems, further enhancing energy efficiency. Overall, integrating VFDs into industrial processes not only saves energy but also contributes to sustainability efforts by minimizing carbon footprint and operational expenses.
Mechanisms of Energy Savings in VFDs
The primary mechanism by which VFDs save energy is through precise control of motor speed and torque. Traditional motors run at full speed regardless of the actual demand, leading to energy wastage. In contrast, VFDs adjust the motor speed to match the specific requirements of the application. For instance, in HVAC systems, pumps, and fans, the power required is proportional to the cube of the speed. Hence, reducing the motor speed by 20% can lead to nearly 50% energy savings. Additionally, VFDs minimize mechanical stress, leading to less maintenance and longer equipment life, contributing to overall energy efficiency.
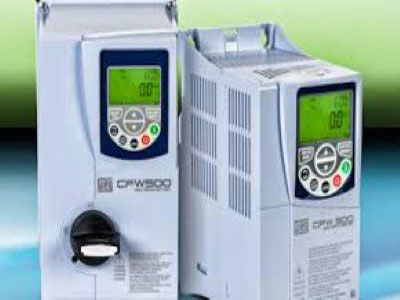
Practical Examples of Energy Savings
Consider a factory with multiple conveyor belts running on fixed-speed motors. These motors consume a constant amount of electricity regardless of the load on the belts. By integrating Variable Frequency Drives (VFDs), the speed of each motor can be adjusted according to the load, significantly reducing energy consumption during low-demand periods. For instance, during off-peak hours, when the conveyor belts carry fewer products, the motors can run at a lower speed, using less energy.
Another example is in water treatment plants where pumps run continuously. VFDs can regulate the pump speed based on the water flow demand, resulting in substantial energy savings. Instead of running at full speed all the time, the pumps can slow down when the water demand is low, which saves electricity and reduces wear and tear on the equipment.
These practical applications show how VFDs can lead to immediate and noticeable reductions in energy use. By optimizing motor speeds according to real-time needs, VFDs not only cut energy costs but also enhance the overall efficiency and lifespan of industrial equipment. This makes them an essential tool for modern industrial operations.
You May Like to Read
Case Studies: Energy Efficiency Achieved with VFDs
Energy Efficiency in Textile Manufacturing
In the textile industry, energy efficiency is a critical concern due to high operational costs. A prime example is a textile manufacturing plant that implemented Variable Frequency Drives (VFDs) on its spinning machines. This move resulted in a remarkable 30% reduction in energy consumption. Not only did this decrease energy usage, but it also significantly lowered production costs. The plant’s management reported a rapid return on investment, showcasing the financial viability of VFDs. This case highlights the potential of VFDs to transform energy consumption patterns in energy-intensive industries like textiles.
HVAC Systems in Commercial Buildings
Another compelling case is a large commercial building that incorporated VFDs into its HVAC system. The installation of VFDs led to a 20% reduction in the building’s annual energy bill. This substantial saving underscores the financial benefits of using VFDs in managing energy consumption in large facilities. Moreover, the building’s management observed improved climate control and reduced wear and tear on HVAC components, extending their operational life. These advantages illustrate how VFDs can be a game-changer in enhancing energy efficiency and operational sustainability in commercial buildings.
Calculating Energy Savings with VFDs
Understanding energy savings with Variable Frequency Drives (VFDs) is crucial. VFDs help in reducing the energy consumption of motors by controlling their speed. The basic formula to calculate energy savings is: Energy Savings (%) = [(Speed Reduction %)³ x 100]. For instance, if a motor’s speed is reduced by 20%, the energy savings can be around 50%.
To accurately estimate these savings, you need to consider factors like the motor’s operating hours, load profile, and efficiency. VFD manufacturers provide tools and software to assist in this. By inputting parameters such as motor size, duty cycle, and operational hours, these tools offer a detailed analysis of potential savings.
Imagine a scenario where a motor runs at full speed continuously. By using a VFD to adjust the speed according to the load demand, significant energy savings can be achieved. This not only reduces operational costs but also extends the motor’s lifespan due to less wear and tear.
Remember, the key to maximizing savings is proper VFD programming and regular maintenance. Stay updated with the latest tools provided by manufacturers to ensure you’re leveraging the full potential of VFDs in your applications. This approach will make your operations more energy-efficient and cost-effective.
Tips for Maximizing Energy Savings
To maximize energy savings with Variable Frequency Drives (VFDs), it’s important to start with a thorough analysis of the motor’s operating conditions and load profile. This analysis helps in understanding the exact energy requirements and identifying areas where energy can be saved. Regular maintenance of VFDs is another critical aspect. Ensuring that the VFDs are clean, free from dust, and properly calibrated can prevent energy losses due to inefficiencies.
Properly sizing the VFD to match the motor’s requirements is essential. An oversized or undersized VFD can lead to energy wastage. Utilize energy-saving modes and features provided by the VFD, such as sleep mode, which can turn off the motor during periods of inactivity, and automatic tuning, which adjusts the VFD settings to match the load conditions accurately. These features are designed to enhance energy savings and operational efficiency.
Training personnel on the proper use and benefits of VFDs can also lead to significant energy savings. Educated staff can make informed decisions, ensuring that the VFDs are used optimally. This not only maximizes energy efficiency but also prolongs the lifespan of the equipment.
Conclusion
VFDs hold immense potential for energy savings in industrial applications. By precisely controlling motor speed and torque, they optimize energy use and reduce wastage. The practical examples and case studies presented demonstrate the substantial benefits that VFDs can bring. Accurate calculation of energy savings and implementing best practices can further enhance these benefits. As industries continue to seek ways to reduce energy consumption and costs, VFDs emerge as a reliable and efficient solution. Embracing this technology not only contributes to a greener planet but also leads to significant financial savings, making VFDs a smart investment for the future.