Key Takeaway
You can’t use just any servo drive for any motor. Compatibility between the servo drive and motor is crucial to ensure proper operation. The servo drive must match the motor’s voltage, current, and power ratings. If these parameters are not aligned, the motor may not perform correctly, leading to potential damage or inefficiency.
Additionally, the feedback system plays a critical role. The servo drive must be compatible with the motor’s encoder or resolver to provide accurate control. Mismatched feedback systems can cause poor performance or even failure. Always check the specifications and ensure that both the servo drive and motor are designed to work together for optimal performance.
Understanding Compatibility Between Servo Drives and Motors
Compatibility between a servo drive and a motor is determined by several factors, including electrical characteristics, mechanical design, and control capabilities. The drive must be able to provide the appropriate voltage and current to the motor without overloading it. Additionally, the drive’s control system must be capable of interpreting the motor’s feedback signals, whether it’s through an encoder, resolver, or other feedback mechanisms. Without this compatibility, the motor may not respond accurately to commands, leading to erratic behavior, reduced efficiency, and potential system failure.
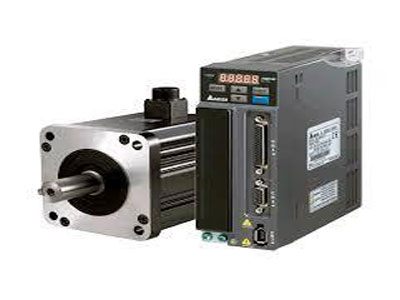
Understanding Compatibility Between Servo Drives and Motors
Compatibility between servo drives and motors is the cornerstone of efficient operation in automated systems. The primary factor to consider is whether the drive can handle the motor’s specific voltage, current, and power requirements. For example, if a servo drive is designed for low-voltage applications, attempting to pair it with a high-voltage motor can lead to catastrophic failure, such as burning out components or triggering safety shutdowns. On the other hand, if the drive provides more power than the motor can handle, this could result in overheating, inefficiency, and premature wear on the motor. It’s essential to check the drive’s specifications against the motor’s needs before proceeding. This matching process ensures that both components work harmoniously, maximizing performance and extending the lifespan of your equipment. Additionally, it is vital to consider the operational environment—ambient temperature, humidity, and potential exposure to contaminants—because these factors can affect both the drive and motor’s performance, adding another layer to the compatibility equation.
Electrical and Mechanical Considerations
Beyond just electrical compatibility, mechanical factors also play a critical role in ensuring that a servo drive and motor pair successfully. Electrically, the drive’s output must align with the motor’s input, not just in voltage and current but also in terms of frequency. For instance, if the drive operates at a frequency that the motor isn’t designed to handle, it can lead to inefficient operation, increased wear, or even mechanical failure. Mechanically, the motor and drive must be compatible in terms of physical connection points, such as shaft size, mounting configurations, and feedback devices like encoders or resolvers. A mismatch in shaft size, for example, can cause poor transmission of power, leading to vibrations, misalignment, and eventual breakdown of components. Additionally, if the feedback system is not compatible, the drive may not be able to accurately control the motor, resulting in performance issues or a complete lack of functionality. Ensuring that both the electrical and mechanical aspects are fully compatible requires thorough checking of technical specifications and, when possible, consulting with both drive and motor manufacturers for guidance.
These considerations are not merely academic; they have practical implications in every application. Whether it’s in a high-precision robotics system or an industrial CNC machine, ensuring that the servo drive and motor are perfectly matched electrically and mechanically is key to achieving the desired performance, reliability, and longevity of the equipment.
Common Mistakes When Pairing Servo Drives with Motors
One of the most frequent mistakes when pairing servo drives with motors is the failure to properly match power requirements. Users sometimes choose a servo drive based on factors like brand reputation or cost, neglecting to ensure that the drive’s power output matches the motor’s needs. This mismatch can lead to underperformance or, in worse cases, damage to both the drive and the motor. Another common oversight is ignoring the compatibility of the feedback system.
The feedback system is crucial for the accurate operation of a servo motor, as it allows the drive to adjust the motor’s position, speed, and torque in real time. If the drive and motor do not have compatible feedback systems, it can result in erratic motor behavior, loss of precision, or even failure to operate. Mechanical mismatches, such as incorrect shaft sizes, improper mounting configurations, or incompatible connectors, are also common. These issues can lead to difficulties during installation, increased wear and tear, and inefficiencies in operation. To avoid these problems, it’s essential to thoroughly check and verify that both the drive and motor are compatible in every aspect before finalizing your selection.
Best Practices for Ensuring Compatibility
To ensure a successful pairing between servo drives and motors, adhering to best practices is crucial. The first step is to meticulously verify that the electrical specifications of the servo drive align with those of the motor. This includes matching voltage, current, and power ratings to ensure that the drive can adequately power the motor without causing any strain or inefficiencies. Additionally, mechanical compatibility must be confirmed by checking that the drive can physically connect to the motor. This involves verifying that the shaft sizes match, the mounting holes align, and the connectors are compatible. Another key practice is to ensure that the feedback systems are synchronized.
The feedback loop is vital for the precise control of the motor, so the drive and motor must be able to communicate effectively to maintain accurate operation. It’s highly recommended to consult with manufacturers or technical experts during the selection process, as they can provide insights into the most suitable combinations of drives and motors. Finally, before deploying the system on a large scale, it’s wise to conduct thorough testing under real-world operating conditions. This helps identify any potential issues early on, allowing for adjustments or replacements before the system is fully operational. By following these best practices, you can ensure that your servo drive and motor work together harmoniously, providing reliable and efficient performance.
Conclusion
Ensuring that your servo drive and motor are compatible is not just about matching specifications—it’s about creating a system that performs efficiently and reliably. By understanding the importance of electrical, mechanical, and feedback compatibility, and by avoiding common mistakes, you can achieve optimal performance from your servo system. Investing the time to carefully select and pair your servo drive and motor will pay off in the long run with a smoother, more reliable operation that meets the demands of your application.