Key Takeaway
The pressure for pneumatic actuators typically ranges between 60 to 120 psi (pounds per square inch), though it can vary depending on the application. Higher pressure results in more force, allowing the actuator to perform heavy-duty tasks.
The exact pressure needed depends on factors like the actuator size and the task at hand. Pneumatic actuators are designed to handle specific pressure levels to ensure efficiency, safety, and reliability in applications such as manufacturing, automation, and robotics.
Standard Operating Pressure Ranges
Pneumatic actuators rely on compressed air to generate motion, and the operating pressure plays a crucial role in determining their performance. Typically, the standard operating pressure for pneumatic actuators ranges from 60 psi to 120 psi (pounds per square inch), depending on the specific application and the type of actuator. This range allows the actuator to generate sufficient force while maintaining efficiency and preventing system damage.
The pressure in a pneumatic system is closely tied to the size of the actuator and the force required for the application. For instance, smaller actuators used in light-duty applications like pick-and-place robots might function well at lower pressures (around 60-80 psi), while larger actuators in industrial machinery or high-force operations may require pressures closer to the higher end of the spectrum (100-120 psi).
It’s important to understand the pressure rating of both the actuator and the air supply system, as exceeding the maximum pressure can lead to overstressing components, while insufficient pressure may result in poor actuator performance and unreliable operation. Maintaining the proper pressure is critical to ensuring that the actuator operates within its designed capacity and performs efficiently throughout its lifespan.
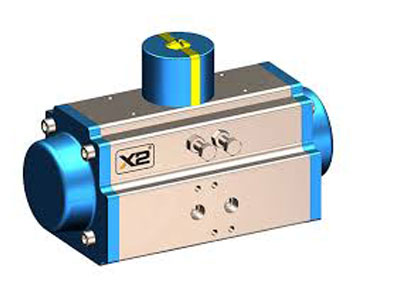
Impact of Low and High Pressure on Performance
The pressure levels within a pneumatic actuator system significantly affect its performance. Low pressure can result in reduced force output, slower movement, and less precision in the actuator’s motion. When the pressure is too low, the actuator may fail to perform tasks efficiently, causing delays in production lines, manufacturing processes, or automated tasks. In applications where high-speed operation or precise movement is essential, low pressure can compromise the system’s performance.
On the other hand, high pressure can provide more force, but it may also lead to potential issues. While higher pressure can increase the actuator’s speed and force output, it can cause additional strain on the components and increase the risk of leakage or mechanical failure. Over-pressurization can result in overheating, wear and tear on seals, and in extreme cases, damage to the actuator or compressed air lines.
To optimize actuator performance and ensure a longer service life, it’s important to find the right balance between too low and too high pressure. Pressure regulation devices like pressure regulators are essential in maintaining this balance. These devices help adjust and stabilize the pressure within a defined range to suit the application’s needs.
Pressure Adjustment for Specific Applications
Adjusting pressure in pneumatic actuator systems is critical for matching performance to specific application requirements. Different processes or machinery demand varying levels of force and speed, which can be achieved by adjusting the air pressure delivered to the actuator. By modifying the pressure, operators can fine-tune actuator response to optimize performance and enhance efficiency.
For example, in light-duty automation, such as packaging systems or sorting machines, lower pressure might be ideal for maintaining smooth, consistent motion without stressing the system. Medium-duty applications, such as conveyor belts or robotic arms, may require a balance of pressure to ensure quick yet controlled movement. For heavy-duty applications like pressing machines or hydraulic-like tasks, higher pressure is often necessary to generate the necessary force.
In some cases, pressure can be varied dynamically to suit different stages of the operation. This is common in systems that require variable speed control, such as in assembly lines where parts must be moved at different speeds based on the task. Operators use variable flow regulators or pressure relief valves to control the amount of pressure based on the specific phase of operation.
For safety and efficiency, it is also critical to match the pressure settings with the capacity of both the actuator and the pneumatic system. Overpressurization or underpressurization can reduce actuator life and increase energy consumption.
Safety Considerations in Pressure Management
Pressure management in pneumatic systems is a critical factor in ensuring both safety and optimal performance. Because compressed air is powerful and potentially hazardous, maintaining appropriate pressure is vital to prevent accidents such as blowouts, explosions, or system failures. These safety risks are typically the result of excessive pressure, but low pressure also poses its own operational challenges.
To avoid these risks, pressure relief valves and pressure regulators should always be installed in pneumatic systems. Relief valves automatically open when the pressure exceeds a preset threshold, preventing the system from reaching dangerous levels. Pressure regulators are used to ensure that air pressure remains within the optimal range required for the actuator, ensuring consistent performance while safeguarding the system from the risks of over-pressurization.
It’s also essential to inspect pneumatic systems regularly for signs of damage or wear, such as leaking hoses, cracks in cylinders, or broken seals, all of which can affect the overall pressure regulation. A preventative maintenance schedule should include checking the entire air supply system, including the compressor, filters, and hoses, for leaks or blockages that could affect air pressure.
In addition, personnel working with pneumatic systems should be well-trained in safety protocols, particularly regarding pressure management. Using the correct personal protective equipment (PPE) is also important when maintaining or servicing pressurized pneumatic systems.
By implementing these safety measures, you ensure both safe and efficient operation of pneumatic actuators, safeguarding both equipment and personnel.
Compatibility with Compressed Air Systems
For pneumatic actuators to function correctly, they must be integrated into a compatible compressed air system. The air supply system must deliver air at the required pressure levels, in a clean and dry state, for the actuator to perform optimally. Compatibility between the actuator and the air system is crucial for ensuring reliable operation and minimizing wear on the system components.
Compressed air systems include compressors, filters, regulators, and hoses, all of which must be matched to the actuator’s requirements. The air must be free of contaminants such as oil, water, and dust, which could damage the actuator and reduce its efficiency. Air filters and dryers are often employed in pneumatic systems to ensure that the air entering the actuator is clean and moisture-free.
Pressure regulators are used to adjust and maintain the correct air pressure, and they ensure that the actuator receives a consistent supply of air at the pressure needed for optimal performance. If the air pressure fluctuates too much, it can lead to inconsistent actuator movement, causing delays and inefficient operation.
It’s also essential that the hoses and fittings used in the system are compatible with the required pressure levels. The wrong type of hose or a loose fitting could cause leaks or reduce the system’s overall efficiency.
In summary, ensuring that the pneumatic actuator is properly integrated into a compatible compressed air system is key to maximizing performance, safety, and lifespan. By choosing the right components and ensuring compatibility, companies can keep operations running smoothly and prevent unnecessary downtime.
Conclusion
In conclusion, the pressure for pneumatic actuators is a critical factor that determines their performance and efficiency. It is essential to maintain the appropriate pressure levels to ensure optimal operation and prevent potential damage to the system. Typically, pneumatic actuators operate within a range of pressures that can be adjusted based on the specific requirements of the application.
Moreover, the ability to control and regulate pressure allows for precise actuator movements, enhancing the reliability and accuracy of automated processes. As industrial applications demand increasingly sophisticated automation solutions, maintaining the correct pressure levels in pneumatic actuators becomes paramount in achieving desired outcomes and maximizing operational efficiency.