Key Takeaway
The principle of pneumatic actuators is based on using compressed air to create movement. When air enters the actuator, it presses against a piston or diaphragm inside. This pressure causes the piston to move, generating linear or rotary motion.
Pneumatic actuators are controlled by valves that regulate the flow of air. When the air is directed into the actuator, it creates force that drives mechanical systems, such as lifting, pushing, or rotating. The key advantage of pneumatic actuators is their simplicity, speed, and ability to handle heavy loads efficiently, making them widely used in industries like manufacturing and automation.
Role of Compressed Air in Pneumatic Actuators
Compressed air is the driving force behind pneumatic actuators, which convert the stored air pressure into mechanical motion. When compressed air is introduced into the actuator, it pushes a piston or diaphragm, creating linear or rotary motion, depending on the actuator’s design. The pressure of the air determines the force and speed of the motion, allowing the actuator to perform a wide range of tasks, from moving valves to powering robotic arms.
The versatility of compressed air allows pneumatic actuators to generate varying levels of force, from light movements for delicate tasks to heavy-duty actions like lifting or pressing. Because compressed air is readily available and relatively inexpensive, it makes pneumatic actuators an economical choice for many industries. Additionally, compressed air systems are often easier to maintain and more durable than hydraulic or electric systems, further enhancing their appeal.
In essence, compressed air acts as both the power source and the medium that controls the movement within pneumatic actuators. Its ability to be easily stored, controlled, and distributed makes it an ideal energy source for a wide range of industrial applications.
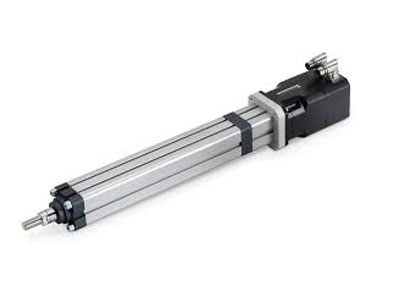
Energy Conversion from Air Pressure to Motion
The core principle behind pneumatic actuators is the conversion of air pressure into mechanical motion. This energy conversion process is simple yet powerful, making pneumatic actuators ideal for a wide range of applications in industries such as automation, manufacturing, and robotics.
When compressed air enters the actuator, it exerts pressure on a piston or diaphragm. As the air pushes against these surfaces, the actuator starts to move, converting the stored energy in the compressed air into linear or rotational motion. The force generated by the air is determined by two main factors: the air pressure and the surface area of the piston or diaphragm. Higher air pressure results in greater force, and a larger surface area amplifies the force exerted on the actuator.
This energy conversion allows the pneumatic actuator to perform various tasks, such as lifting, pushing, or rotating objects with high precision and speed. In linear actuators, for instance, the piston moves back and forth inside a cylinder, allowing the actuator to push or pull objects along a straight path. In rotary actuators, the force generated by the compressed air is used to rotate a shaft or wheel, enabling rotational movement.
One of the most notable characteristics of pneumatic actuators is their ability to provide rapid motion and quick response times, which is essential in industries where speed and accuracy are critical. Furthermore, the simplicity of converting compressed air to motion with minimal friction or wear makes pneumatic actuators highly reliable and low-maintenance.
You May Like to Read
Components Involved in Pneumatic Actuation
Pneumatic actuators rely on several key components working in unison to convert compressed air into controlled mechanical motion. Understanding these components is essential to grasp how pneumatic actuators function efficiently and reliably.
1. Air Compressor: The air compressor is the first component in the pneumatic system. It compresses the surrounding air and stores it in a reservoir or tank. The compressor increases the air pressure, providing the necessary force to drive the actuator.
2. Reservoir (Air Tank): The air reservoir holds the compressed air and acts as a storage system to ensure a steady supply of air pressure for the actuator. It also helps maintain a consistent flow of air during operations, allowing for smooth and continuous motion.
3. Valves: Pneumatic systems use control valves to regulate the flow and direction of compressed air. These valves control when and where the air is released into the actuator, allowing for precise control of movement. For instance, a directional control valve may be used to direct air into the actuator in either direction, enabling forward or reverse motion.
4. Actuator (Cylinder or Motor): The core of the pneumatic system, the actuator converts the pressure from the compressed air into mechanical force and motion. In linear actuators, the force pushes a piston back and forth, creating linear motion. In rotary actuators, the force is used to rotate a shaft, producing rotary motion.
5. Filters and Regulators: Air filters remove contaminants from the compressed air, ensuring the system stays clean and free from debris that could damage the components. Pressure regulators control the air pressure to ensure the actuator receives the correct amount of pressure for optimal performance.
Together, these components work seamlessly to ensure the smooth operation of a pneumatic system, providing precise and reliable actuation for various industrial and commercial applications.
Controlling Force and Movement through Pneumatic Systems
The control of force and movement in pneumatic actuators is a key aspect of how they function in automation and industrial systems. Valves, pressure regulators, and feedback systems are used to precisely control the force generated by pneumatic actuators, ensuring that motion is accurately applied as needed.
1. Control Valves: Pneumatic systems rely heavily on control valves to direct the flow of compressed air to the actuator. These valves determine when and how air is released into the actuator. Directional control valves can be used to change the direction of the actuator’s motion, while flow control valves regulate the speed of the actuator’s movement. By controlling how much air enters the system and at what rate, valves enable fine-tuned control over the force and motion produced.
2. Pressure Regulators: The force generated by a pneumatic actuator is directly tied to the air pressure within the system. Pressure regulators are used to maintain a consistent pressure level within the system, ensuring that the actuator receives a steady and controlled amount of force. By adjusting the pressure, the regulator ensures that the actuator can perform the required task with the right amount of power, whether it’s lifting a heavy object or making precise adjustments.
3. Feedback Systems: Advanced pneumatic systems incorporate sensors and feedback mechanisms to monitor the actuator’s position and performance in real time. These sensors help detect if the actuator is moving at the correct speed or if it has reached the desired position. Feedback loops enable automatic adjustments to the system, ensuring the actuator performs with high precision and repeatability.
By controlling the flow of air, regulating the pressure, and using feedback systems, pneumatic actuators can perform tasks with remarkable accuracy and efficiency, making them ideal for applications requiring precise force and motion control.
Efficiency and Precision in Pneumatic Actuators
Pneumatic actuators are known for their efficiency and precision, making them ideal for applications where speed, accuracy, and reliability are critical. The key factors contributing to their efficiency and precision lie in the control of air pressure, component design, and system integration.
1. High-Speed Response: Pneumatic actuators provide rapid movement, making them highly efficient for tasks that require quick response times. Compressed air flows through the system rapidly, enabling actuators to reach their desired position almost instantly. This high-speed motion is especially useful in automated systems where time-sensitive operations need to be performed quickly and with minimal delay.
2. Precision Control: Pneumatic actuators can be equipped with advanced control systems, such as valves and pressure regulators, to ensure precise control over the actuator’s movements. The force exerted by the compressed air can be adjusted based on the system’s needs, allowing for accurate motion control. Flow control valves enable fine-tuned adjustments to the speed and direction of the actuator, ensuring that it performs actions with minimal deviation.
3. Minimal Friction and Wear: Pneumatic actuators often have fewer moving parts compared to mechanical actuators, which helps reduce friction and wear. This design leads to increased reliability and longer lifespan of the actuator. The absence of heavy components also reduces the overall strain on the system, making it more efficient in the long term.
4. Low Power Consumption: Pneumatic actuators are energy-efficient because they only require compressed air, which can be generated from readily available resources. The low power consumption makes pneumatic systems more environmentally friendly compared to systems powered by electricity or hydraulic fluid.
In conclusion, the efficiency and precision of pneumatic actuators make them a popular choice for industries that demand high-performance, cost-effective, and reliable systems.
Conclusion
In conclusion, the principle of pneumatic actuators revolves around converting compressed air energy into mechanical motion, allowing for controlled and efficient movement in various applications. This principle provides a reliable and cost-effective solution for automation processes, contributing to enhanced productivity and performance.
Furthermore, pneumatic actuators offer advantages such as simplicity, durability, and rapid response times, making them an ideal choice for tasks requiring precise and swift motion. As industries continue to adopt advanced automation technologies, the principle of pneumatic actuators remains a cornerstone of modern engineering, driving innovation and enabling the seamless integration of automated systems within diverse operational environments.