Key Takeaway
The maximum flow of a control valve is determined by its size, design, and operating conditions. It is essential to select a control valve with a flow capacity that meets the system’s requirements to ensure efficient operation.
Accurate determination of the maximum flow is crucial for preventing issues such as cavitation, excessive pressure drop, and inefficient operation. It helps ensure the control valve provides reliable flow regulation and complies with system specifications.
Understanding Maximum Flow Ratings
Maximum flow ratings define the highest flow rate a valve can handle safely. These ratings are critical for ensuring system safety and preventing equipment damage.
Determining maximum flow ratings involves considering system requirements, material properties, and safety margins. Accurate ratings ensure reliable valve performance under all conditions.
Regular testing and verification of flow ratings are essential for maintaining system safety. This includes periodic inspections and recalibration to ensure compliance with safety standards.
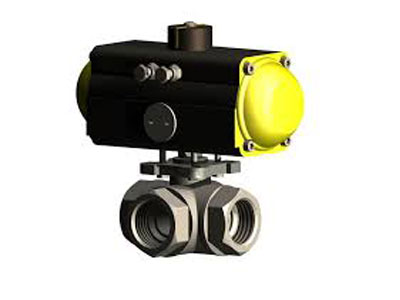
Factors Affecting Maximum Flow
The size and design of control valves significantly affect their maximum flow rates. Larger valves can handle greater flow volumes, while specialized designs improve flow efficiency.
The pressure differential across the valve impacts capacity; higher pressure drops can reduce the achievable flow rate. This is crucial in systems with varying pressure demands.
Additionally, fluid properties like viscosity and density influence flow. High-viscosity fluids require more energy to move through the valve, potentially lowering the flow rate. Proper valve selection ensures optimal performance and efficiency.
You May Like to Read
How to Determine Maximum Flow for Control Valves
Determining the maximum flow for a control valve is a critical process to ensure that the valve operates efficiently within the designed system parameters. The maximum flow rate is primarily determined by the size of the valve, the pressure differential across the valve, and the type of fluid being processed.
1. Valve Sizing: The valve’s size must match the system’s requirements. A larger valve can accommodate higher flow rates, while a smaller valve may restrict flow. The valve’s orifice size is one of the primary factors in determining the maximum flow, and this should be calculated based on the system’s specifications.
2. Pressure Differential: The pressure difference between the inlet and outlet of the valve plays a significant role in determining the maximum flow. A higher pressure differential typically leads to a higher flow rate, as the valve opens more to allow for fluid movement. Engineers can calculate the pressure drop across the valve to ensure it aligns with the desired flow characteristics.
3. Fluid Properties: The density, viscosity, and temperature of the fluid also impact the flow rate. For example, thicker fluids such as oils will flow more slowly than thinner fluids like water, requiring more force to move through the valve. Calculations also consider the fluid’s specific gravity and flow resistance to determine the maximum flow capacity.
Ensuring Compliance with Standards
Ensuring compliance with industry standards is vital when determining the maximum flow for control valves (CVs). Standards provide a structured approach to ensure that valves operate safely and efficiently within specified limits. One critical standard to follow is the ASME (American Society of Mechanical Engineers) Boiler and Pressure Vessel Code, which outlines the safety criteria for valves in pressure systems. This standard ensures that valves are designed and tested to handle extreme flow rates without causing failure or damage. Additionally, international standards such as the ISO (International Organization for Standardization) provide specific guidelines on the sizing and flow characteristics of control valves to ensure consistency and reliability.
In practical terms, complying with standards helps to prevent situations where a control valve might exceed its flow capacity, potentially causing damage to the system or unsafe operating conditions. Proper selection, testing, and documentation of the maximum flow allowed are part of these compliance processes. These protocols are necessary for both ensuring the safety of the system and achieving performance objectives. Valve manufacturers and engineers must regularly review these standards to stay current with the evolving technology and regulatory requirements that affect control valve systems.
Failing to adhere to these standards could result in legal liabilities or unsafe operations. Thus, having the correct certifications, documentation, and tests to verify maximum flow limits is crucial. When choosing a CV, the appropriate valve must be selected according to the pressure, temperature, and fluid characteristics outlined by the applicable standards. Compliance ensures both safety and long-term reliability, making it an essential step in every industrial application.
Common Challenges and Solutions
Control valves (CVs) are critical in maintaining proper flow and pressure regulation, but they can encounter several issues during operation. A common challenge is valve stiction, where the valve sticks in one position, preventing smooth operation. To address stiction, ensure that the valve and actuator are properly maintained, lubricated, and free from debris.
Another issue is wear and tear on valve components such as seals and diaphragms, leading to leaks and reduced performance. Regular inspection and replacement of worn parts are essential to maintaining the valve’s functionality. In some cases, recalibration may also be required to ensure the valve operates within its desired range.
Flow instability can be another challenge, especially in dynamic systems with fluctuating pressures. This can often be remedied by installing a valve with higher rangeability or employing control systems that automatically adjust valve positions to maintain stability and prevent excessive fluctuations in the system.
Conclusion
The maximum flow of a control valve refers to the flow capacity or the maximum flow rate that the valve can handle. It is determined by factors such as the valve size, design, and operating conditions.
Understanding the maximum flow capacity is essential for ensuring the control valve provides reliable flow regulation and complies with system requirements. Accurate determination of the maximum flow helps prevent overloading and ensures efficient operation.