Key Takeaway
VFDs can experience several common faults. Overheating is a major issue, often due to poor ventilation. Display problems can arise, making it hard to monitor performance. Motor control issues are frequent, affecting the operation. Communication errors between the VFD and the motor can disrupt processes. Power supply problems can lead to malfunction. Grounding issues can cause erratic behavior. Programming errors might result from incorrect settings. Motor bearing failures can also occur due to wear and tear. Electrical noise interference can affect signals, and faulty input/output components can lead to system failures. Understanding these faults helps in maintaining optimal VFD performance.
Overview of Typical VFD Faults
Variable Frequency Drives (VFDs) are pivotal in managing the speed of electrical motors, enhancing energy efficiency across various industries. However, they can encounter specific common faults that can disrupt operations. Overvoltage, undervoltage, overheating, and issues related to improper grounding are frequent culprits. Additionally, electrical faults such as short circuits or phase loss can also lead to unexpected downtime.
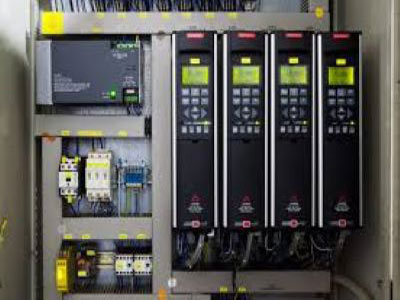
Diagnostic Techniques for Identifying Faults
Diagnosing VFD issues requires a systematic approach blending technical knowledge with practical skills. Start by examining the error codes displayed on the VFD panel; these codes offer initial clues about the problem. Error codes can indicate issues like overvoltage, undervoltage, or motor overload. Use multimeters and oscilloscopes to measure voltage and current levels, ensuring they align with the VFD’s specifications. If voltage or current levels are outside the expected range, it could point to wiring issues, faulty components, or incorrect settings.
Regular thermal imaging can detect overheating issues before they lead to failure, serving as an essential preventive tool. Overheating can be caused by excessive load, poor ventilation, or faulty cooling systems. A VFD expert will often use a combination of these diagnostic tools to pinpoint the exact cause of the problem.
Additionally, always check for any loose connections or damaged wiring, as these can cause intermittent faults that are hard to diagnose. Proper maintenance routines, including regular inspections and timely repairs, can prevent many common VFD issues. Ensuring that all components are clean and free of dust also helps maintain optimal performance.
You May Like to Read
Preventative Measures to Avoid Faults
When it comes to Variable Frequency Drives (VFDs), prevention truly is better than cure. Ensuring proper installation is crucial. Start with correct wiring and grounding techniques. This fundamental step can prevent many issues down the line.
Next, establish a regular maintenance schedule. This should include cleaning dust from cooling fans to maintain optimal airflow. Dust buildup can lead to overheating, which is a common cause of VFD failures. Also, routinely check all electrical connections for tightness. Loose connections can result in intermittent faults and operational errors, which can be tricky to diagnose.
Moreover, always verify that the VFD is not overloaded. Overloading can cause excessive wear and tear, leading to premature failure. Programming the VFD according to the motor’s precise requirements is another key step. This ensures the drive operates efficiently and prevents unnecessary strain on the system.
Remember, these practices not only extend the life of your VFD but also enhance overall system reliability. By adhering to these guidelines, you can avoid unexpected downtimes and costly repairs. Always aim for meticulousness in maintenance to keep your VFD running smoothly and efficiently. Your dedication to these preventative measures will pay off in the long run.
Case Studies of VFD Faults
In our manufacturing plant, we experienced frequent VFD (Variable Frequency Drive) failures, frustrating both the team and production schedules. After a detailed analysis, we discovered that the cooling fans were clogged with debris, leading to overheating. This was a crucial oversight. VFDs rely heavily on efficient cooling to function correctly, and blocked fans cause excessive heat buildup, leading to failures. Once we implemented a routine cleaning schedule for the cooling fans, the failure rate decreased significantly.
In another instance, we faced a VFD that frequently tripped due to overvoltage. This issue puzzled us initially, as the power supply was within the expected range. However, after examining the VFD settings, we realized they were not optimized for our specific power supply characteristics. By adjusting the settings to better match the power supply, the tripping incidents reduced drastically. This experience taught us the importance of regular maintenance and precise configuration of VFDs. Ensuring that cooling fans are clean and settings are correctly adjusted can prevent many common VFD issues. Remember, proactive maintenance and proper settings are key to reliable VFD operation.
Repair and Replacement Solutions
When diagnosing a VFD fault, the decision between repairing and replacing it hinges on several critical factors, including cost, age, and the likelihood of future failures. Let’s delve into these aspects.
Cost: Minor issues, like replacing a fan or capacitor, are generally cost-effective. These repairs can extend the VFD’s operational life significantly. For instance, a fan replacement is straightforward and relatively inexpensive, making it a practical choice when aiming to maintain system performance without incurring substantial costs.
Age: The age of the VFD plays a pivotal role. Older drives might frequently encounter problems, leading to higher maintenance costs over time. In such cases, even if the repair cost is lower, the recurring issues can disrupt operations and increase downtime, making replacement a more viable option.
Potential for Future Failures: If a VFD has sustained significant damage or is experiencing recurrent faults, it indicates underlying issues that might not be fully resolved through repairs. In such scenarios, investing in a new, more efficient model could be more economical in the long run. Newer models often come with advanced features, improved energy efficiency, and better reliability, reducing the risk of future failures.
Conclusion
Maintaining the reliability of VFDs is crucial for minimizing downtime and enhancing operational efficiency. By understanding common faults, applying thorough diagnostic techniques, and implementing preventative measures, you can significantly improve the lifespan and performance of your VFD systems. Remember, a well-maintained VFD not only saves time and money but also ensures the continuous productivity of your applications.