Key Takeaway
Yes, a VFD can convert AC to DC. Here’s how it works: the VFD first takes the incoming AC power and uses a rectifier to convert it into DC power. This process is crucial because DC power is more stable and easier to control. The rectifier ensures that only positive voltage passes through, effectively creating DC power from the AC input. After this conversion, the VFD then uses an inverter to convert the DC power back into a controlled AC output, which is used to control the speed and torque of the motor. This dual conversion process is key to the VFD’s functionality.
The Power Conversion Process in VFDs
The primary function of a VFD is to convert the fixed frequency AC power supply into a variable frequency and voltage to control motor speed. The first step in this process involves converting AC power to DC. This conversion is crucial because it allows the VFD to generate a variable frequency output. The conversion process starts with the input AC power passing through a rectifier, which converts AC to DC. This DC power is then filtered and stored in DC link capacitors. The next stage involves converting this DC power back to AC with variable frequency and voltage using an inverter. This entire process is essential for achieving precise control over motor speed and efficiency.
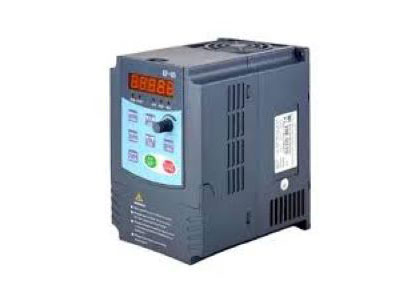
Role of Rectifiers in VFDs
In Variable Frequency Drives (VFDs), rectifiers serve a crucial function by converting alternating current (AC) into direct current (DC). This process begins at the input stage of the VFD, where AC power, which cyclically changes direction, is transformed into DC power that flows consistently in a single direction. This transformation is achieved through the use of diodes within the rectifier circuit.
The most commonly employed rectifier configuration in VFDs is the three-phase bridge rectifier. This configuration is favored for its efficiency in handling high power levels typically encountered in industrial applications. Once the AC power is rectified into DC, the next step involves smoothing this DC voltage to minimize any residual AC ripple. Capacitors play a pivotal role in this stage, ensuring that the output voltage remains stable and consistent.
The stability of the DC voltage is critical for the subsequent stages of the VFD operation, particularly the inversion process. During inversion, the DC voltage is converted back into AC with the desired frequency and voltage parameters suitable for driving the connected motor. This entire process, from rectification to inversion, enables VFDs to precisely control motor speed and optimize energy efficiency in industrial settings.
You May Like to Read
Applications of AC to DC Conversion in VFDs
In variable frequency drives (VFDs), the process of converting AC to DC serves crucial roles across diverse industrial applications. One primary function involves the precise control of AC motors. By first converting alternating current (AC) into direct current (DC), and then back to AC with a variable frequency, VFDs enable meticulous adjustment of motor speed and torque. This capability proves indispensable in applications spanning conveyor systems, pumps, and fans within industrial settings.
Another pivotal application lies in regenerative braking systems. Here, VFDs play a pivotal role in converting the kinetic energy from decelerating motors back into electrical energy. This regenerated power can then be seamlessly reintegrated into the power supply system, markedly enhancing overall energy efficiency—a critical consideration in sustainable industrial practices.
Moreover, VFDs find extensive utility in renewable energy sectors, such as wind turbines. Here, they facilitate the conversion of variable frequency AC power generated by turbines into DC power. Subsequently, this DC power undergoes inversion to match the grid frequency, ensuring seamless integration with existing power systems.
Benefits and Challenges of AC to DC Conversion in VFDs
In industrial settings, the conversion from AC to DC within Variable Frequency Drives (VFDs) brings significant advantages, making it a pivotal technology for engineers to grasp. VFDs excel in precise motor control, enabling optimal speed and torque adjustments that lead to substantial energy savings. This efficiency not only reduces operational costs but also enhances overall process efficiency, crucial for maintaining competitiveness in today’s industrial landscape.
However, this conversion process isn’t without its challenges. One primary concern is the generation of harmonic distortions during operation. These distortions can degrade power quality, potentially causing disruptions in other connected equipment. Moreover, the initial investment required for VFDs can be considerable, necessitating careful financial planning. Furthermore, ensuring proper maintenance is essential to uphold VFD longevity and reliability, safeguarding against downtime that could impact production schedules.
Despite these challenges, the benefits of integrating VFDs into industrial operations far outweigh these drawbacks. They provide indispensable control over motor operations, contributing to both cost savings and improved productivity. For engineers entering the field, understanding these dynamics is crucial for harnessing the full potential of VFD technology in driving industrial innovation and efficiency.
By focusing on these fundamentals, engineers can navigate the complexities of VFD applications with confidence, leveraging their benefits while mitigating potential challenges effectively.
Technical Aspects of Conversion in VFDs
In Variable Frequency Drives (VFDs), the process of converting AC to DC begins with the rectifier stage. Here, the incoming AC power undergoes conversion into DC power. This DC voltage is then stored in capacitors, ensuring a consistent and stable power supply. Following this stage is the inverter, where the stored DC power is transformed back into AC. This conversion allows for varying both the frequency and voltage of the output AC waveform.
Key components involved in this stage include insulated-gate bipolar transistors (IGBTs) or metal-oxide-semiconductor field-effect transistors (MOSFETs). These components switch rapidly on and off under the control of a microcontroller or digital signal processor (DSP). This precise control is crucial for adjusting the speed and torque of the connected motor according to industrial requirements.
Advanced VFDs incorporate additional features such as regenerative braking, which enhances energy efficiency by redirecting energy back into the power supply. They also offer robust fault diagnostics and communication interfaces, facilitating seamless integration and monitoring within industrial systems.
This comprehensive control and versatility make VFDs indispensable in modern industrial applications, providing efficient motor control while ensuring operational reliability and energy savings.
Conclusion
In conclusion, the ability of VFDs to convert AC to DC is a fundamental aspect of their operation. This conversion process enables VFDs to provide precise control over motor speed and torque, leading to improved efficiency and energy savings in industrial applications. Despite the challenges associated with harmonic distortions and initial costs, the benefits of using VFDs in terms of energy savings, process control, and versatility make them an invaluable component in modern industrial systems. Understanding the power conversion process, the role of rectifiers, and the technical aspects involved is essential for engineers to effectively utilize VFDs in various applications.