Key Takeaway
A PLC control system is an industrial computer designed to control manufacturing processes. It is rugged and adapted for high reliability and ease of programming. PLCs manage tasks such as assembly lines, robotic devices, and machinery, ensuring smooth operation and process fault diagnosis. They receive input signals from sensors, process the data according to a pre-set program, and send output signals to actuators. This real-time control helps maintain efficiency and safety in industrial environments. PLC control systems are crucial for automation, reducing manual intervention, and enhancing productivity.
Definition and Components of PLC Control System
A Programmable Logic Controller (PLC) is a digital computer used for automation of industrial processes. PLCs are designed to manage complex tasks and can operate in harsh environments. They consist of several key components: the processor unit, power supply, input/output (I/O) modules, and programming device. The processor, often called the CPU, executes control instructions stored in its memory. I/O modules interface the PLC with the machinery, sensors, and actuators, ensuring seamless communication. The power supply provides the necessary energy, while the programming device allows engineers to write and download control programs.
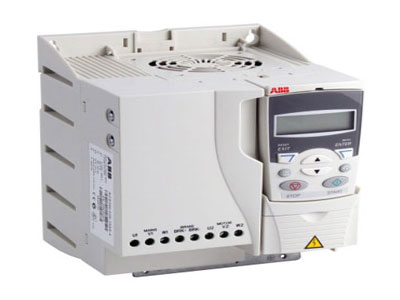
Functions of a PLC Control System
PLCs perform a variety of essential functions for industrial automation. At their core, PLCs execute control programs that manage machinery and processes. This involves several key tasks. First, they monitor inputs from various devices like sensors and switches, gathering real-time data about the system’s state. Based on this input data, PLCs make decisions according to pre-programmed logic, which can range from simple operations, such as turning a motor on or off, to more complex tasks, including managing sequential processes, timing, and counting events.
PLCs also control outputs to machinery and devices, ensuring that operations proceed as intended. Beyond basic control, they offer advanced features like diagnostics and data logging. These capabilities are crucial for monitoring system performance and troubleshooting issues. By logging data, PLCs help identify trends and potential problems before they lead to failures, improving maintenance strategies and operational efficiency. Overall, the versatility and reliability of PLCs make them indispensable in modern industrial automation, enabling precise and efficient control of complex systems.
You May Like to Read
Applications in Various Industries
PLCs are incredibly versatile and find applications in a wide range of industries. In manufacturing, PLCs control assembly lines, robotic devices, and machinery, ensuring efficient and precise operations. The automotive industry relies on PLCs for production lines and quality control systems, where they manage tasks such as welding, painting, and assembly with high accuracy. In the food and beverage sector, PLCs maintain consistent and safe production processes by controlling cooking times, mixing ingredients, and packaging products.
The chemical industry benefits from PLCs in process control, where they regulate temperatures, pressures, and chemical reactions to ensure product quality and safety. In the utilities sector, PLCs are crucial for managing water treatment plants, controlling the flow and treatment processes to ensure safe drinking water. They are also used in electrical grids to monitor and control the distribution of electricity, maintaining stability and efficiency. The adaptability of PLCs allows them to be customized for specific tasks, making them indispensable in industrial automation. Their ability to improve productivity, enhance safety, and ensure quality across various sectors highlights their critical role in modern industry.
Benefits of Using PLC Control Systems
Using PLC control systems offers numerous benefits that are essential for modern industrial operations. Firstly, PLCs provide high reliability. They are designed to operate in harsh industrial environments, withstanding factors like extreme temperatures, dust, and vibrations. This robustness ensures consistent performance and reduces downtime due to equipment failure.
PLCs are also highly flexible. Their programs can be easily modified to adapt to changing requirements, making them suitable for a wide range of applications. This flexibility extends to scalability, allowing systems to grow with the needs of the operation without requiring extensive overhauls.
Another key benefit is enhanced productivity. PLCs automate repetitive tasks, reducing human error and ensuring consistent quality. By automating complex processes, PLCs free up human operators to focus on more strategic tasks, improving overall efficiency.
Additionally, PLCs have advanced diagnostic capabilities that facilitate quick fault detection and troubleshooting. This minimizes downtime and maintenance costs, ensuring that production processes run smoothly. PLCs also support data collection and analysis, providing valuable insights for continuous improvement and decision-making.
Future Trends and Innovations
The future of PLC control systems is incredibly promising, with several exciting innovations on the horizon. One major trend is the integration of PLCs with Internet of Things (IoT) technology. This connectivity enables real-time data monitoring and remote control of systems, enhancing operational efficiency and reducing the need for on-site personnel. Imagine being able to oversee a factory’s entire production line from your smartphone or computer, making adjustments on the fly.
Artificial Intelligence (AI) and machine learning are also making their way into PLC systems. These technologies enable predictive maintenance by analyzing data patterns to predict equipment failures before they happen, thus reducing downtime and maintenance costs. AI can also help in optimizing processes by making smarter, data-driven decisions.
Another trend is the advancement in communication protocols. Improved protocols will enhance interoperability between different systems and devices, making it easier to integrate new technologies into existing setups. This means smoother, more cohesive operations across the board.
As technology evolves, PLCs will continue to be at the forefront of industrial automation. These advancements will not only make industrial processes more efficient and reliable but also open up new possibilities for innovation and growth in various industries. The future of PLCs is about smarter, more connected, and more efficient industrial automation systems.
Conclusion
In conclusion, PLC control systems are the backbone of modern industrial automation. They are essential for ensuring efficient, reliable, and flexible control of industrial processes. With their ability to operate in harsh environments, adapt to changing needs, and integrate with advanced technologies, PLCs are set to play a critical role in the future of industrial automation. Understanding their components, functions, and applications provides a solid foundation for engineers entering the field. As technology advances, staying updated with the latest trends and innovations in PLC systems will be crucial for maintaining a competitive edge in the industry.