Key Takeaway
Latching in PLC refers to a control method that keeps an output device on, even after the input signal is removed. When a momentary push button is pressed, a latching instruction activates and maintains the output in the ON state. This is useful for applications where continuous operation is needed, like keeping a motor running. To turn off the latched output, an unlatching instruction is used. Unlatching deactivates the output, stopping the motor or device. Latching and unlatching are essential for maintaining control states without requiring continuous input signals, enhancing automation efficiency in various industrial processes.
Definition of Latching in PLC
Latching in PLCs refers to a control mechanism that maintains the state of an output even after the initiating input signal is removed. In simple terms, once a latching circuit is activated, it stays on until it is explicitly turned off by another signal. This is akin to a light switch that stays on until you turn it off. Latching is used in scenarios where it is necessary to maintain a condition without continuous input signals, ensuring processes continue running smoothly without constant monitoring.
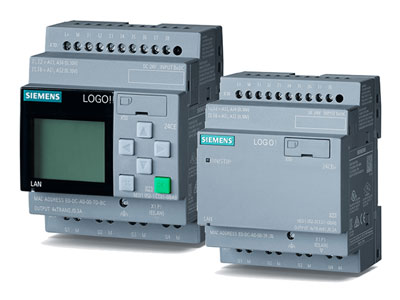
Latching Instructions and Logic
Latching instructions in PLC programming are vital for creating stable and reliable control systems. They typically involve two main commands: set (latch) and reset (unlatch). The set command activates the latch, causing the output to remain on even after the initiating input signal is removed. This means, for instance, that if you press a start button, the machine will continue running until a separate stop command is issued.
Conversely, the reset command deactivates the latch, turning the output off. This logic is crucial because it allows processes to maintain their states without needing constant input signals, which is essential in maintaining continuous operations in an industrial setting. For example, a conveyor belt can keep moving even if the initial signal is no longer present, stopping only when explicitly commanded to do so.
Ladder Logic, one of the most common PLC programming languages, visually represents these latching mechanisms. This visual representation helps engineers easily design, troubleshoot, and modify control systems. By understanding and implementing latching instructions, new engineers can create more efficient and dependable automation processes, ensuring that machinery operates smoothly and effectively without unnecessary interruptions. This clarity and control are fundamental in industrial automation.
Applications of Latching in Industrial Processes
Latching mechanisms are essential in maintaining operational continuity in various industrial processes. For instance, in manufacturing, a latching circuit can keep a machine running until a specific task is completed, even if there are temporary interruptions in the control signal. This ensures that processes are not disrupted by minor signal fluctuations, leading to higher efficiency and productivity.
In conveyor systems, latching is used to ensure that conveyors continue moving materials until they reach their destination. This mechanism reduces the need for manual intervention, streamlines operations, and enhances overall efficiency. It ensures that the conveyor system operates smoothly, even if there are temporary lapses in the input signal.
Latching is also crucial in safety systems. For example, alarms or emergency stop conditions are maintained until the issue is resolved and manually reset. This ensures a safe working environment by preventing machinery from restarting automatically after an emergency stop. It provides an additional layer of safety, as the system remains in a safe state until an operator intervenes.
These examples highlight the importance of latching in ensuring seamless, efficient, and safe industrial operations. Understanding and implementing latching mechanisms can significantly enhance the reliability and effectiveness of various industrial processes.
Differences Between Latching and Non-Latching Circuits
Understanding the difference between latching and non-latching circuits is crucial for designing effective control systems. The primary distinction lies in how these circuits respond to input signals.
Latching circuits maintain their state even after the initiating signal is removed. Once a latching circuit is activated, it remains in that state until it receives a reset signal. This feature is particularly useful in applications where it is essential to keep an output active without continuous input, such as keeping a motor running or maintaining an alarm state until manually turned off.
On the other hand, non-latching circuits only stay active as long as the input signal is present. Once the signal is removed, the output immediately returns to its original state. This characteristic is suitable for processes requiring immediate cessation of operation when the input is no longer available, such as a light that turns off when a button is released.
The choice between latching and non-latching circuits depends on the specific requirements of the application. Latching circuits offer sustained control, ideal for ongoing operations, while non-latching circuits provide immediate responsiveness, suitable for temporary actions. This distinction is essential for engineers to design systems that meet the precise needs of industrial automation, ensuring both efficiency and safety.
Examples of Latching in PLC Programs
Latching is a fundamental concept in PLC programming, and one common example is the start/stop control circuit for a motor. Imagine you have a motor that needs to run continuously once started. When you press the start button, a set instruction is triggered, latching the motor’s output. This means the motor will keep running even after you release the start button. It will continue to run until you press the stop button, which triggers a reset instruction to unlatch the output and stop the motor. This setup is essential for processes that require uninterrupted operation until a task is completed or manually stopped.
Another practical example is an emergency stop system. In this scenario, an emergency stop button, when pressed, activates an alarm that stays latched. This alarm will remain active until the issue that caused the emergency is resolved. Only after the problem is addressed can the alarm be manually reset, ensuring that the system does not resume operation until it is safe. This type of latching mechanism is crucial for maintaining safety in industrial environments, providing a fail-safe that requires human intervention to clear and reset.
These examples demonstrate how latching ensures continuous operation and safety in industrial processes, highlighting its importance in PLC programming.
Conclusion
Latching plays a critical role in PLC automation, providing the ability to maintain control states without continuous input signals. This functionality is essential for ensuring the smooth and efficient operation of industrial processes, reducing the need for constant monitoring and manual intervention. By understanding and effectively implementing latching mechanisms, engineers can design robust and reliable control systems that enhance productivity and safety in various industrial applications. As a fundamental concept in PLC programming, mastering latching logic is crucial for anyone involved in industrial automation, ensuring that processes run smoothly and efficiently.